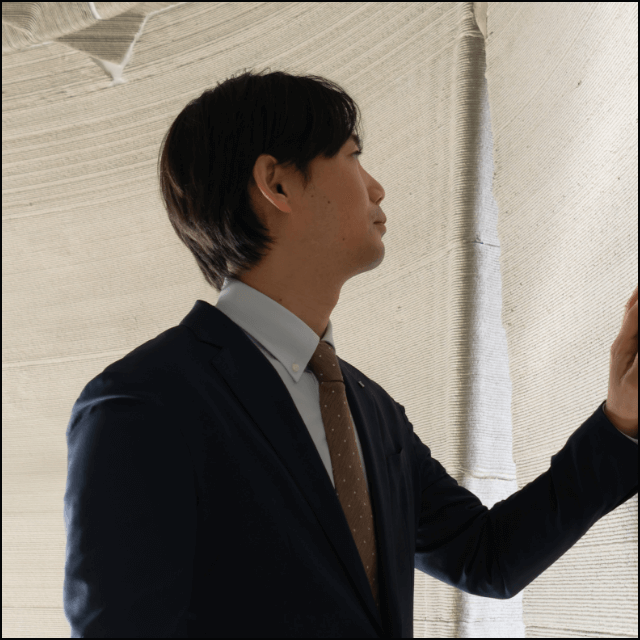
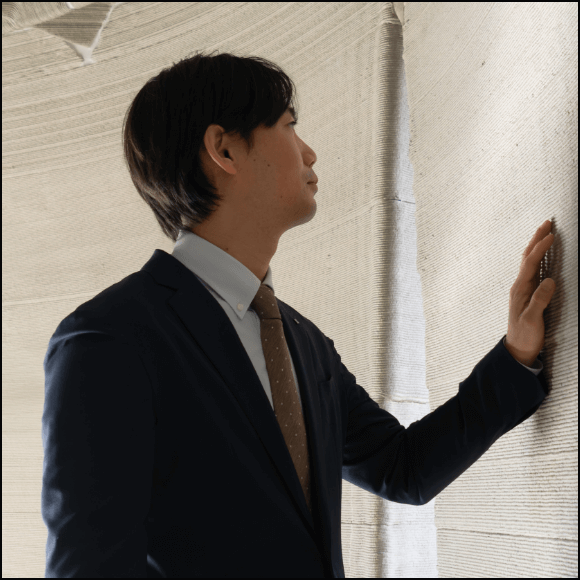
Project Leader
生産技術研究部 課長
坂上 肇
Hajime Sakagami
入社後、建設作業の自動化・省力化に関する技術開発に従事し、現在は、建設用3Dプリンターや耐火被覆吹付けロボットの開発に取り組む。粘り強さとトライ&エラーの繰り返しで課題解決に挑んでいる。
入社後、建設作業の自動化・省力化に関する技術開発に従事し、現在は、建設用3Dプリンターや耐火被覆吹付けロボットの開発に取り組む。粘り強さとトライ&エラーの繰り返しで課題解決に挑んでいる。
建設業界における3Dプリンターの活用範囲は拡大している。省人化、多品種少量生産、複雑なデザインの実現など、従来の建築プロセスを変革する技術といえるだろう。国内で初となる地上構造物のすべてに3Dプリンター製の部材を使用した「3dpod」はその顕著な事例。プロジェクトを担当する坂上肇研究員が見据える未来の建築とは。
About Project
3Dプリンター建築物として国内初の大臣認定を取得した「3dpod」
