Project Frontline
Building "ES CON FIELD HOKKAIDO,"
a Baseball Park with a Giant Openable Roof

Kitahiroshima City, located in the center of the Ishikari Plain between the Sapporo Station and the New Chitose Airport Station on Japan Railway Hokkaido Chitose Line, is a town among gently sloping hills with a harmonious blend of abundant nature and urban functions. It is an area where temperatures drop to -20℃ in winter, and construction is underway to build the new baseball park for the Nippon Professional Baseball Team, HOKKAIDO NIPPONHAM FIGHTERS.
Constructing a new baseball parkthat will serve as the center of the city
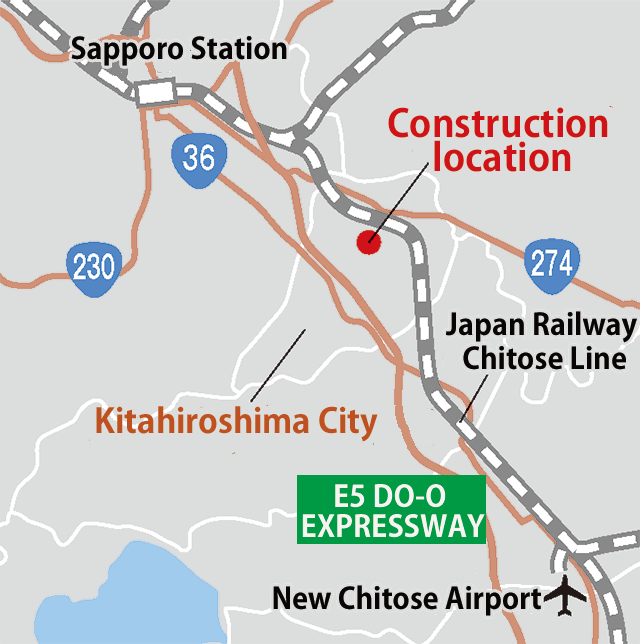
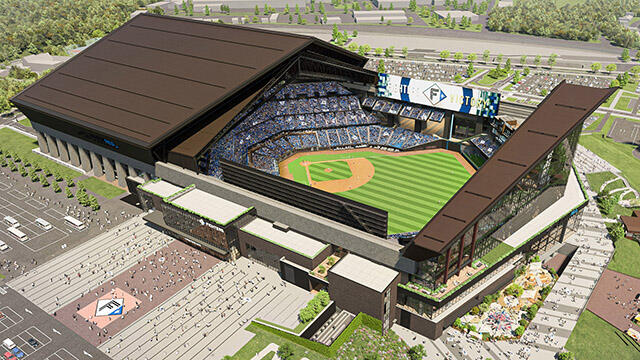
SAPPORO DOME, serving as the current base for the HOKKAIDO NIPPONHAM FIGHTERS, is a facility owned by City of Sapporo and thus cannot be directly managed and operated by the baseball team. The baseball team therefore set out to build their own new baseball park through a public and private sector collaboration with Kitahiroshima City, by promoting urban development with the new park at its core.
The construction site for the new baseball park, ES CON FIELD HOKKAIDO, is a sloped area with a 30 m elevation covering approximately 320,000 m², and was formerly planned as the site of Kitahiroshima Sports Park. It will be a park with capacity of 35,000 people when it opens for the 2023 season. The baseball park is designed with various features, including seats close to the field offering a great sense of presence, an openable roof, natural turf field and glass walls as high as 70 m providing natural lighting, and a 360-degree circuit-style concourse.
"Hokkaido Ballpark F Village," which will hold the new baseball park, is scheduled to house a hotel and commercial facilities in the future, becoming a town appealing in areas other than spectator sports. Construction on-site has passed the midway mark for full delivery, with the fixed roof almost completed, and assembly of the retractable roof having been started.
