Project Frontline
Creating a New Landmark in Yokohama Minato Mirai
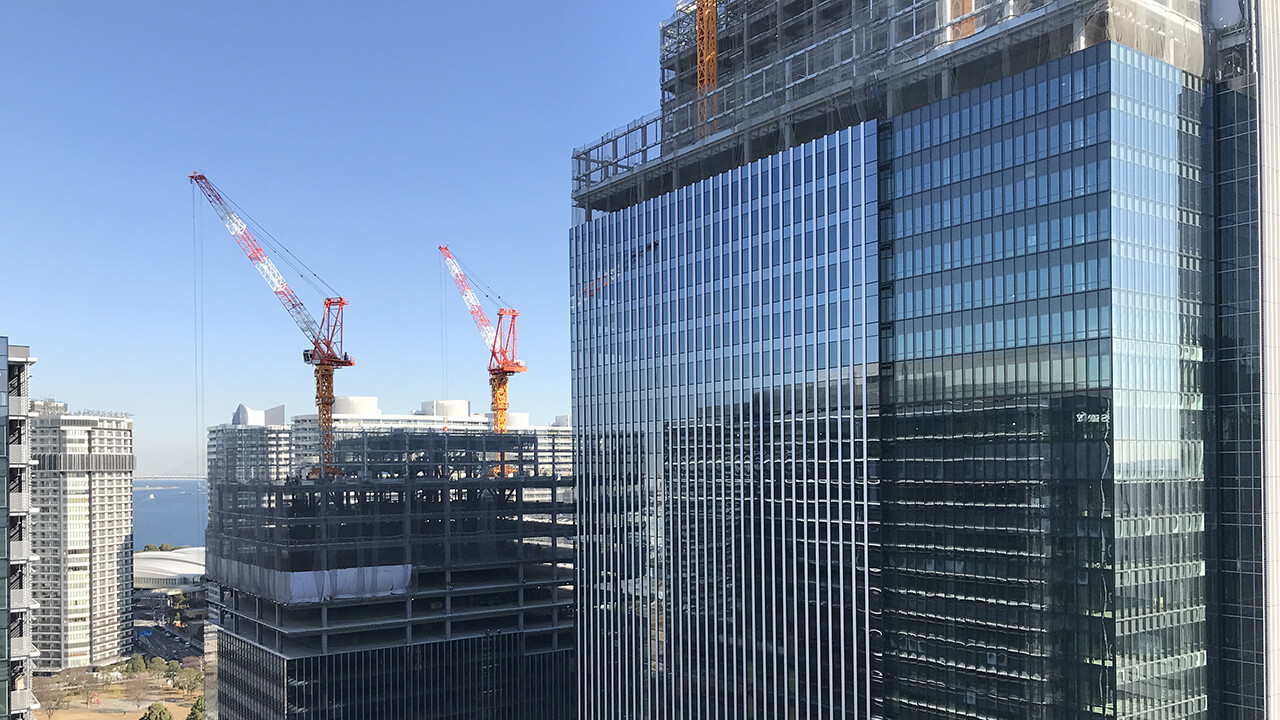
Planned urban development has been underway in the Minato Mirai 21 District in the waterfront area of Yokohama City, Kanagawa Prefecture since the 1980s. In conjunction with other companies, Obayashi Corporation is currently developing a large-scale complex called the Yokohama Symphostage that will house offices, a hotel, retail outlets, such as shops and restaurants and other tenants. Obayashi is in charge not only of the development, but also the design and construction of the complex, trying to create an attractive city where people will come and meet.