3Dプリンターとは材料を重ねていくことで立体物をつくり出す機械のことです。3Dモデルさえあれば誰でも簡単にものづくりができるため、近年さまざまな業界で普及が進んでいます。材料はプラスチックが一般的ですが、建設分野では強度や耐久性が求められるため、主にセメント系材料であるモルタルを使用したものが、建設用3Dプリンターとして盛んに研究されています。自動化、機械化による省人化、一品(多品種少量)生産への対応、複雑な形状をした構造物の実現など、建設業界における3Dプリンターへの期待は日に日に高まっているといって間違いないでしょう。
建設用3Dプリンターは2002年頃から米国で研究が始まり、2016年頃から活発に論文発表が行われてきました。大林組でも2014年に次世代技術として検討を開始、2017年に3Dプリンター用モルタルを開発しモルタルアーチ橋を製作しました。2019年には大林組の保有技術である常温硬化型超高強度繊維補強コンクリート「スリムクリート®」を導入しシェル型ベンチを製作、2022年に国内初となる国土交通大臣認定による建築確認を取得した建築物として「3dpod」の建設を開始し、2023年3月に竣工しました。
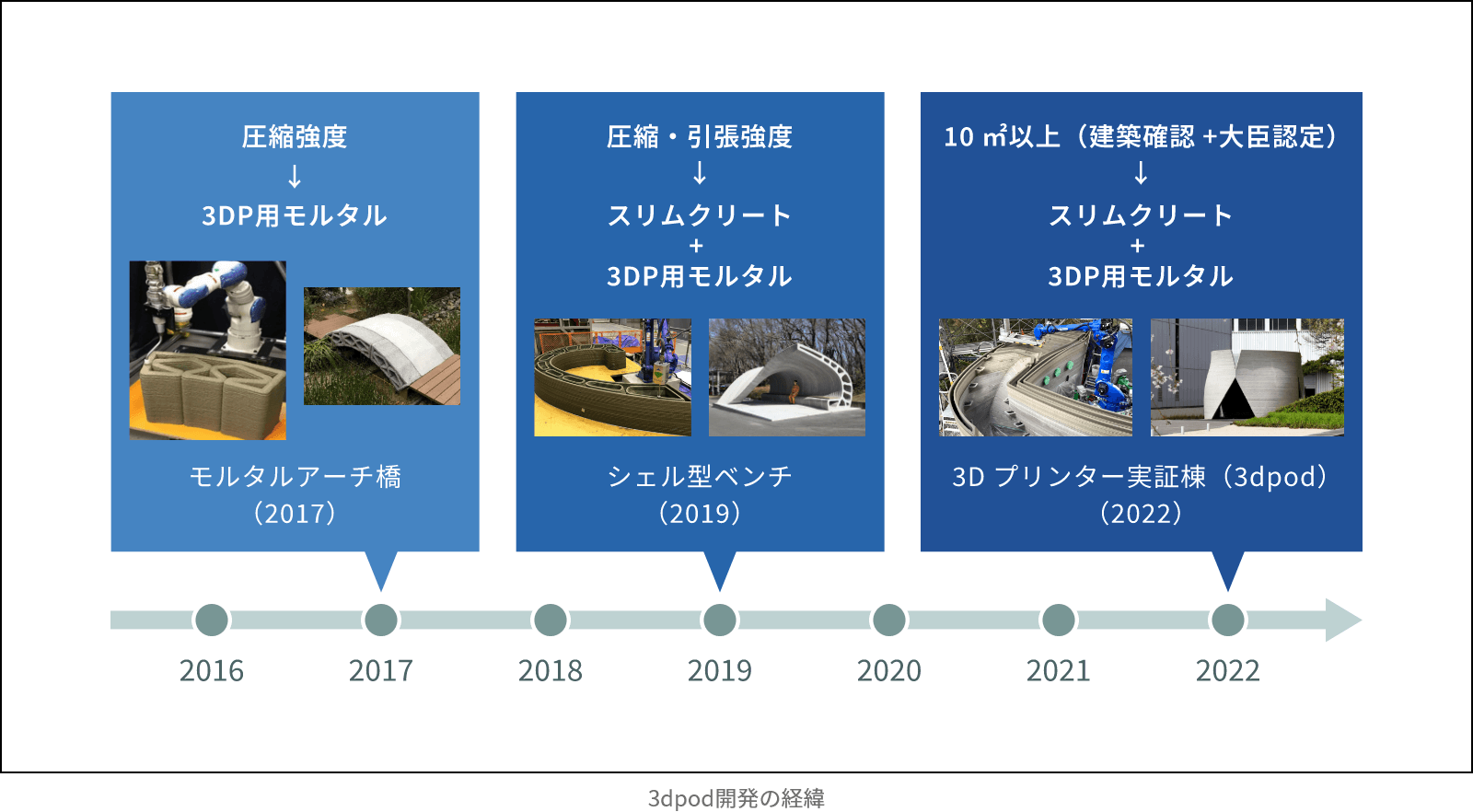
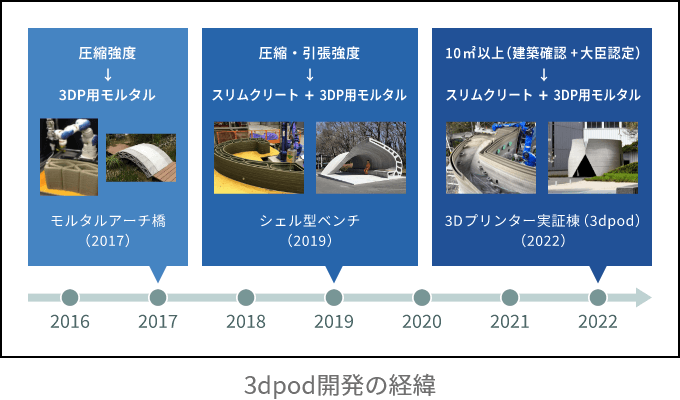
