- 4 Technology
- Technology Development
“Sand-Grip Bar” High Performance Anticorrosive Rebar
Development of the Sand-Grip Bar, a high performance anticorrosive rebar, using polyvinyl butyral resin and silica-sand
Ensuring the strength of the adhesion to concrete and reducing the damage to the coating
OBAYASHI CORPORATION has developed the Sand-Grip Bar using polyvinyl butyral resin (hereinafter referred to as “PVB resin”) and silica-sand.
In recent years, for the purpose of enhancing the durability of infrastructure, etc., the use of rebars with anticorrosive properties has been required for concrete structures in coastal regions which are affected by seawater, in order to prevent chloride attack causing steel corrosion, and in cold regions and mountainous regions where anti-freezing agents are applied in winter.
Epoxy resin-coated rebars are mainly used in conventional anticorrosive rebars. However, the epoxy resin used in epoxy resin-coated rebars easily degrades when exposed to ultraviolet light; furthermore, its adhesive strength with concrete declines compared to ordinary rebars which are not coated, so it was necessary to make the lapping length of the lap joints longer than for ordinary rebars. Furthermore, there are cases in which the epoxy resin is damaged due to shocks during bending and assembly, so it was necessary to repair the damaged parts before implanting the concrete.
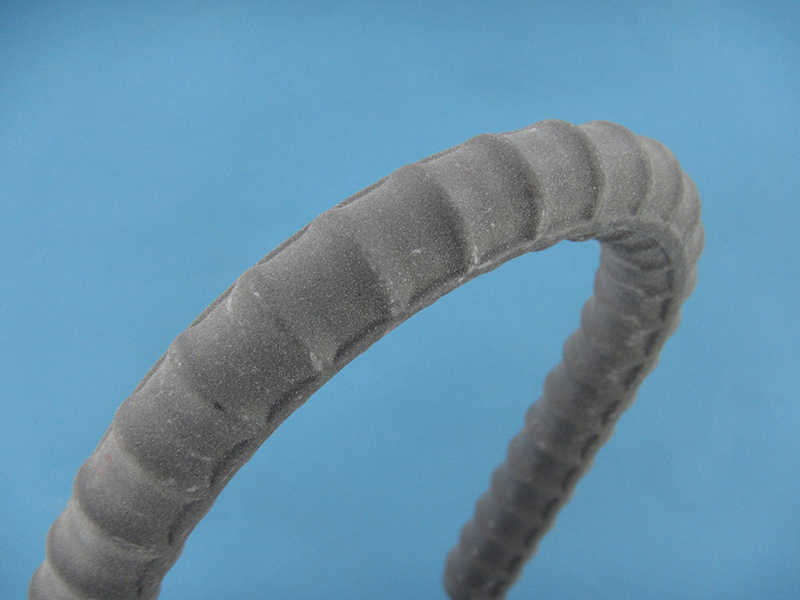
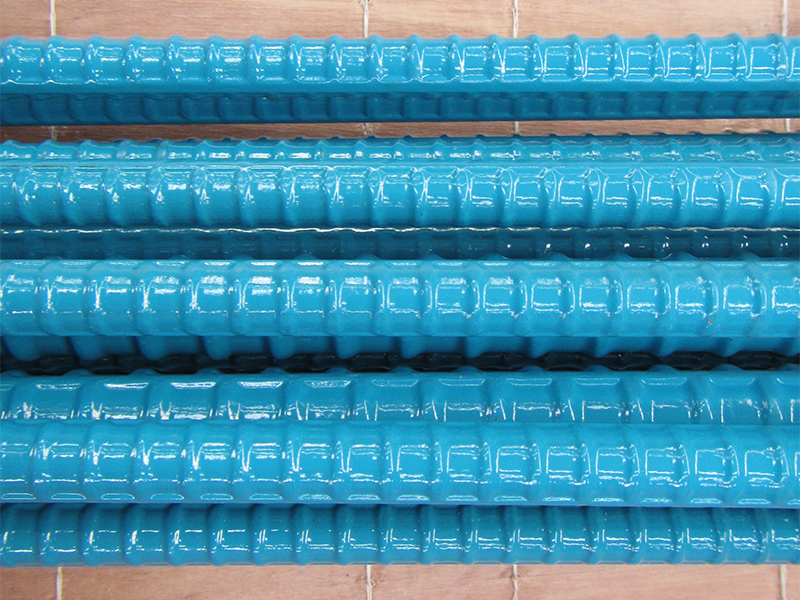
The Sand-Grip Bar is a new anticorrosive rebar which has solved the issues of the decline in adhesive strength and the repairs, etc. by cladding the rebar with PVB resin which has better weather resistance and a higher extension rate compared to epoxy resin, and attaching silica-sand around the PVB resin. We have jointly developed this product with Kawanetsu Co., Ltd. (Head Office: Ayase City, Kanagawa Prefecture), and the price is the same or lower than that of epoxy resin-coated rebars. Furthermore, in September 2016 the product acquired the evaluation of the “Examination and Certification Service of New Coastal Technologies developed by Private Companies” of the Engineering Coastal Development Institute of Technology under the name “PVB-S Cladded Rebar (Evaluation Certificate No. 16001).”