An urban development project by four companies from different industries
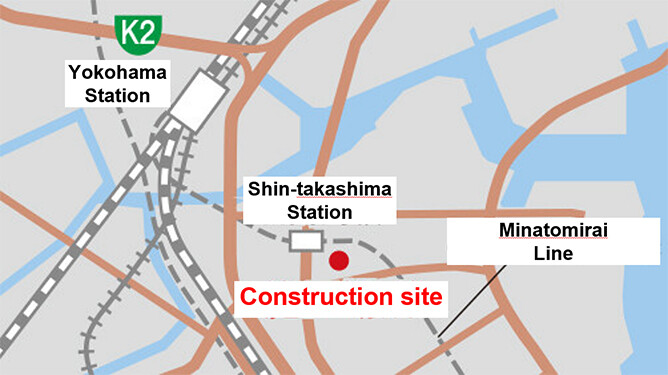
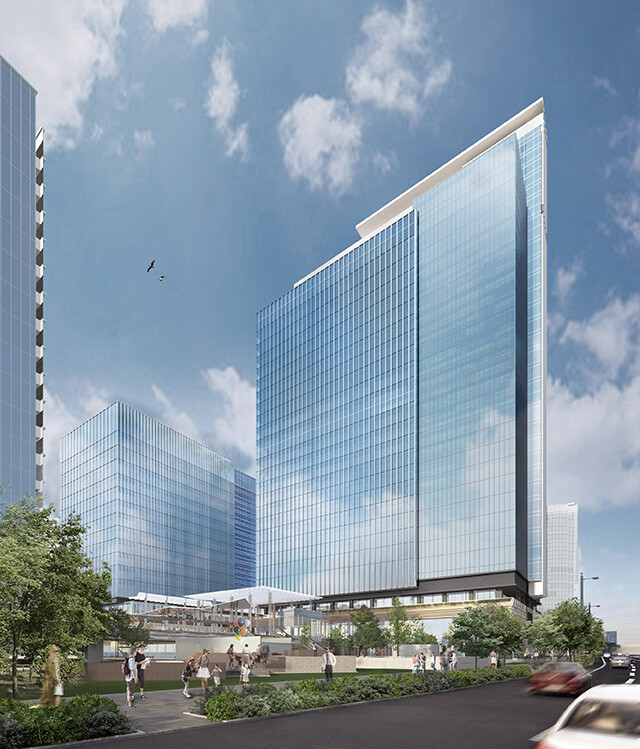
In March 2019, a consortium that included Obayashi was selected as a prospective project developer in a proposal-based competition sponsored by Yokohama City, and land owned by the city near Shin-Takashima Station on the Minato Mirai Line and roughly eight minutes on foot from Yokohama Station was transferred for the purpose. A construction of a large-scale multipurpose complex with a total area of over 180,000 square meters and boasting a 30-story West Tower and a 16-story East Tower will be developed on this land.
The consortium consists of four companies with different core businesses: Obayashi, Keikyu Corporation, Nippon Steel Kowa Real Estate Co., Ltd., and Yamaha Corporation. Our strength is its abilities to create new synergies by bringing together each company's expertise and know-how.
This is the first time that Obayashi will serve as the managing company in a large-scale joint development project with other companies. Obayashi is determined to capitalize on its position as developer, designer, and as a construction company to reduce costs and create environmentally friendly, attractive facilities through the introduction of the latest technologies and other means. To those ends, we are cooperating with the consortium members on a daily basis.
The pursuit of ultimate efficiency
Large-scale construction site with 1,500 workers
We are using standard technologies and construction methods to keep the cost of construction as low as possible. However, given the huge construction volume, around 1,500 workers are expected to be on site during peak periods. So as not to compete with large construction sites in Tokyo over worker allocation, we carefully reviewed processes to ensure that work would be spread out as evenly as possible over the construction period.
We started work first on the underground section of the West Tower, a tower taller than the East Tower, involving more construction. After that, we will move onto the underground section of the East Tower, while also assembling the aboveground steel frame for the West Tower.
We concluded contracts with suppliers and subcontractors early on. As Project Director Yuji Sato says, "It is not easy to minimize peak of the number of workers when constructing two high-rise buildings on the same site. That's why we carefully examined the work procedures and created firm construction scenarios before starting the work."