私が開発に携わった「3dpod」の画期的な点は以下の3点です。1つ目は「国内で初めて地上構造部材をすべて 3Dプリンターにより建設」したことです。建設地に建設用3Dプリンターを据え付け、3Dプリンター用モルタルで壁の外殻部をプリントします。そして、その内部に「スリムクリート」を流し込んで構造体となる壁を構築します。床版もあらかじめプリントしたデッキを架設してから、「スリムクリート」を流し込む構造形式とし、すべての地上構造部材を3Dプリントにて製造しました。この新しい構造形式で建築基準法に適合した建築物を建設。形状の自由度や施工の省力化などを実現しています。
2つ目は「3D プリンターの特長を活かした曲面形状の構造床と複層壁」です。複雑な曲面形状の部材を製造できる3D プリンターの特長を活かし、床版に生じる力が分散するように、突起(リブ)で床版を補強しています。また、電気・空調・衛生などの設備も実装するため、壁は構造体層・断熱層・設備層(空調ダクト層)からなる複層構造としています。3D プリントによる躯体工事と同時に断熱、設備工事の一部を行うことで工期短縮および省力化を実現しました。
3つ目は「3D プリンターによる施工に合わせた設計フローを整備」したことです。本プロジェクトでは、建築・構造・設備の各設計と施工を連携するために、3次元で製造したモデルを一貫利用した設計・製作フローを構築するとともに、プリント経路の自動生成や傾斜部の積層性、障害物との干渉状況を確認するソフトウェアを開発しました。これにより、デザインされた形状に、建築物として必要な情報を付加し製作するまでの時間を短縮することを可能にしました。
