- 4 Technology
- Technology Development
Composite Structure That Combines 3D Printer Mortar with Slim-Crete
We have developed a composite structure that combines special 3D printing mortar with ultra-high-strength fiber-reinforced concrete in order to use cement materials with 3D printers to manufacture one of the largest structures of its kind in Japan.
August 29, 2019
Obayashi Corporation has developed a structure that unifies special 3D printing mortar and the ultra-high-strength fiber-reinforced concrete Slim-Crete in order to use cement materials with 3D printers to manufacture one of the largest structures of its kind in Japan (shell-shaped bench: 7,000 mm wide x 5,000 mm deep x 2,500 mm tall).
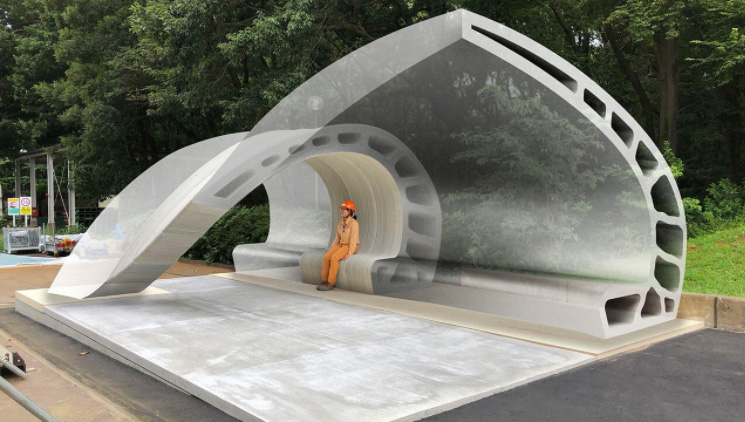
In 2017, Obayashi Corporation developed a 3D printer that discharges special 3D printing mortar from a nozzle attached to a robot arm to achieve additive manufacturing. In general, concrete and many other cement materials are mainly used to bear the compressive force of structures. Therefore, when using cement materials for structures, it is necessary to employ a composite structure that combines cement with rebar and other steel materials used to bear the tensile force, a common example of which is a reinforced concrete structure. In terms of making 3D printers that use cement materials practical as well, one key issue was to develop a method for bearing this tensile force.
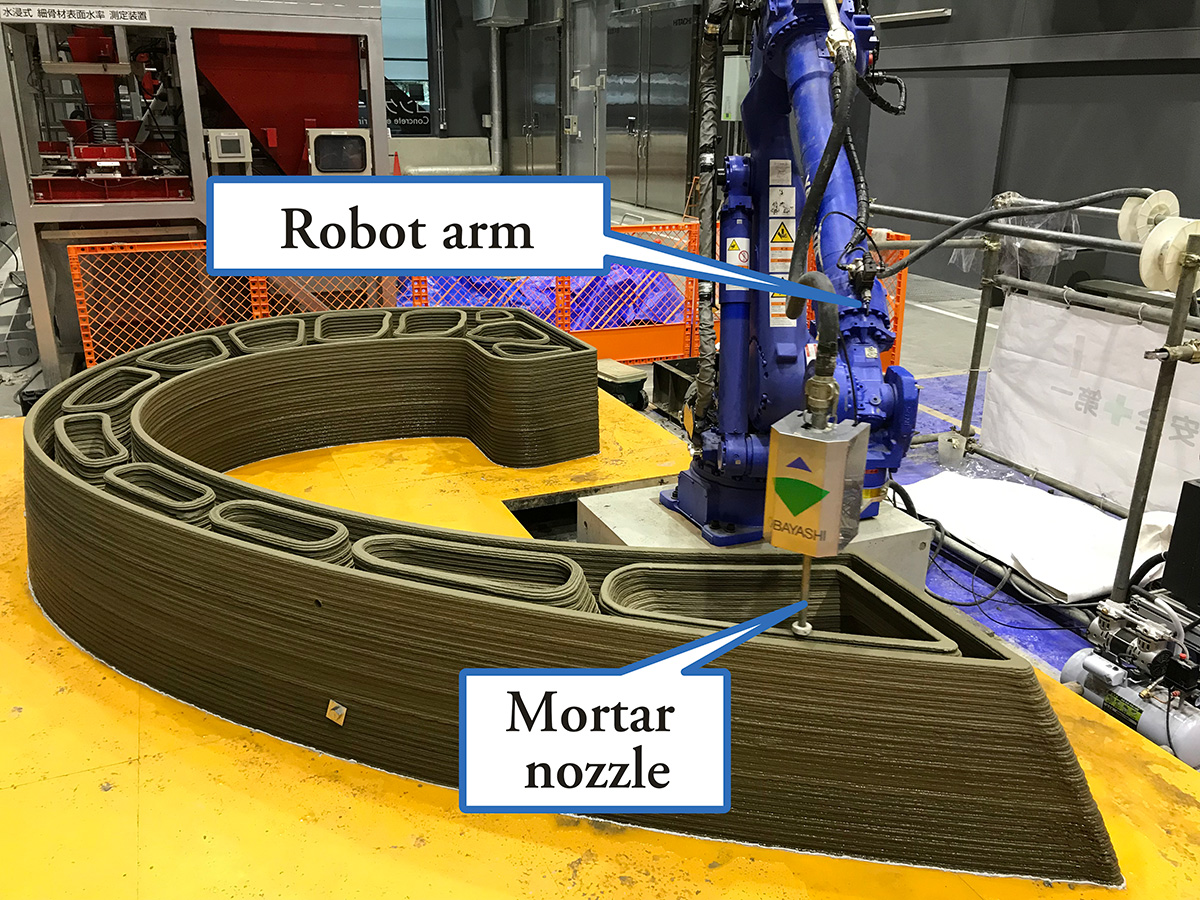
Obayashi Corporation therefore developed a composite structure that involves filling an external shape manufactured using special 3D printing mortar with Slim-Crete capable of bearing the tensile force. As proof of this concept, we also used cement materials with 3D printers to manufacture a shell-shaped bench, the largest scale structure of its kind in Japan.
The shell-shaped bench was first manufactured as 12 separate pieces, and then the completed members were set up at the installation location. We are currently conducting an outdoor exposure test to evaluate the bench's durability and other characteristics.
The features of our recently developed technology are described below.
-
Composite structure that includes the ultra-high-strength fiber-reinforced concrete Slim-Crete
Slim-Crete is a cement material that boasts high tensile strength, can be used even on its own as a structure, and hardens at room temperature. In addition, because this material is self-compacting, it can easily be used to fill external shapes manufactured using special 3D printing mortar, and—compared to manually arranging rebar inside structures—this material greatly reduces the amount of work.
-
Development of a 3D printer that uses proprietary control technology of a pump and a large robot arm