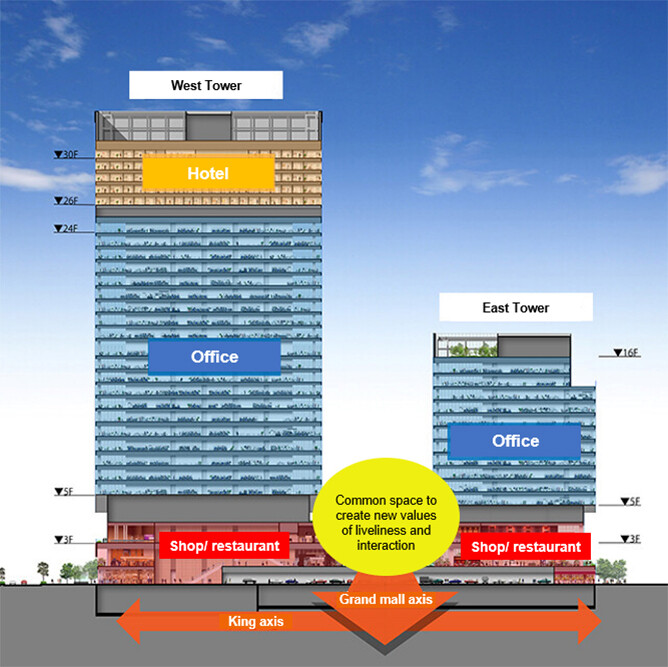
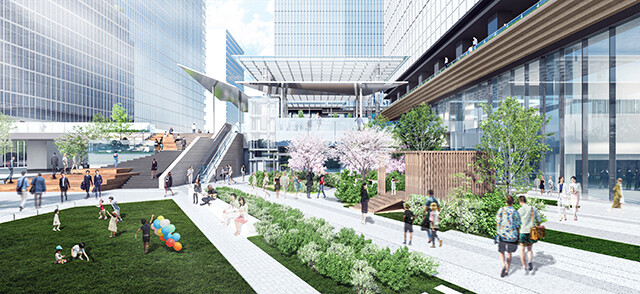
Taking full advantage of the design-build contract in underground construction
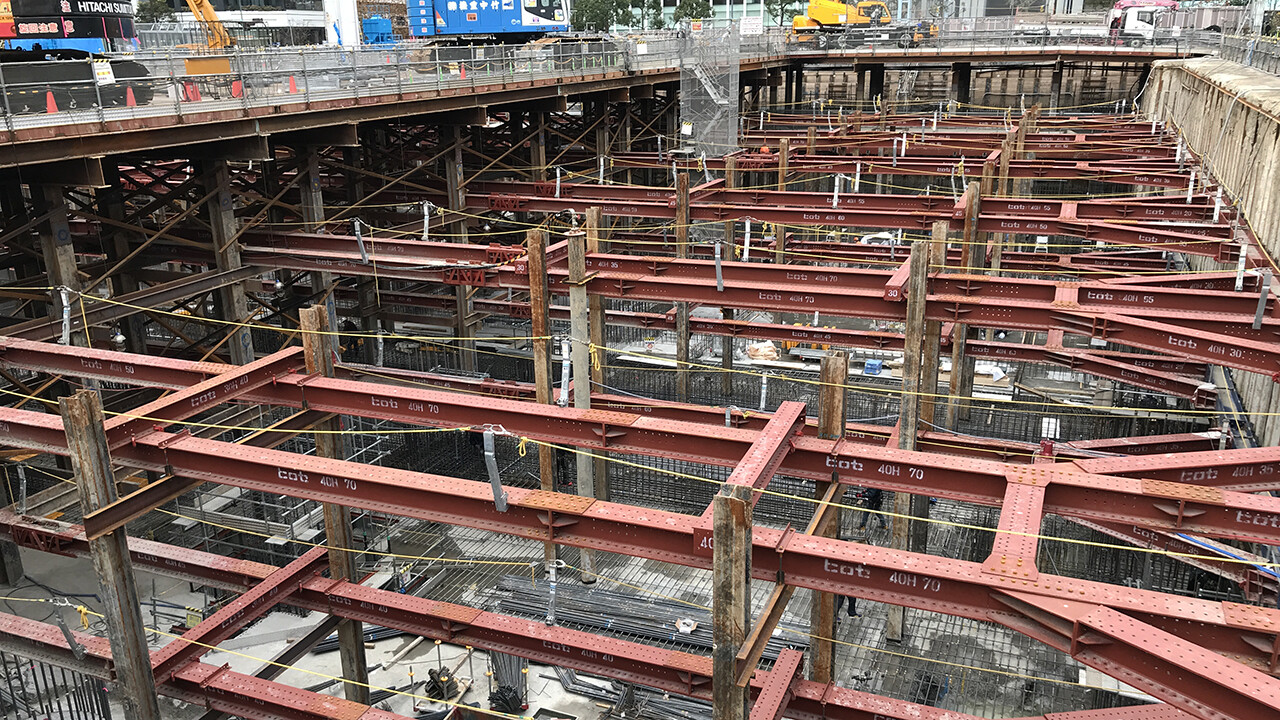
To minimize the volume of excavation required, the basement floor was only one floor, and the underground space was kept to an absolute minimum to reduce the volume of construction work.