Supporting a giant roof weighing 10,000 tons
Construction planning was established one year before start of construction
While this construction project had fixed start and end dates and full delivery of 32 months, detailed design drawings were not fixed when the construction order was placed. Therefore, progress of the roof construction was the greatest point of concern in meeting the established delivery date.
Taking the positioning of four individuals including Project Director Takenaka as the starting members one year before start of construction as an opportunity, frontloading that would allow opinions held by the construction side to be reflected from the outset with regard to structure and architectural design work was implemented. Both the design and construction sides exchanged their opinions and ideas with regard to construction planning to meet the tight construction delivery. As a result, a plan was formulated that would divide the baseball park into the North Zone for the home base side and the South Zone for the center field side, and move ahead with construction for the general area where the fixed roof would be built, from the North Zone toward the South Zone.
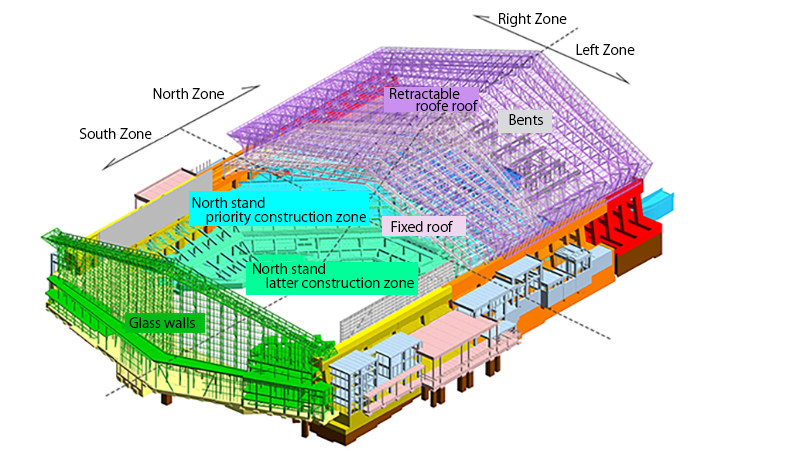
Girder frame structure to support and slide the roof
The large roof is sloped and gable-shaped, with strong force spreading the roof outward to support heavy snowfall during the winter. It is the girder frames made of rebar concrete that withstand this force. A giant framework structure with an unprecedented 2.5m x 4m column cross section and 4 m x 3 m beam cross section, equivalent to civil engineering structures such as roads and bridge piers, became necessary for the architecture.
Ideas were also sought from sources such highway construction methods. However, this construction would not be completed in time if such methods were to be implemented. Thus it was decided that the framework of the girder structures would be made in a factory in advance by precasting (PCa). Since the framework had a large cross section, however, creating it with PCa as one structure would result in several hundred tons in weight, and heavy lifting equipment used at construction sites would not be able to lift it. It was also necessary to keep the structure at a weight that could be transported, putting into consideration weight limits placed upon public roads that would be used to transport the manufactured structures from the factory to the site.
Therefore, a method where only the columns and beams would be manufactured with PCa, and the parts joined on-site was considered. The "outer shell PC", which takes columns made with PCa for the outer part only, and "knuckle PCa" beams, in which several parts made with PCa for the bottom layer only are layered together, with the upper portion being joined at the construction site, were developed for this construction.
The issue regarding weight was resolved by layering factory-manufactured outer shell PCa on-site, and filling them with concrete. Inner and upper portions of the girder structure framework were filled with Clean-Crete, a low-carbon concrete developed by Obayashi Corporation.
Further, high-precision construction was realized utilizing a sliding system frame for the complex-shaped structure of the framework for the retractable roof, and enhanced safety and productivity were successfully achieved.