今後はさらに複雑なデザインや強度・耐久性を備えた構造物を実現できるセメント系材料を用いた建設用3D プリンター建設の研究を進め、実用化を推進していきます。
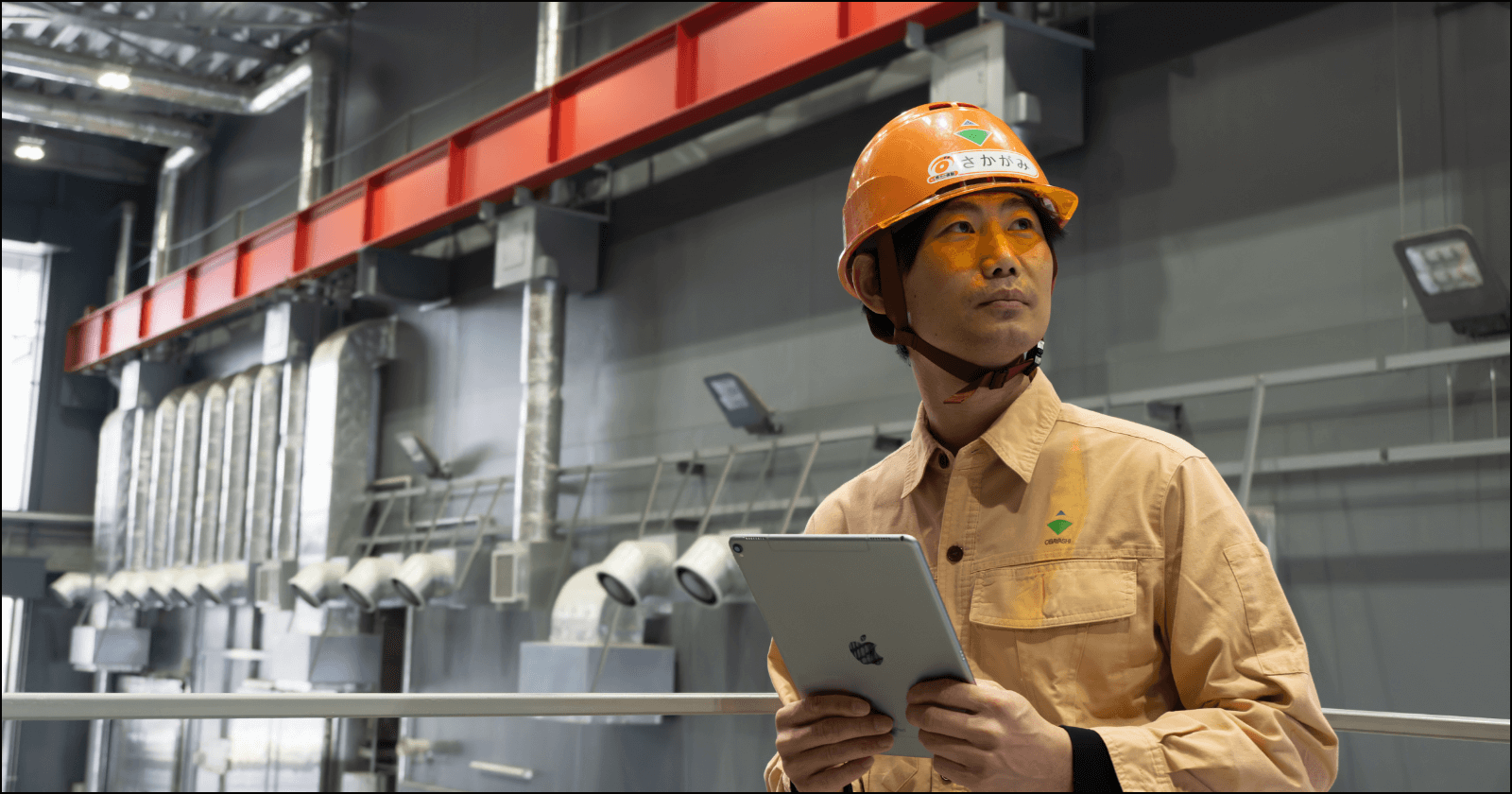
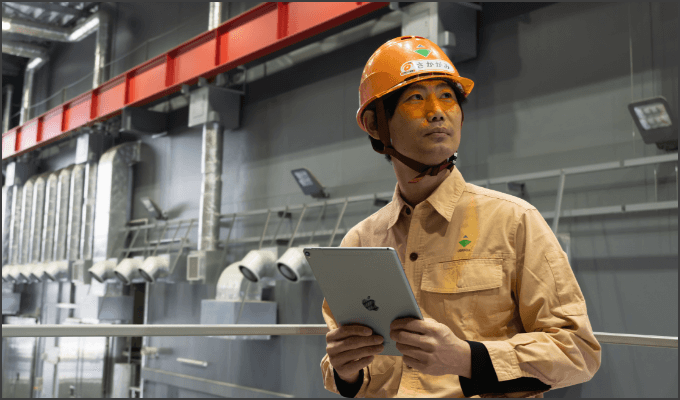
Story
材料から工法へ、段階的に3Dプリントの課題を解決
私は入社後、ロボットアームを使用する研究開発に従事していた関係から、同じくロボットアームを使用する3Dプリンター関連のプロジェクトに参画していきました。
前述したように大林組における3Dプリンターの活用は2014年に机上検討が始まり、2017年に材料メーカーと3Dプリンター用モルタルを開発し、これを用いた小規模部材の製造を開始します。最初に製作したのが圧縮力に強いセメント系材料の特性を活かしたアーチ構造のモルタルアーチ橋です。この時はアームの長さが1mの小型3Dプリンターでモルタルブロックを製作し、アーチ状にして建造しました。私はこのロボットアームの制御に従事していました。