Girder shoring was used to support the earth-retaining walls during excavation, and a bottom-up construction method was adopted to build the underground frame upwards from the foundation's footing beams. Unlike with the top-down construction method, in which underground and aboveground construction can be carried out at the same time, it was therefore essential to shorten the underground construction period. However, because the land was soft, it was also necessary to install girders at a fine pitch in order to control any displacement of retaining walls.
To increase construction efficiency, girders were arranged in one direction in a concentrated layout to secure large workspaces, while corner angle braces and ground anchors were used at the ends of the excavation area.
Given the proximity of the West Tower to the public road, it was not possible to secure the space required to install the ground anchors needed for cantilever retaining. So the design of the underground frame was also changed to facilitate its installation. The advantage of design-build contract is that you can incorporate builder side's opinions into the design to reduce construction time and costs.
- *1 Clean-Crete
A type of concrete which can reduce CO2 emissions by a maximum 80% by replacing cement with industrial by-products such as fine powdered slag from blast furnaces, which do not generate much CO2.
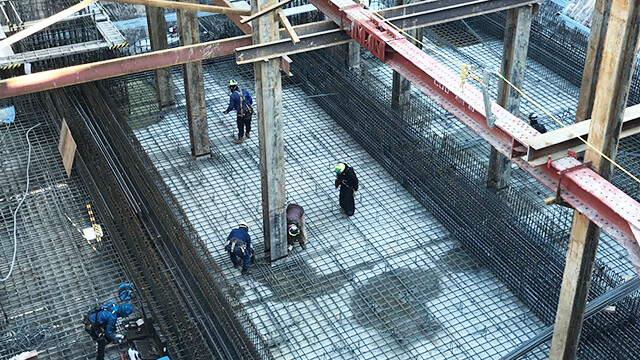
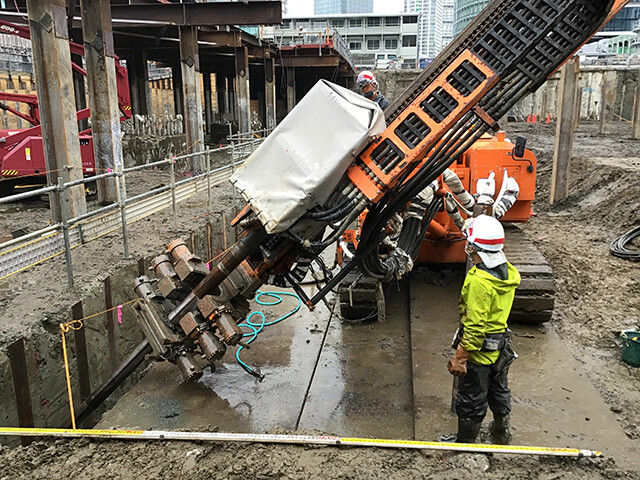
