- 4 Technology
- Technology Development
Our Machine Guidance System Facilitates Crane Operation
We developed a Machine Guidance System that facilitates safe, efficient crane operation.
Obayashi Corporation has developed a Machine Guidance System that facilitates safe, efficient crane operation by utilizing BIM (Building Information Modeling) to create 3D models of construction sites and then linking with information from sensors attached to cranes to display information on the crane situation in real time for operators.
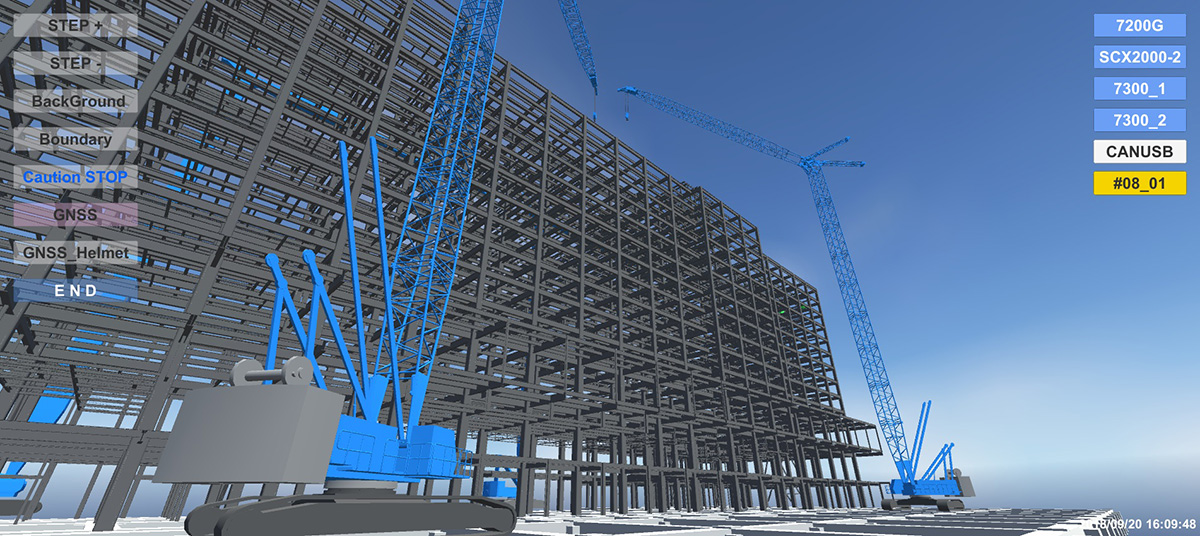
Operators who operate cranes to do lifting work at construction sites must be extremely careful about potential collisions between cranes, contact with nearby structures, interference with paths for important radio communications, violations of height limits based on the Civil Aeronautics Act, crossing property lines, and similar issues. Conventional equipment regulated in terms of work range also has functions that warn operators when the equipment approaches the range over which work is prohibited, but—because the screens confirmed by the operator display information in 2D—it is difficult to understand the height, which was an issue.
In addition, in cases where the operator was inexperienced or had poor visibility due to blind spots, bad weather, or other issues, the operator had to more frequently communicate with workers via radio, which sometimes necessitated interrupting the work and ran the risk of reducing work efficiency.
However, with our recently developed Machine Guidance System, 3D models are used to enable the operator to confirm the crane situation from any point of view, making it possible for the operator to make decisions as if they can see everything even in the case of blind spots and similar issues. In addition, the system features a function that displays guidance on the necessary operation amount to safely transport lifted members to the attachment position.