With conventional approaches, the discharge of special 3D printing mortar could not be interrupted, and there was no choice other than to handle the entire layer path in one stroke. However, by linking the robot arm to a pump and controlling the system, our 3D printer achieves additive manufacturing for which it is possible to freely start and stop discharging, thereby eliminating the need to handle the entire layer path in one stroke. The layer path is automatically generated from 3D design data. In addition, by introducing a large robot arm with a length of around 3.0 m, we have enabled the manufacturing of large structural members.
-
Achieving complex designs and pursuing structural rationality through topology optimization
For the shell-shaped bench design, we incorporated both curved surfaces and hollow parts and took advantage of the ability of our 3D printer to manufacture complexly shaped members without using forms.
In addition, for the internal structure design, we pursued structural rationality by using topology-optimization technology, which is capable of deriving a lightweight, durable form similar to a frame. As a result of using this technology to decide on the hollow parts of the internal structure, we achieved approximately 50% lighter weight (compared to a dense internal structure) without undermining the structural performance.Conceptual diagram of the composite structure Considering an internal structure using topology optimization
Before topology optimization After topology optimization
Mortar that uses special cement materials jointly developed with Denka Company Limited (https://www.denka.co.jp/eng/). Because the material possesses the strength and durability necessary for buildings and civil engineering structures, and it does not lose its shape immediately after being discharged thanks to its thixotropic properties, it can be used to manufacture structural members without using cement forms.
Obayashi Corporation's proprietary mortar material that hardens at room temperature and attains a compressive strength of 180 N/mm², a tensile strength of 8.8 N/mm², and a bending strength of 32.6 N/mm². In addition to high tensile and bending strength, Slim-Crete also offers high tensile toughness and can be used even on its own as a structure. Slim-Crete has a slump flow of around 600 mm and is self-compacting.
With topology optimization, it is possible to determine the proper distribution of materials to ensure structural integrity given certain load conditions. Such optimization is also used in the field of biomimetics—which involves imitating the forms of living things—and it is also used for structural design to derive lightweight, durable forms similar to frames.
- Management and
Organization- The Articles of Incorporation
- Basic Principles
- Transitioning of Corporate Symbol
- Corporate Officers
- Organization Chart
- Stock Information
- Financial Statements
- Technology
- BIM Timeline
- Awards
- Major Publication
- Group Companies
- Group Companies (in Japan)
- Group Companies (Overseas)