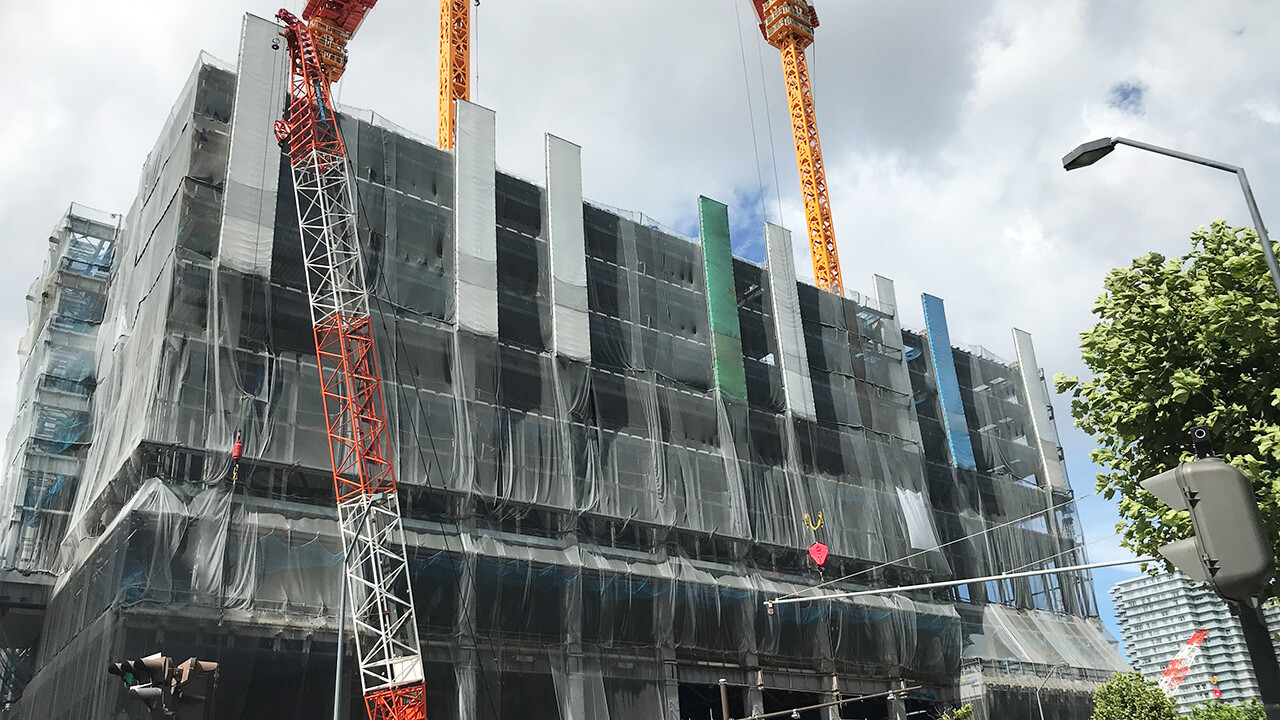
Long-term use of temporary platform
Controlling the timing for starting the construction on the Grand Mall area connecting the West Tower and East Tower was key to the smooth construction process. This area is to be used as an event space, which involves installing a large roof. The site plan makes the most of every inch of land, so there wasn't enough space for the necessary construction yards. To overcome this problem, a temporary platform was installed in the Grand Mall space to serve as a route for construction vehicles to access the two buildings. "To avoid delaying construction processes for the two buildings, we decided to leave the temporary structure in place for as long as possible and remove it when the steel frame assembly and framing work had progressed," explains Mr. Sato.
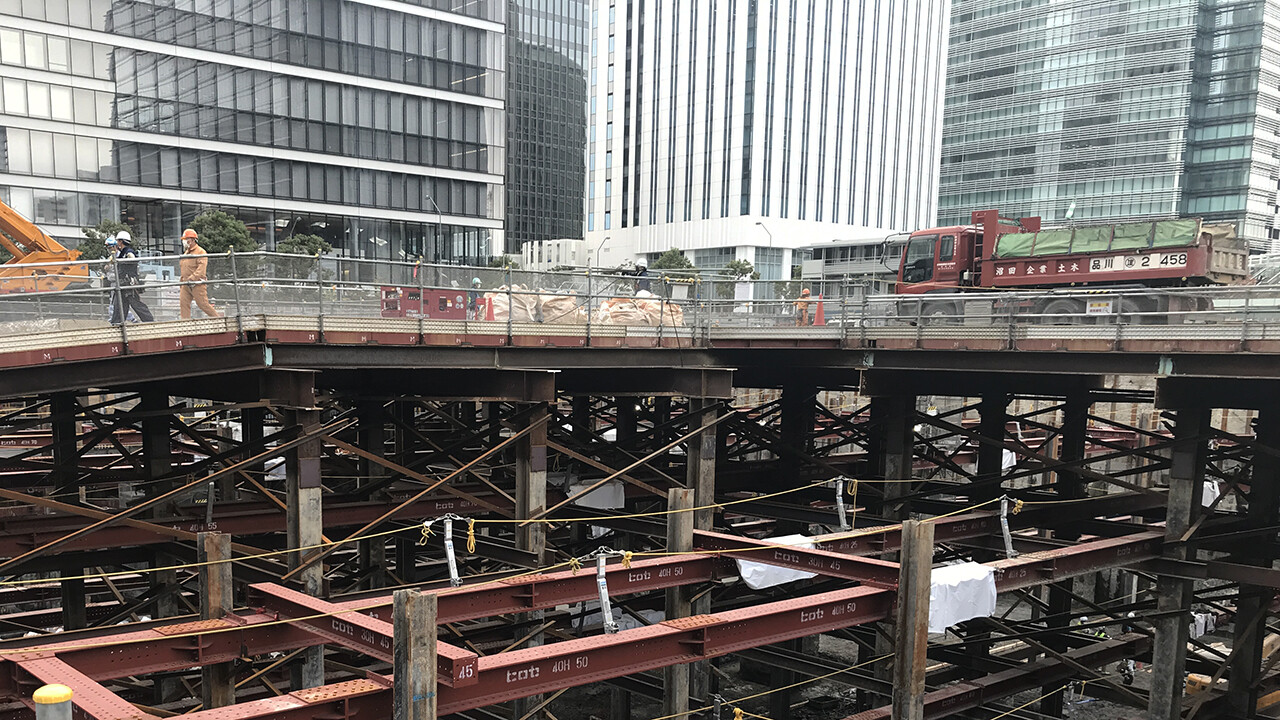
The two buildings topped up as planned, and the time for removing the temporary platform drew near. Fortunately, as construction progressed, we were able to rent space on the adjacent site to secure a route for construction vehicles and solve the shortage of storage options for materials and equipment. In the end, we were able to arrange things so construction was not overly impacted by the removal of the temporary platform.