2019年に完成したシェル型ベンチ以降は開発を主導する立場で開発を進めてきました。このシェル型ベンチでは、3Dプリンター用モルタルと超高強度繊維補強コンクリート「スリムクリート」とを一体化する複合構造、そして独自の積層制御技術および大型ロボットアームを用いた3Dプリンターを開発しました。モルタルアーチ橋で解決できなかった引張力を負担するため「スリムクリート」を導入したシェル型ベンチは、セメント系材料を用いた3Dプリンターとして当時国内最大規模となる構造物(幅7m、奥行き5m、高さ2.5m)でした。3Dプリンターとスリムクリートの両者の特長を活かした複合構造を考案し、建築物レベルの大型構造物を製作できたことは大きな成果でした。
2022年からは3Dプリンター建築物の設計施工に関する知見の収集を目的に建設した「3dpod」の開発を進めてきました。プロジェクトの進行にあたっては社内外の関係者の協力を得て、国内で初めて建築基準法に基づく国土交通大臣認定を取得しました。施工当初は、屋外の気候に左右されるなどの苦労もありましたが、多くの知見を収集することができました。
開発当初の課題は、3Dプリンターで積層できる材料開発が中心でしたが、その後、引張力の負担方法が課題となり、「スリムクリート」との複合工法を考案。また、さまざまな試行と適用を繰り返すことでより自由度の高い形状を実現するためのプリント方法を開発することができたと考えています。それらノウハウを活用することで、複数階や面積規模を拡大した構造物の建設につなげるとともに、将来的には3Dプリンターによる宇宙空間での建設など幅広い可能性を追求していきたいと考えています。
