Development of an autonomous logistics system for construction site with multi AGV(Automatic Guided Vehicle) collaboration
Improvement of on-site logistics with boarding automation into construction elevator
-
Building Construction
Obayashi Corporation (Head Office: Minato-ku, Tokyo, President: Kenji Hasuwa) has developed an autonomous logistics system to deliver various sizes and types of materials within construction sites using multi-AGV collaboration to work in a variety of construction projects.
(Video playback time: 2minutes 28seconds)
The low-floor AGV, which Obayashi developed in 2015, is small and light weight. Since it can enter a construction elevator while holding material, operators do not need to load/unload material to change the material direction in order to carry material in narrow area. Only one operator is required to carry one pile of material whereas this would require three or four workers to carry using traditional methods.
To improve productivity, Obayashi Corporation collaborated with SRI International in the USA to make the low-floor AGV autonomous. The AGV runs autonomously, avoiding obstacles in its route by using start and delivery target coordination. Additionally, by collaborating with multiple AGVs and a construction elevator, the system can reduce wasteful waiting time and the number of AGV boarding into construction elevator.
- ※1 SRI International
One of the most innovative nonprofit independent research institutes in the world SRI was established by Stanford University to support local economy development in 1946. It became independent from Stanford University in 1970 and is based in Menlo Park, California. SRI International and Obayashi Corporation currently are engaged in a strategic partnership for the co-development of construction related technology.
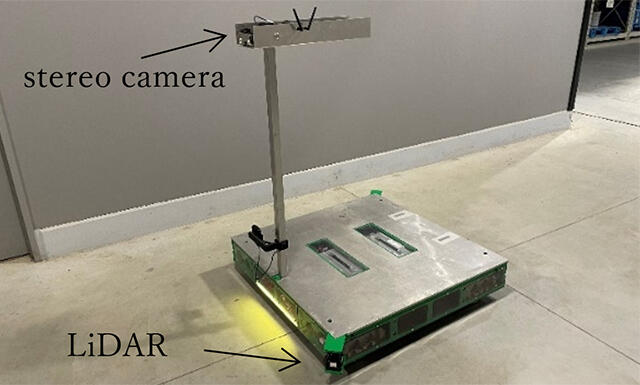
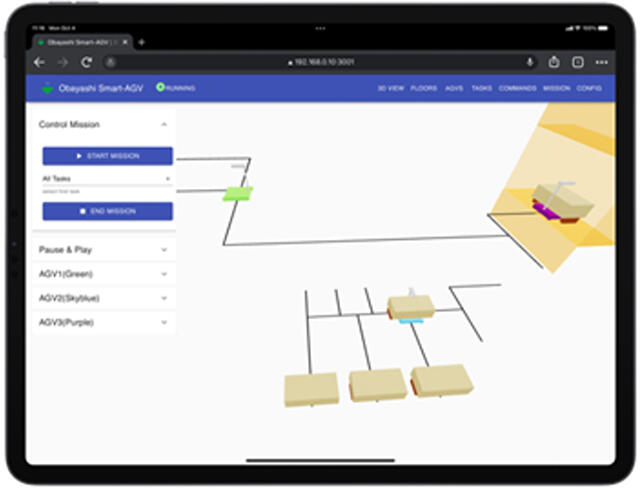
The system features include the following.
Autonomous operation with two dimensional markers
The system runs automatically, estimating self-location by reading two dimensional markers with a stereo camera on the top of sensor head. An operator needs to provide a target point and rough recommended route. Because the system can detect obstacles on the route with LiDAR, the system works safely within the construction site, despite the environment changing dynamically.
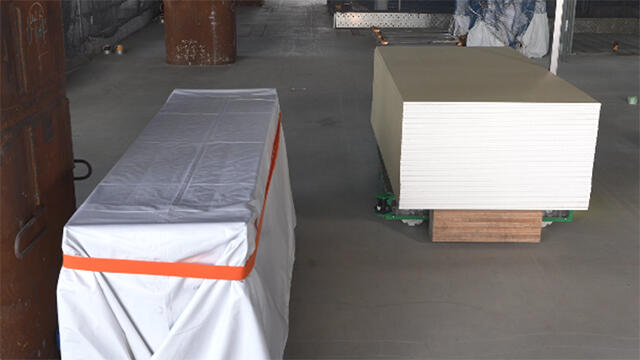
Instant adjustment allows route change
Many autonomous systems require generating an environment map(pre-map) by driving the AGV one time before actual operation. However, in a construction site, the layout changes often due to construction progress. Generating an environment map before each runtime would limit the time available for actual operation. The system Obayashi and SRI have developed needs to only coordinate any changes of two-dimensional markers to adjust route change. This saves a lot of time in actual operation.
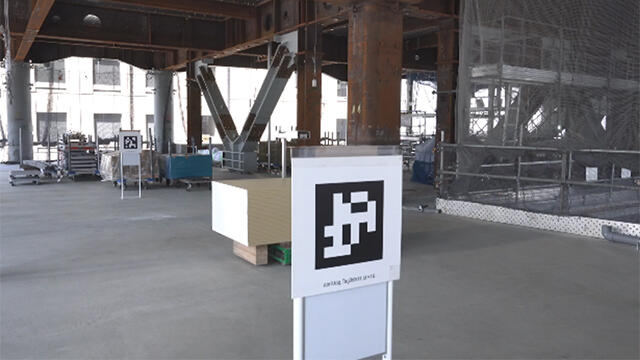
One operator controls multiple AGV collaboration
Since the low floor AGV can enter the construction elevator, the system operates three AGVs and the elevator collaboratively by setting waiting points on the starting and target floor. The system can add additional AGVs matching to construction project size and the amount of material. One operator can monitor all AGVs status through devices like a laptop or tablet.
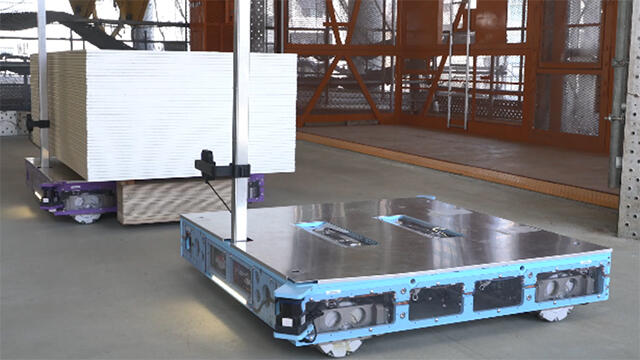
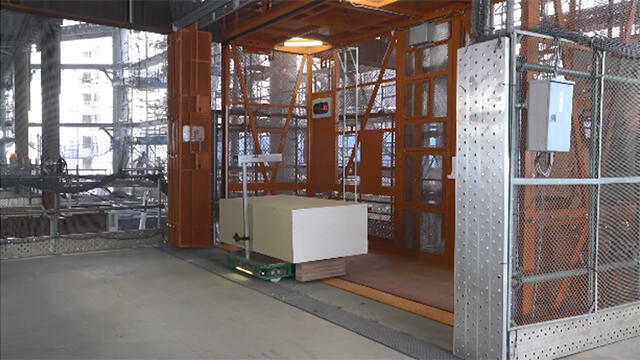
In the future, Obayashi will install the system at an actual construction site and will keep developing and improving the system to carry more material, even more efficiently. Obayashi will continue to polish the autonomous technology to enable their future vision of a construction site where many types of construction robots work autonomously and collaboratively.