Mr. Sato proudly states, "We had a firm grasp of the volume of each construction project before construction started and we were able to determine how long we could wait before starting construction of the Grand Mall area. As a result, we were able to proceed with the construction several months earlier than initial schedule. All thanks to our determined pursuit of the most efficient construction methods."
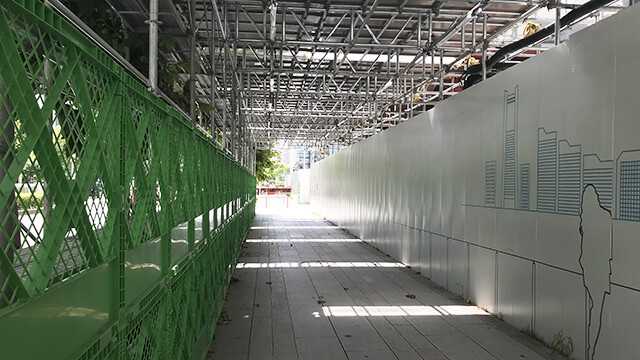
Acquiring ZEB Ready certification: creating environmentally friendly buildings
Increasing the value of the building can prove a strong appealing point when looking to attract office tenants. Under the Building-Housing Energy-efficiency Labeling System (BELS) evaluation, the entire building received the highest rating of 5 stars, and the office section received ZEB Ready(*2) certification.
This achievement was due in large part to Obayashi's determined stance as an eco-conscious(*3) business operator, as well as the design change proposals made to improve the building's added value. The building boasts the first ZEB Ready certification acquired in the Minato Mirai 21 Central Zone.
One distinctive feature of the building's outer skin is its ability to reduce heat load. Three types of glass curtain walls: vertical louvers, compact double skin, and horizontal louvers are strategically placed where they can have the maximum effect on reducing heat load. We took great care with the installation spacing and angle of the louvers and verified the heat load reduction. The exterior was designed to suit each orientation and air conditioner capacity optimized to reduce energy consumption.
