- 4 Technology
- Technology Development
3D Printers Using a Special Cement Material
Development of a 3D printer that uses a special cement material as ink
Automatic and accurate manufacturing of members of various shapes without using forms
Obayashi Corporation has developed a 3D printer that uses a special cement material as ink to enable the automatic manufacturing of building and civil-engineering-structure members without using forms.
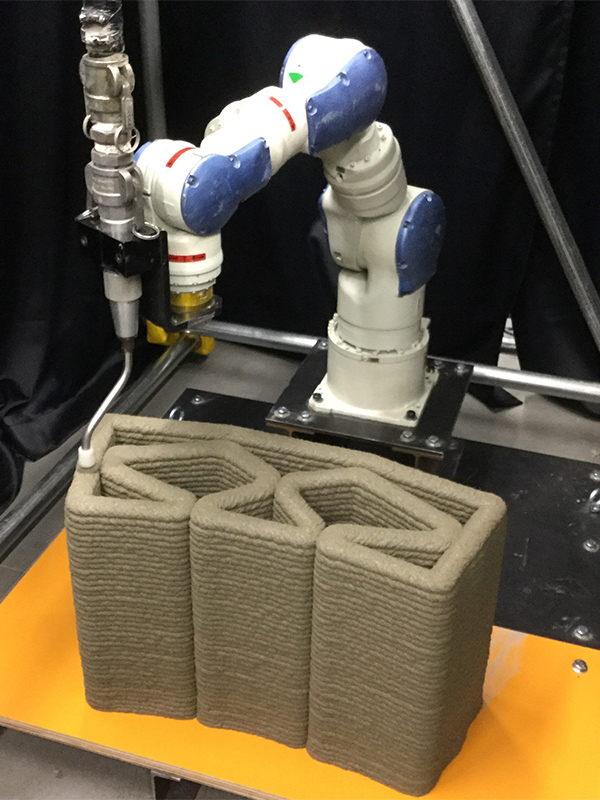
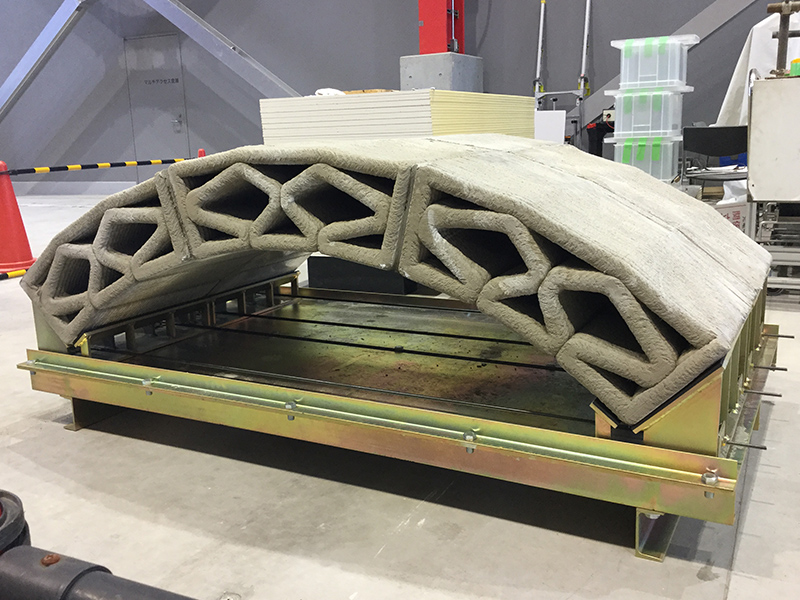
In recent years, the use of 3D printers has been expanding—including additive manufacturing using plaster, resin, and various other materials as ink—but, in the Japanese construction industry, such printing has really only been used to model buildings, and it has not reached the level of constructing actual buildings or civil engineering structures.
In general, concrete and many other cement materials are used for buildings and civil engineering structures, but, because it takes a certain amount of time for such materials to reach sufficient strength, forms are necessary to maintain the prescribed shapes and dimensions, which has been one of many issues related to the use of 3D printers.
However, our recently developed 3D printer discharges ink from a robot arm to achieve additive manufacturing, thereby making it possible to automatically manufacture building and civil-engineering-structure members.
The ink is a special cement material jointly developed with Denka Company Limited (https://www.denka.co.jp/eng/). Because the material possesses the strength and durability necessary for buildings and civil engineering structures, and it does not lose its shape immediately after being discharged, it can be used to manufacture structural members without using forms.
It took a lot of time and effort to manufacture a member having a complicated shape including a curved surface and a hollow with a cement material. This development has made it possible to manufacture it automatically.
Obayashi Corporation has used this 3D printer to print hollow curved mortar-blocks, and actually succeeded in manufacturing an arch-shaped bridge by combining them.
Feel free to check out our video of mortar-block manufacturing using our 3D printer.
The features of our 3D printer that uses a cement material are described below.
-
Manufacturing members with various shapes without using cement forms
When using general cement materials, because it takes a certain amount of time for the materials to reach sufficient strength, it is necessary to install forms. However, because our new cement material is thixotropic, no forms are necessary. It does not lose its shape immediately after being printed, integrates with the lower layer, and hardens in a short time. As a result, our 3D printer does not require form assembly and disassembly work that requires a lot of time and effort, especially when manufacturing curved and hollow shaped members.
Looking to the future, we are also considering how to take advantage of the features of our 3D printer—which can handle the additive manufacturing of various designs—to apply it to the manufacturing of biomimetic-based structures characterized by light, strong frames as well as form-optimization-based structures.
-
Automatic and accurate printing materials via offline teaching
Our 3D printer features a seven-axis robot arm with a material-discharging nozzle attached to its tip. Because the nozzle is controlled via offline teaching to accurately move along a prescribed path at a certain speed, materials can be automatically and accurately used for additive manufacturing. To manufacture the arch-shaped bridge, we printed hollow mortar blocks that were 500 mm wide x 250 mm deep x 500 mm tall in around 15 minutes.
Arch-shaped bridge installation situation
The property of a substance to have fluidity when under pressure but to become viscous when this is no longer the case and to then harden and maintain its shape. The cement material used by our 3D printer has fluidity while under pressure before it reaches the discharging nozzle, and then it hardens in a short time after being discharged.
A design methodology that involves imitating the structures of living things for purposes that include applying lightweight, durable frames to structures, etc.
A method of analyzing the optimal form for given load conditions.
A method of teaching operations to robots by inputting work programs into a computer without using an actual machine. If the work details are modeled, this offers the advantage of better work accuracy compared to teaching using an actual machine.
- Management and
Organization- The Articles of Incorporation
- Basic Principles
- Transitioning of Corporate Symbol
- Corporate Officers
- Organization Chart
- Stock Information
- Financial Statements
- Technology
- BIM Timeline
- Awards
- Major Publication
- Group Companies
- Group Companies (in Japan)
- Group Companies (Overseas)