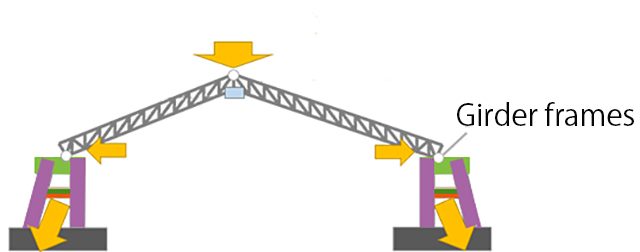
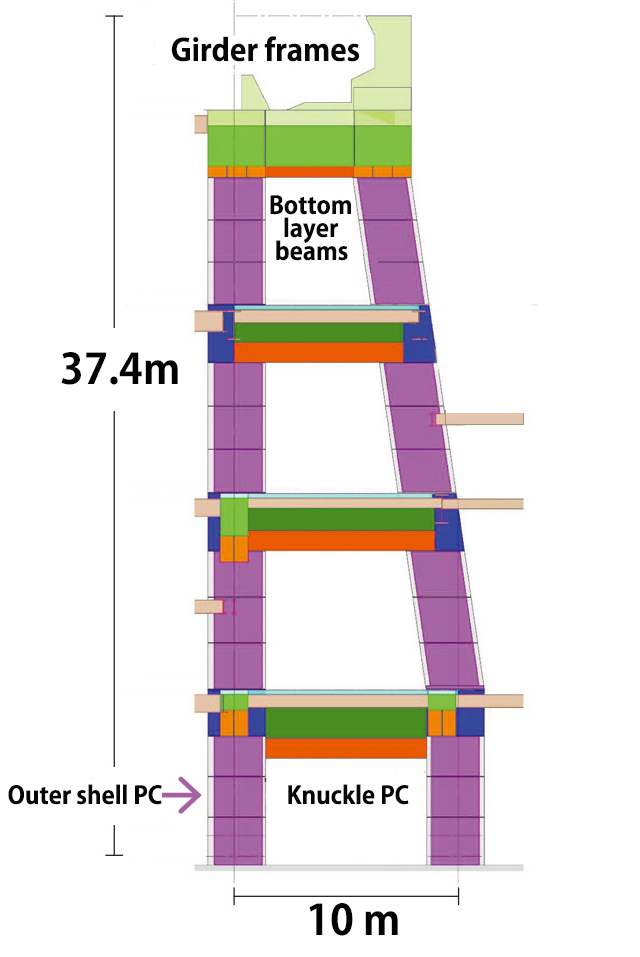
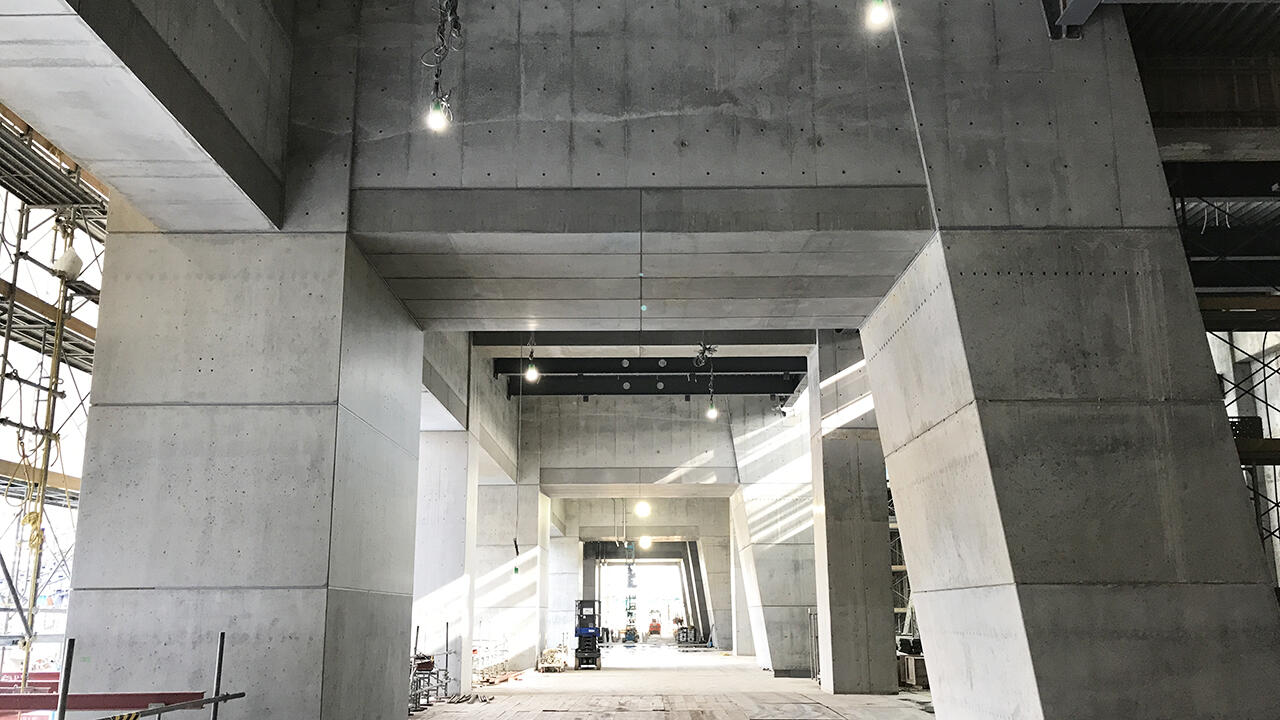
Enhancement of safety and productivity for the roof construction
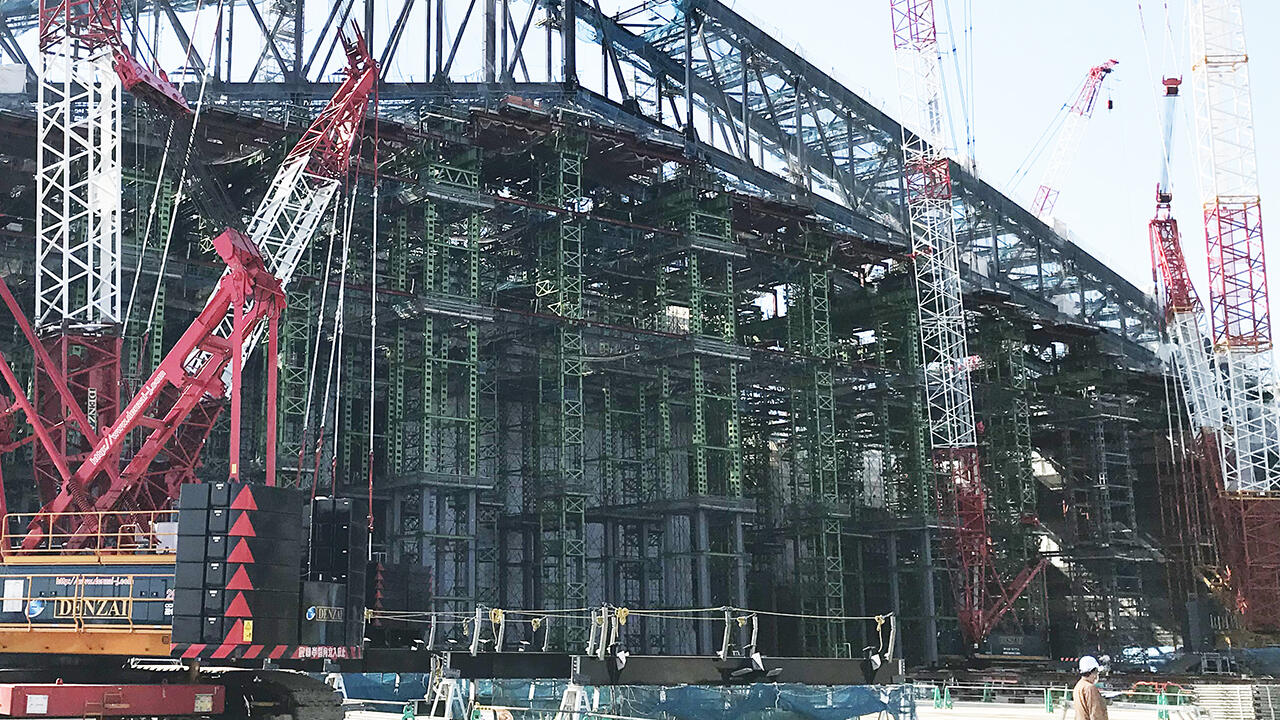
The new baseball park's giant roof consisting of the gable-shaped fixed roof and retractable roof has two major features. One is that since there are a large number of seats on the right side, the slope is 20 degrees on the left side and 17 degrees on the right side, making the roof asymmetrical. The other is that the roof is designed to be waterproof to keep the snow piled up on the roof in the winter from falling off.
