- 4 Technology
- Technology Development
Underwater Infrastructure Inspection Robot DIAG
Development of underwater infrastructure inspection robot DIAG™ equipped with AQUAJUSTER®
Takes clear images without blurring by using stabilization technology underwater
OBAYASHI CORPORATION has developed the underwater infrastructure inspection robot DIAG which is equipped with AQUAJUSTER and is able to take clear images underwater.
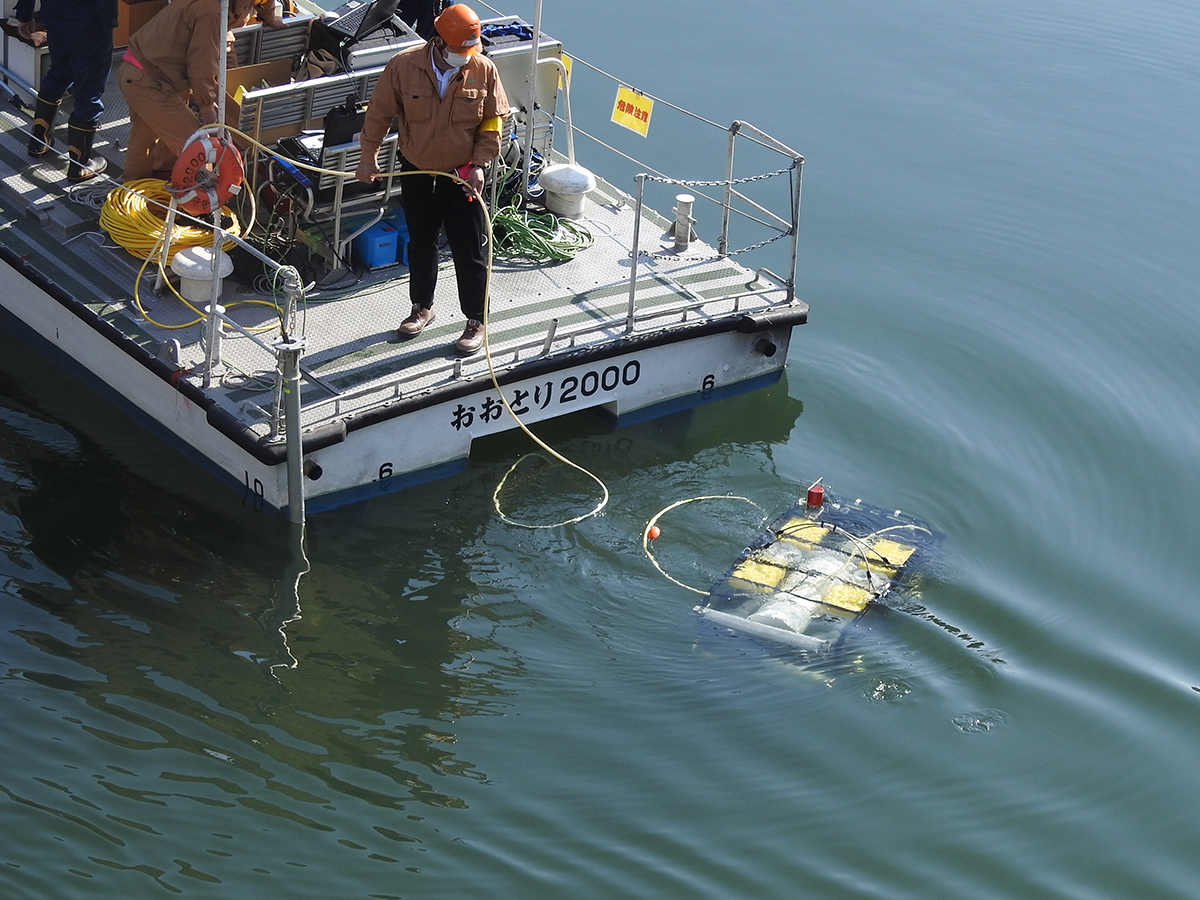
Japan’s infrastructure was developed intensively during its high-growth period and currently most of it is becoming increasingly decrepit and structures such as dams are also in urgent need of update and repairs to extend their service life. In repairing projects for underwater structures such as dams and seawalls, it is necessary to investigate whether there are any cracks and the extent of any cracking, etc. in advance.
Previously, divers went underwater to inspect the structures visually and take photographs, etc. But there are restrictions on work hours and limits to diving depth with underwater work by people, so the development of robots to carry out continuous inspections safely was eagerly anticipated.
The DIAG now developed by Obayashi Corporation is a Remotely Operated Vehicle (ROV) for underwater inspections for which remote operation from land or ship is possible. The frame is equipped with the attitude control system AQUAJUSTER which uses the gyro effect, so it controls the shaking of the frame caused by water flow and is able to take photos of physical objects in a stationary state.
Furthermore, with inspections by divers, a diving depth of approximately 40 m was the limit, but DIAG is capable of diving up to 100 m, and it can continue operating for a long time using a power supply from above the water.