加速する3Dプリンターの
活用事例
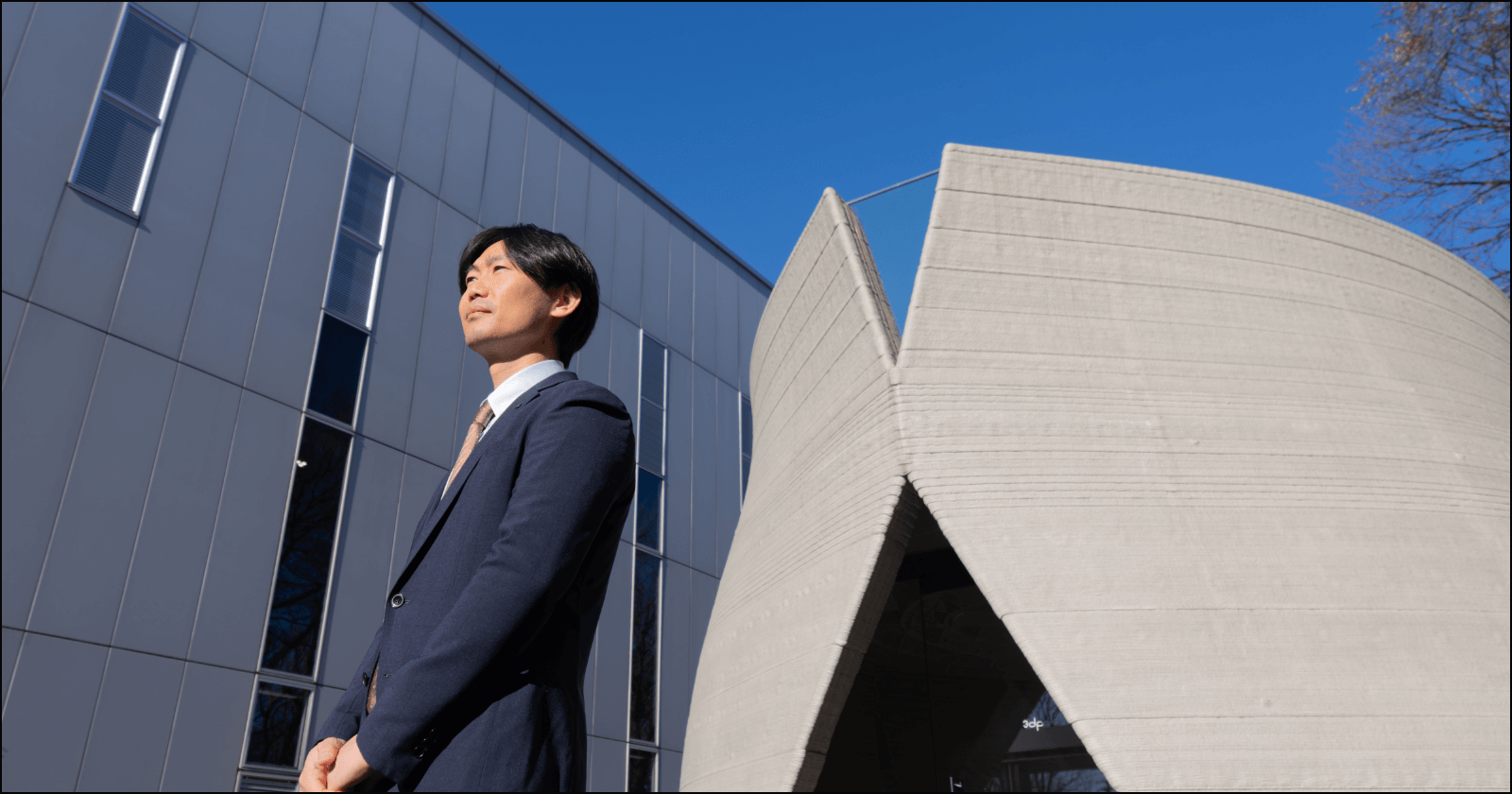
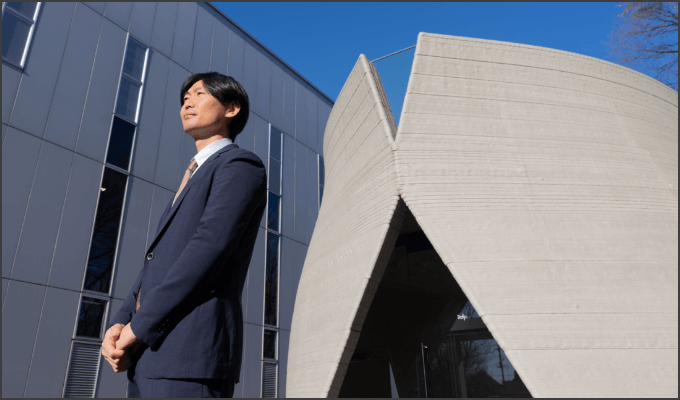
「3dpod」の竣工以後、3Dプリンターはさまざまなシーンで活用され始めています。2023年11月には神奈川県の西湘海岸岩盤型潜水突堤整備工事おいて、砂浜を侵食から守る岩盤型潜水突堤の一部を3Dプリンターで製作しました。これは3Dプリンターで製作したプレキャスト部材を大型構造物に適用した国内初の事例です。
2024年3月に竣工した横浜シンフォステージでは、広場のベンチを3Dプリンターで製作。白鯨の動きを手掛かりにデザインされたユニークな形状は3Dプリンターの高度な技術により実現されたもので、塗料や足元の舗装部には低炭素化を実現した材料を使用するなど、最新の環境配慮技術も組み込まれています。
2024年12月には新丸山ダム建設工事において、擁壁工事に3Dプリンターを活用したプレキャスト部材を適用し、工程を約30%短縮することができました。これらの事例の他にも適用が進んでいます。
3Dプリンター建設の最も難しい点は、従来の建設プロセスと異なり、前例がないことです。前例がないものを確実に実現するためには、関係各所との連携や入念な試行が欠かせません。また、新たなプロジェクトに携わるたびに少しずつでも新たなチャレンジを取り入れ、技術を進展させるように心がけています。