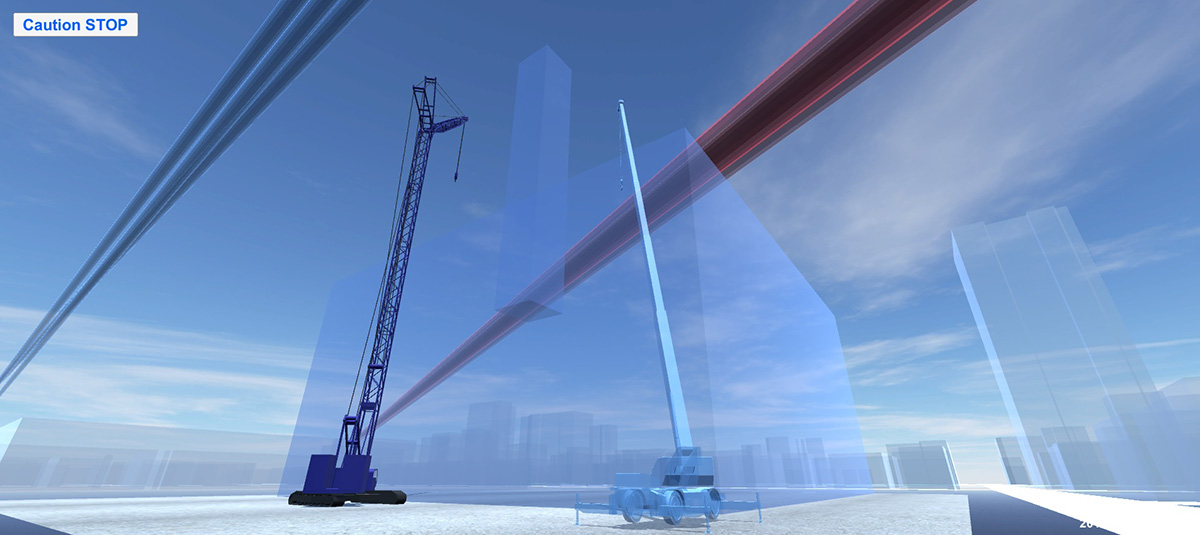
In recent years, there has been an active trend in the manufacturing industry and elsewhere for craftsmanship to evolve due to cyber-physical systems (called CPS below), and our system incorporates the idea of CPS to achieve an information-oriented system that fuses 3D models of the construction site in cyberspace with the actual movement of the crane.
The features of our Machine Guidance System are described below.
-
Safety is greatly improved by displaying crane movement and construction site information in 3D
Crane movement information acquired from wireless sensors is fused with 3D models of the construction site, and then the result is displayed on a touch screen in the crane control room. The 3D models utilize BIM to display not only the construction target and surrounding structures but also to visualize things that cannot be seen, such as radio paths, height limits based on the Civil Aeronautics Act, and property lines.
With our system, the operator can confirm bird's-eye images of the crane—which they cannot normally see—as well as the position of the crane relative to its surroundings from any point of view by performing touch screen operations. This complements the information the operator can obtain by eye to help enable safe crane operation even when there are blind spots or visibility is poor, such as at night or when the weather is bad. In addition, warnings are displayed on the screen to help prevent the crane from entering the range over which work is prohibited.Touch screen installed in the control room AI is also utilized to confirm the situation under the crane, which cannot be applied to 3D models. Based on images from a camera installed so that it faces down from the crane, AI is used to further improve safety by recognizing the positions of the crane hook and boom as well as workers and then issuing warnings when dangerous situations are detected, such as contact between the suspended load and buildings or workers being directly below the suspended load.
AI-based image recognition of the situation below the crane -
The system enables efficient, accurate work regardless of the experience of the operator
When the attachment position of the member to be lifted is selected on the screen, the crane operation amount relative to the current position is quantified and then linked to the crane's movement and displayed on the screen in real time. Guidance that is accurate to within an error level of several centimeters can also be provided, including the coordinates of the attachment position of the member to be lifted, which are based on the BIM design information, the movement of the crane, which is based on gyro sensors attached to the tower and jib (both of which detect changes in the angle), and the crane position, which is acquired using RTK-GNSS.
Because even an inexperienced operator can operate a crane by referring to the operation amount displayed on the screen, the frequency of radio communication to provide instructions on the transport position can be reduced, which helps enable safe, efficient work. Our system is therefore effective for resolving the problem of operator shortages because—even in the absence of experienced operators—work can easily be done at construction sites where the range of possible work was once limited.Quantification and display of the operation amount necessary to reach the member attachment position -
Easy to attach regardless of the crane model
In the case of conventional equipment regulated in terms of work range, each crane had its own specially designed system, so it was difficult to use such systems for other cranes, and the systems were large and therefore necessitated a lot of effort to do the attachment work. With our system, the sensors that acquire the crane position, tower and jib angle, and turning angle information are set up as a unit, which means their design enables them to be easily retrofitted to any crane regardless of its model.
Thanks to the portable size of each unit, attachment to a crane is as easy as tightening bolts and connecting wiring cable, so no special tools or skills are required. This results in installation costs that are lower than those of conventional equipment regulated in terms of work range.Sensor units attached to a crane
With CPS, information acquired by sensors in the real (physical) world is collected via a network, and then this information is processed, analyzed, and converted to knowledge in virtual space (cyberspace) set up on a computer. The information, calculated values, and estimated values are then applied to the real world.
This GNSS (global positioning) system is used to acquire highly accurate position information (with an error of only centimeters) in real time based on the relative positioning of nearby reference stations for which the positions are known.
- Management and
Organization- The Articles of Incorporation
- Basic Principles
- Transitioning of Corporate Symbol
- Corporate Officers
- Organization Chart
- Stock Information
- Financial Statements
- Technology
- BIM Timeline
- Awards
- Major Publication
- Group Companies
- Group Companies (in Japan)
- Group Companies (Overseas)