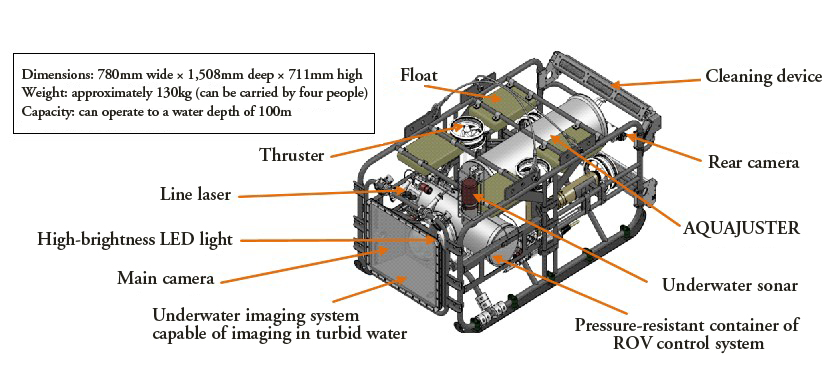
DIAG was adopted under the "robot technologies and robot systems for next-generation societal infrastructure" program by the Ministry of Land, Infrastructure, Transport and Tourism, and as a result of multiple demonstrations DIAG obtained a top-ranked evaluation.
The features of DIAG are as follows.
-
Clear images due to outstanding stabilization and image analysis underwater
DIAG is equipped with AQUAJUSTER, so it can use the gyro effect to control the shaking of the frame caused by water flow and is able to take photos of physical objects in stationary state. Furthermore, images photographed with the frame’s hi-vision camera are displayed on the monitor after the underwater white suspended solids, etc. have been automatically removed by image analysis, so it is possible to see clear images in real time even in turbid water.
Image before image analysis Image after image analysis -
Safe inspections using simple remote operation are possible from land or ship
There are restrictions on work hours for inspections by divers. For example, in the case of a water depth of 40 m, divers can only continuously work for a few minutes. Divers advance their inspections while taking the prescribed rest, but the danger of decompression sickness inevitably accompanies this work.
On the other hand, this danger does not exist for inspections using DIAG because the frame is remotely operated with a controller from land or ship. It can be operated so easily that there is no need to have a qualification to operate it. Furthermore, DIAG can continue operating for a long time by receiving a power supply from a power generator on a working ship.
Underwater infrastructure inspection robot DIAG Controller -
Can reach the inspection site and record accurate position information in a short time
Divers go toward inspection sites while measuring the distance from the base point at their current position, but underwater gets darker with greater depth, and there are cases in which visibility becomes poor due to the turbidity of the water, so it takes time to reach the inspection sites. With inspections using DIAG, the frame’s position information can be accumulated in real time using surveying instruments installed on the land and transponders installed on working ships, so it is possible to reach the inspection sites in a short time.
Furthermore, it is possible to measure the dimensions of the cracking, etc. by irradiating the cracking, etc. with a line laser from the frame, and to utilize the frame’s position information to record the positions where there is cracking.Currently, Obayashi Corporation is upgrading DIAG so that it can move in parallel and record while facing the wall surfaces of dams, with a view to the creation of mosaic maps which can confirm the status of the overall structure of dams at a glance.
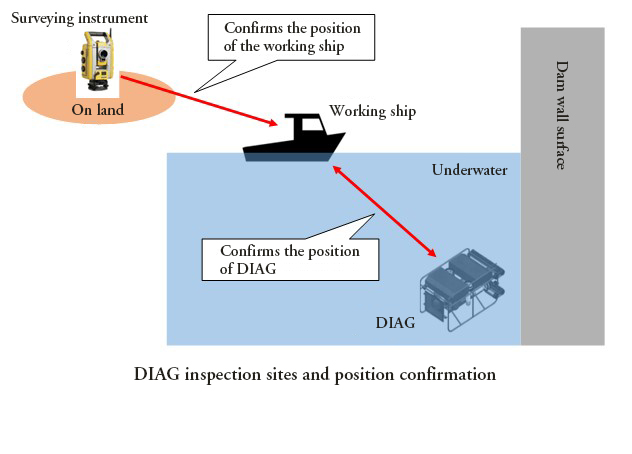
Unique technology possessed by Obayashi Corporation that uses the gyro effect (the effect that the posture is less likely to be disturbed by the rotation of the object) and controls the direction of the suspended load during lifting work underwater. In the construction work for TOKYO SKYTREE®, which was constructed by Obayashi Corporation, we used the SKYJUSTER, which has the same kind of function, to control the suspended loads of tower cranes which shake (rotate) due to the effect of wind.
An injury which occurs due to the decompression process after diving. Also called decompression sickness, there are symptoms such as pain in the joints of the limbs, choking, and immobility.
A radio repeater used in wireless communications, etc. It sends response signals (sound waves) from the working ship and listens to the reply signals (sound waves) from DIAG underwater. It measures the distance between the working ship and DIAG from the round-trip time of the sound waves and the underwater speed of sound.
- Management and
Organization- The Articles of Incorporation
- Basic Principles
- Transitioning of Corporate Symbol
- Corporate Officers
- Organization Chart
- Stock Information
- Financial Statements
- Technology
- BIM Timeline
- Awards
- Major Publication
- Group Companies
- Group Companies (in Japan)
- Group Companies (Overseas)