Various ideas were put into place, especially with the temporary design plans, to realize these features. If the fixed roof were to be constructed with a standard bent method overall, temporary support columns (hereafter, "bents") would be positioned on the field and necessary steel beams for building the roof would be assembled on top.
However, building the stand will not be possible directly underneath construction of the fixed roof, and as the space for moving the boom of heavy lifting equipment required for construction underneath will become limited after the roof is completed, work efficiency will decrease.
Therefore, a plan was proposed for the construction of the fixed roof to be the same sliding type as the retractable roof, and for bents to be placed on the outer framework of the stand that can be shared with construction of the retractable roof. Construction of the fixed roof steel beams and framework for the stand directly underneath took place at the same time.
The roof is assembled on the ground into units made with waterproof materials and ceiling sound-absorbing panels, and only waterproofing between the units is handled at roof height. This has led to successfully enhancing safety and work efficiency as well as cost reductions.
Deputy Project Director Kuroda said, "Proposal of the construction method was proactively made by the construction side. Cooperating with relevant divisions, various methods were taken so that delivery was not delayed, and construction is currently also progressing smoothly."
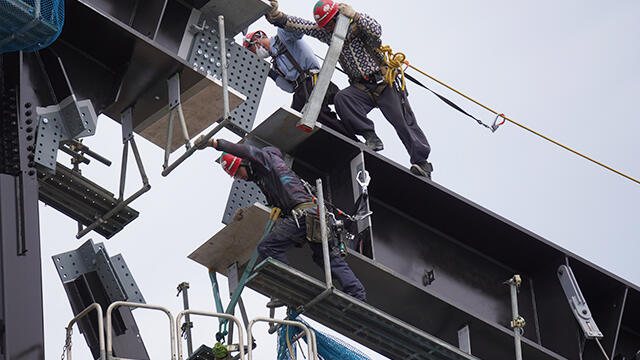
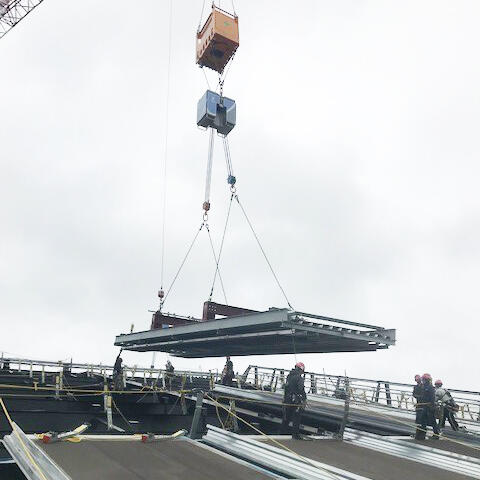
Site Scan, effective in construction management
Using images captured by drone, the Site Scan for ArcGIS service automatically creates point cloud data in a cloud allowing the data to be shared. As the construction site area is large, the system can be used to monitor conditions on-site that change daily. It is able to confirm the site three dimensionally, and data is shared among employees to confirm on-site conditions, undergo simple measuring, and calculate cut and fill soil volumes. It is effective in construction management. And this has been utilized for work plan briefings of stock yards and cranes as well as during construction site tours.