The features of the Sand-Grip Bar are as follows.
-
Ensures the same level of anticorrosive properties as the epoxy resin-coated rebar
As an anticorrosive rebar, general epoxy resin-coated rebars protect the rebar from deterioration factors such as salt content and prevent steel corrosion by cladding the rebar with epoxy resin. Their durability quality standards (chloride ion permeability, chemical resistance, etc.) are stipulated in the Recommendations for Design and Construction of Reinforced Concrete Using Epoxy Resin-Coated Rebars published by the Japan Society of Civil Engineers. The Sand-Grip Bar satisfies the quality standards in the recommendations and ensures the same level of anticorrosive properties as epoxy resin-coated rebars.
-
Extension of the lap joints is unnecessary due to the enhancement of adhesive strength with concrete
The proving tests In the case of the epoxy resin-coated rebar, the surface is smooth so the adhesive strength with concrete declines and the rebar is slippery. For that reason, when the rebars are joined, it is necessary to make the lapping length of the lap joints installed in order to ensure tensile strength at least 18% longer compared to a noncoated and ordinary rebar. On the other hand, the Sand-Grip Bar has a rough surface due to the effect of the silica-sand attached around the rebar, so its adhesive strength with concrete increases.
In the proving tests, we confirmed that the adhesion stress when the rebar begins to slip greatly increases to approximately 2.8 times that of an epoxy resin-coated rebar. For this reason, the Sand-Grip Bar can be made with the same lapping length as a noncoated ordinary rebar. -
Reduction of damage to the coating
Comparison of the extension rates of PVB resin and epoxy resin
PVB resin is a resin with a larger extension rate compared to epoxy resin, meaning that it has high followability with respect to deformations. As a result of this, damage to the coating due to shocks during bending and assembly is unlikely to occur and the time and effort required for repairs can be reduced, leading to the shortening of construction time.
It became possible to make rebar concrete structures which solve the issues of declining adhesive strength and the need for repairs, by using the Sand-Grip Bar in marine structures, etc. in regions where chloride attack countermeasures are necessary. Furthermore, the Concrete Made with Sea Water and Un-washed Sea Sand already developed by Obayashi Corporation has the advantage that its raw materials can be procured easily locally even in places where securing fresh water and good-quality inland sand is difficult, and by combining this concrete with the Sand-Grip Bar we can reduce the environmental load of materials transport and realize highly-reliable reinforced concrete structures at low cost.
Natural quartzose sand containing a lot of silicate (SiO2) which is washed with water to remove impurities. It is hard and chemically stable, so it is used in aggregates for construction materials, abrasive materials, filter materials, etc.
A degradation phenomenon in which the steel in the concrete corrodes due to the effect of chloride ions, and cracking and scaling of the concrete and cross-sectional defects in the steel, etc. occur.
This refers to steel becoming rusty. Normally, the rebars in the concrete are protected by the oxide layer called the passive layer, but the infiltration of chloride ions, etc. leads to a condition in which the passive layer is destroyed and rust can easily occur.
Agents containing chlorides that are applied to road surfaces for the purpose of preventing freezing. These agents typically contain natrium chloride, calcium chloride, or magnesium chloride.
This is one method of extending rebars, the method of joining the edges of the rebars by lapping them at a fixed length.
The general name for sand extracted from land. Generally, inland sand extracted in the neighborhood of the construction place is used as the aggregate for the concrete. For example, in the case that extraction of good-quality inland sand is difficult because the land area is small so there is not much inland sand, as in the case of remote islands, etc., transportation of the sand from the mainland is necessary.
- Management and
Organization- The Articles of Incorporation
- Basic Principles
- Transitioning of Corporate Symbol
- Corporate Officers
- Organization Chart
- Stock Information
- Financial Statements
- Technology
- BIM Timeline
- Awards
- Major Publication
- Group Companies
- Group Companies (in Japan)
- Group Companies (Overseas)