- *2 ZEB Ready
An energy-saving building that consumes 50% or less energy compared with a standard building. ZEB stands for net zero energy building. - *3 eco-conscious
Short for ecology conscious. Demonstrates a strong interest in protecting the natural environment.
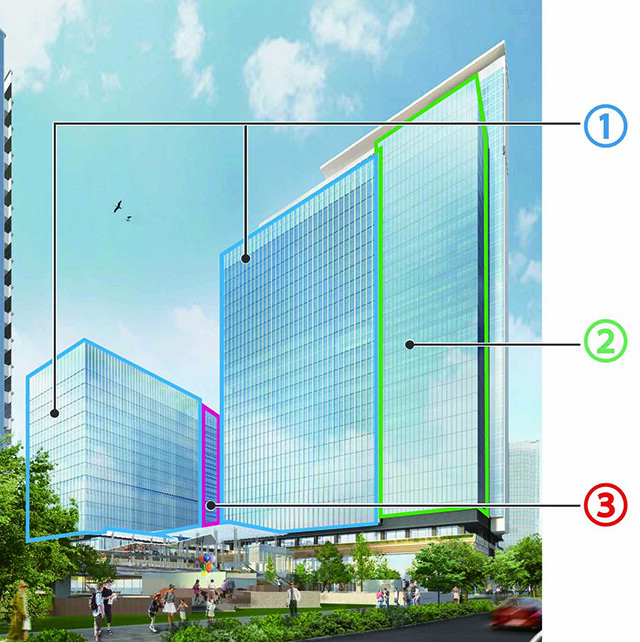
(1) The vertical louvers with their solid, chiseled vertical fins provide effective shielding from solar radiation.
(2) Compact double-skin high-performance curtain walls are used on the west, east, and south sides that experience the highest heat load.
(3) The horizontal louvers with horizonal fins create an extended line of sight.
Real work style reforms and job satisfaction
Work style reforms are often judged on working hours, but Project Director Sato feels that "it is important to ensure that employees experience great job satisfaction and feel comfortable in the work. That's why we first created a positive office environment."
The construction site office was equipped with all the latest fixtures and fittings to improve the work environment. We also came up with various ways of creating an office environment in which people could relax, communicate easily, and concentrate on their work. One example of this was our decision to create zones in the construction site office. The office space is divided into an active zone, a solo work zone, and other specific spaces.
Keeping the office exclusive to authorized personnel helps enhance concentration and inspire vigorous horizontal communication in each of the specific zones. This reduces the emergence of gaps between each work and makes for smoother coordination across the site.
In addition to improving the office environment, we are also actively utilizing ICT tools. As a rule, we circulate information electronically on eYACHO, a construction management app for construction sites, and share information with relevant parties using Microsoft Teams to facilitate a paperless operation.
All of these measures help create an environment in which employees can concentrate on their work and enjoy a greater sense of fulfillment. Ultimately, these innovative measures have boosted productivity considerably further than was initially expected. "The dynamic excitement of building something on a site is unique to the construction industry. I believe that we have to adjust our workplaces flexibly in order to create environments in which employees get to truly enjoy that sense of fulfillment," says Mr. Sato.