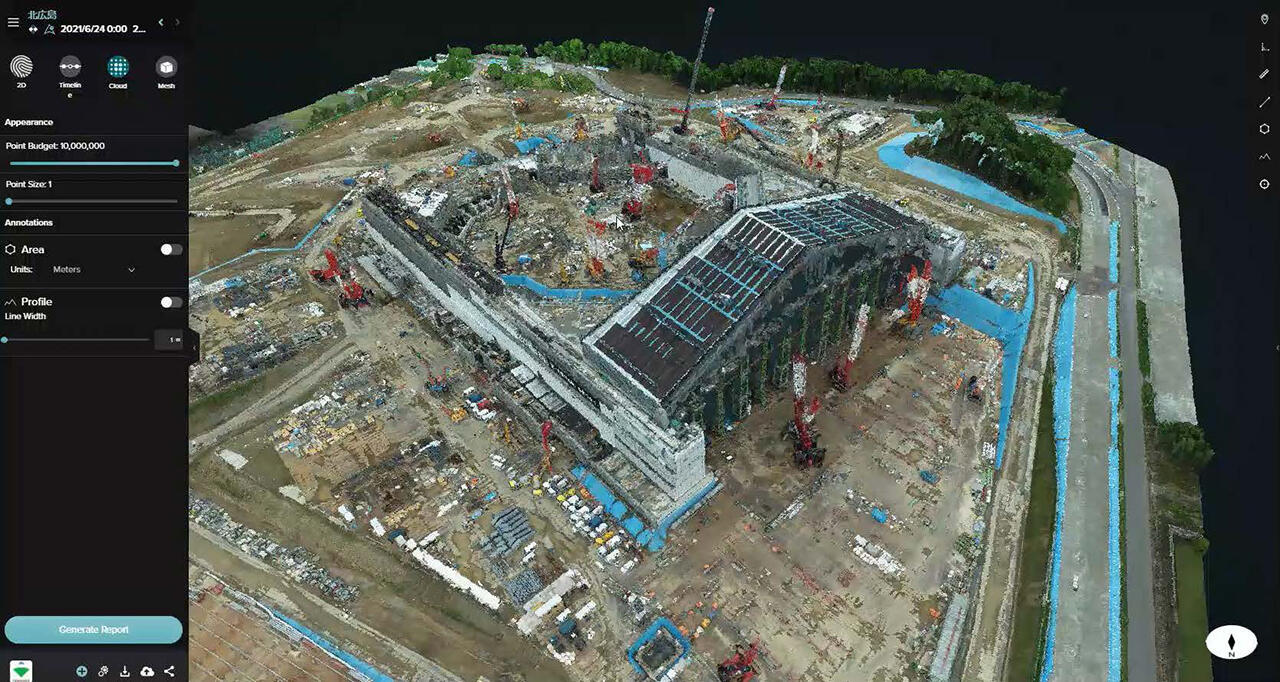
Taking on construction during severe winter season
Handling accumulated snow
Construction is sometimes halted in Hokkaido during the severe winter season; however, this construction is on a tight delivery schedule and the work cannot be halted twice during construction of the park due to harsh winters. Therefore, measures must be put in place that can meet the unique needs of vast construction sites in Hokkaido.
With the site area so extensive, most workers commute by car. Removal of massive snow in the winter and heating on-site are important for the construction location, including parking areas. Two large-scale wheeled excavators and five small excavators are positioned on-site to work on snow removal.
If the weather forecast is for snow, a dedicated snow plow team is deployed overnight to work on snow plowing from midnight to 6:00 a.m., to prepare the site for construction to smoothly begin in the morning. Even after that, snow must be plowed around one's area for roughly 30 minutes after the morning staff meeting, and snow must constantly be handled.