私の直近の目標は、建設用3Dプリンターを特殊形状や省ロット部材のプレキャストコンクリートの製造技術の一つとして確立することです。その後、自動化率を高めて3Dプリントの適用範囲を拡大することにつなげていきたいと考えています。より複雑なものを安定的にプリントするための技術は、まだまだ開発する余地はたくさんあります。工法の選択として普通に3Dプリンターが候補に挙がる日は確実に近づいています。
Project Development
オープンラボ2
「コンクリート実験スペース」
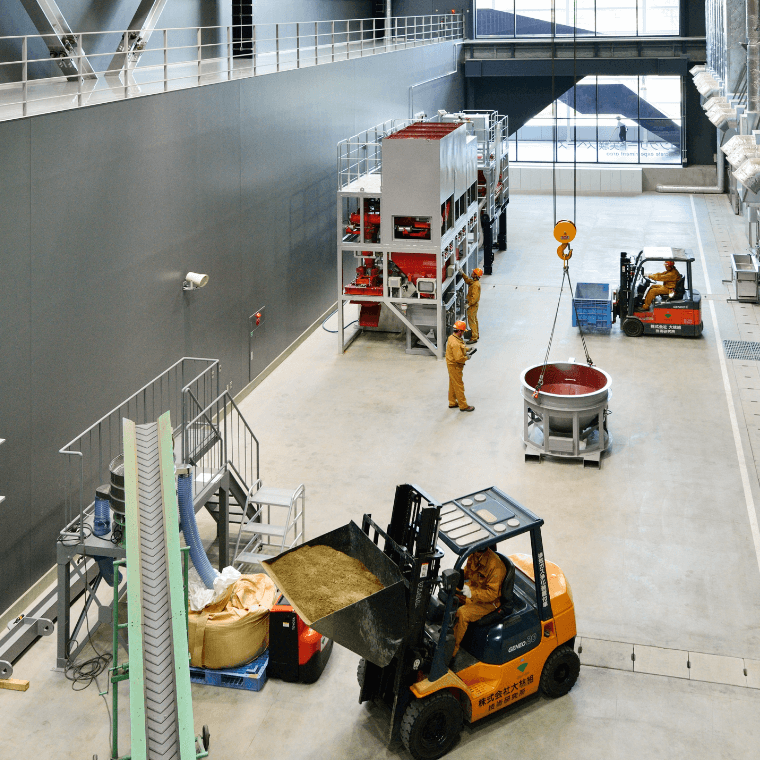
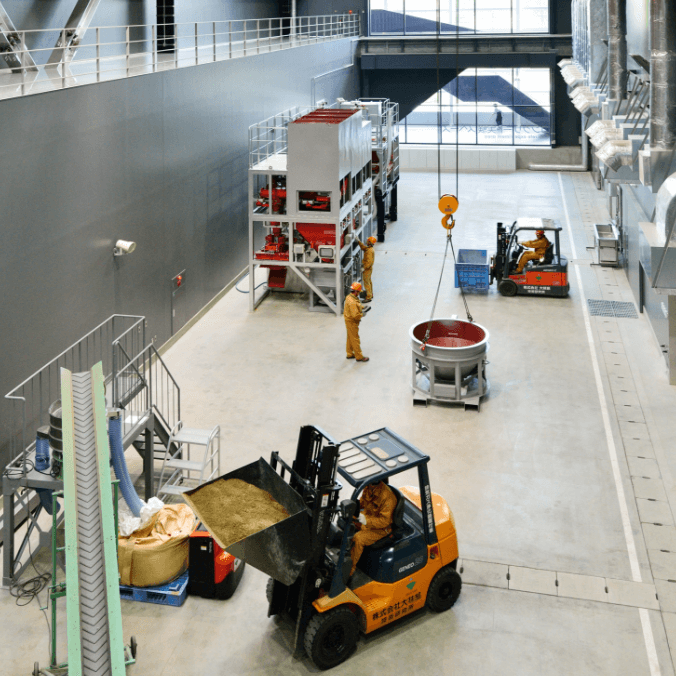
3Dプリンターの実証棟である「3dpod」の建設には、W10m×L45m×H10mの大空間「コンクリート実験スペース」を活用し、実大サイズの部材の施工試験を行いました。ロボットアームに取り付けたノズルから3Dプリンター用モルタルを吐出・積層して自動で3Dプリント。従来の型枠では製造が難しかった部材の製造を研究し、「スリムクリート」との複合構造も試験することで、3Dプリンターの可能性をさらに広げることができました。