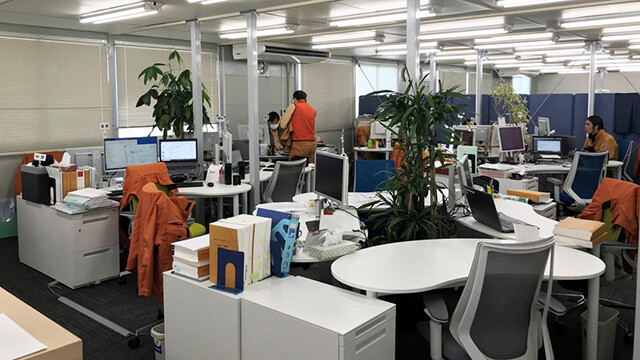
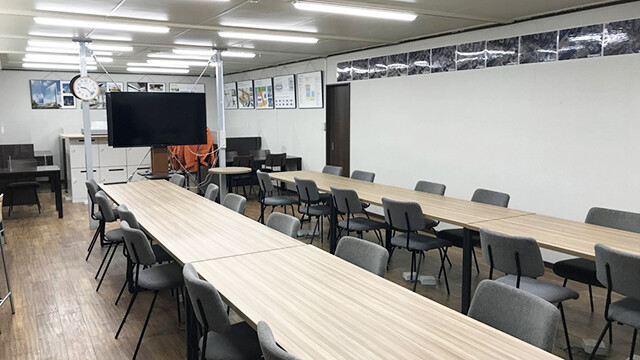
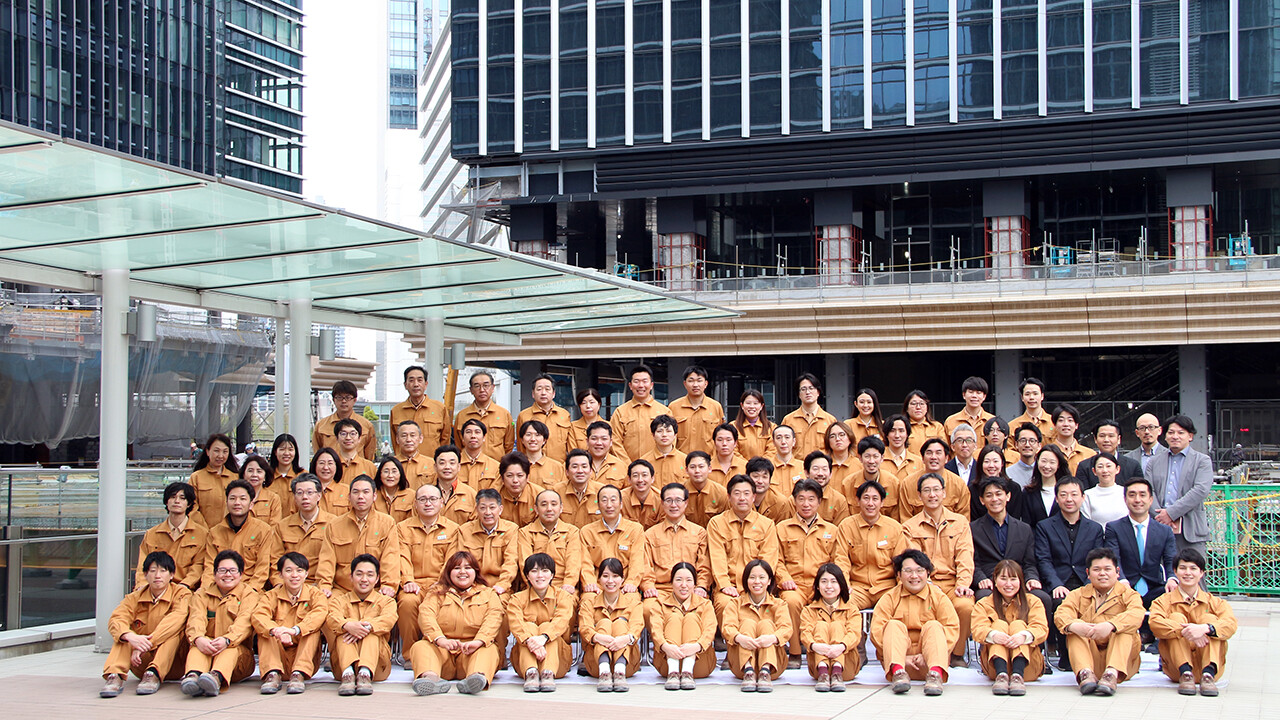
(Interview in March 2023)
Project outline
Project name | (Tentative name) Minato Mirai 21 Central District 53 Block Development Project |
---|---|
Location | Yokohama City, Kanagawa Prefecture |
Client | Obayashi Corporation, Keikyu Corporation, NIPPON STEEL KOWA REAL ESTATE CO.,LTD., Yamaha Corporation and Minato Mirai 21 Central District 53 Block Development Joint Company(Special Purpose Company invested by Obayashi) |
Designers | Obayashi Corporation |
Outline | S, SRC, CFT construction, B1F, 30F, PH2F, 2 buildings, total floor area 183,132m², number of hotel rooms: 150 |
Construction period | From April 2021 to March 2024 |
Contractor | Obayashi Corporation |