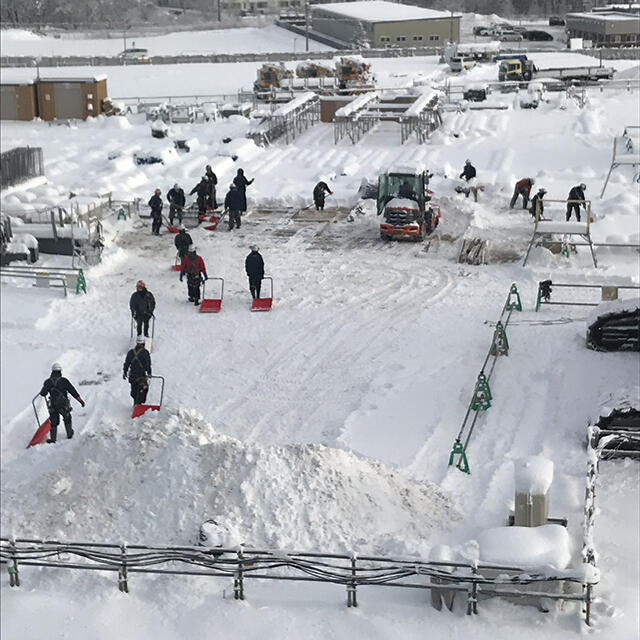
Ensuring safety and quality
Temperatures can drop to -20℃ during winters in Kitahiroshima City. Under such circumstances, sufficient consideration must be put into ensuring quality of buildings not to mention the safety and wellness management of employees and workers.
In concrete pouring during the severe winter season, concrete freezes during curing if left in the cold, which affects the quality. Temporary walls and roofs are therefore set up to cover the working area before pouring begins, and stoves are lit each time work begins so as to ensure quality. Snowfall that has accumulated melts into water as the temperature rises during the day, but then turns to ice. As this process gets repeated, ice blocks become as thick as roughly 20 cm, and they cannot be easily removed, causing disruptions in work. As it gets slippery and dangerous and issues arise surrounding the safety of employees and workers, workers use electric pick hammers to break up the ice one by one.
Deputy Project Director Shimada said, "Continuing construction work in the winter is harder both physically and mentally than one might imagine, but we still have to look ahead and keep working in those conditions." Taking effort to handle the snow and ice before starting work, workers assemble the rebar and pour concrete. Project Director Takenaka said, "The work during winter in Hokkaido is done with the help of know-how from the local community, striving to maintain the same level of quality in construction as in areas without a severe winter season."
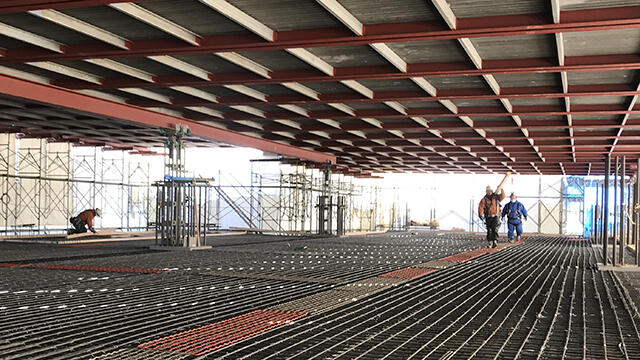
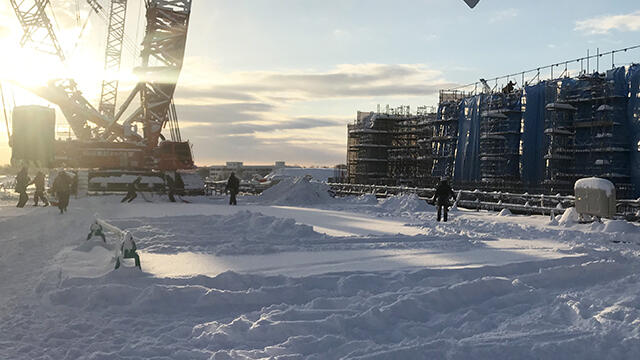
The site is scheduled for construction going forward of the retractable roof together with the glass walls on the south side, and the exterior and field as well. Construction work is moving along in preparation for the 2023 season opening in spring.
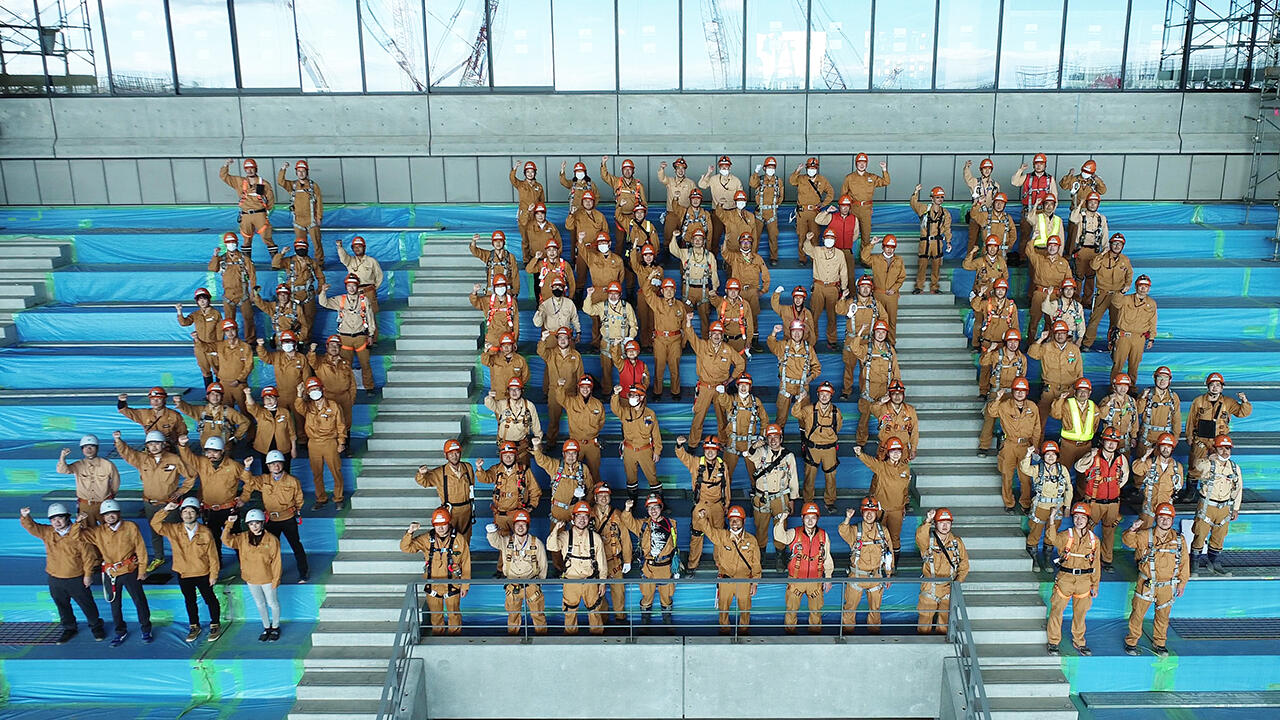
(Reporting in September 2021)
Construction Overview
Project Name | Construction plan for Hokkaido Ballpark (provisional name) |
---|---|
Location | Kitahiroshima City, Hokkaido |
Client | Fighters Sports & Entertainment Co., Ltd. |
CMr | Yamashita PMC |
Design | Obayashi Corporation and HKS |
Overview | RC construction, steel construction, steel RC construction, B2, 6F, total 120,500 m² |
Delivery | May 2020 - December 2022 |
Construction | Obayashi Corporation and IWATA CHIZAKI INC. |