Developed OBRIS™: Obayashi Bridge Renewal Integrated Management System
Improves productivity and construction quality in road bridge renewal
-
Civil Engineering
Obayashi Corporation has developed the Obayashi Bridge Renewal Integrated Management System (OBRIS), a cloud-based integrated management system that streamlines operations in each phase of a large-scale expressway bridge renewal project through centralized utilization of data, from the measurement progress of existing structural shapes to the design of new structures, and pre-cast components fabrication, on-site construction, and maintenance and management.
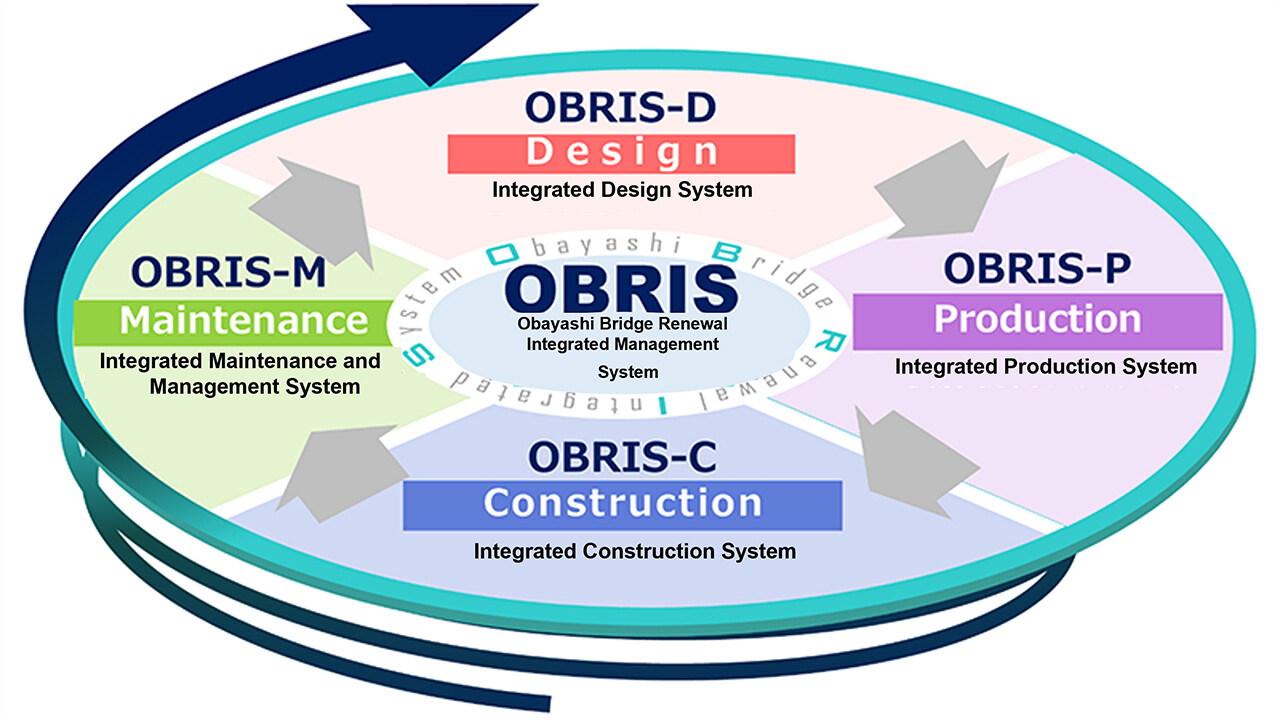
Approximately 70% of Japan's expressway bridges were built 30 years ago, and renewal work is underway in many areas. In order to respond to the increase in construction in the future, the challenge will be how to ensure safety and quality while completing construction as quickly as possible without rework.
The newly developed OBRIS system is an integrated management system that eliminates human error in the data transfer and creation process, and greatly reduces labor and improves efficiency by linking operations on the system, using the 3D model created at the design stage, through to the production of precast parts, on-site construction, and post- construction maintenance.
OBRIS comprises of four integration system modules: D (design), P(production), C (construction), and M (maintenance and management). By linking necessary data for design and construction, it realized labor saving by automating manual operation at each phase and the introduction of construction simulation with digital twins, enabling standardization of each phase, thereby contributing to improving productivity, preventing defects, and ensuring high quality.
The four systems that comprise OBRIS are as follows.
Integrated Design System
The 3D laser scanner or UAV is used to survey the as-built geometry of the existing bridge to acquire point cloud data, to create a highly accurate 3D model that can be used as a reference.
Based on this 3D model, the system automatically allocates new slabs and wall railings according to the road alignment data, and automatically makes cutting arrangements for existing slabs. The conventional manual creation of allocation drawings can be completed immediately by simply entering the allocation conditions, reducing the time required for review to approximately one-tenth of the time required in the past.
In addition, each part can be placed on the 3D model to check for conflicts between parts to avoid design errors.
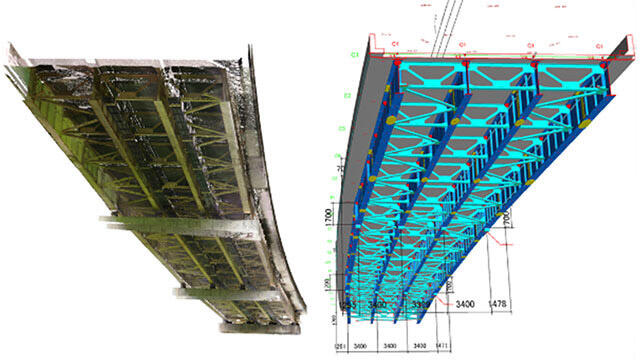
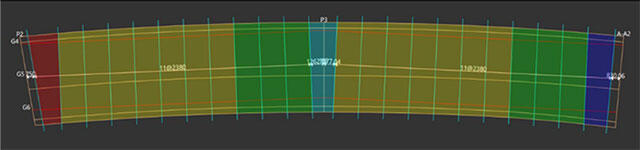
Integrated Production System
For new deck slabs and wall railings, a production drawing (3D model) is created based on design data, such as allocation drawings created by OBRIS-D, with the shape and dimensions of the parts automatically calculated, and then transferred to the factory for production as precast parts. During the production process, quality data is recorded in OBRIS, and the production status is monitored and supervised by cameras to ensure a high level of quality.
The precast parts are measured for shape and size using a 3D laser scanner, and compared to the 3D model at the time of design to make a pass/fail judgment based on dimensional errors.
Furthermore, by placing each part reflecting the measured data on a 3D model and simulating the construction, installation coordinates can be obtained and conflicts between the newly produced slabs and the existing structure can be avoided in advance.
This is the first time in Japan that BIM/CIM digital twin technology has been used in a deck slab replacement project to perform virtual construction in advance.
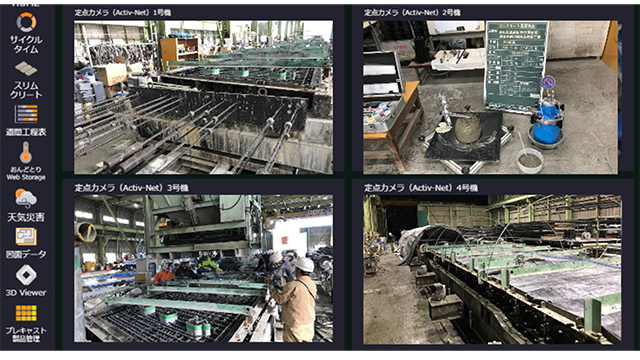
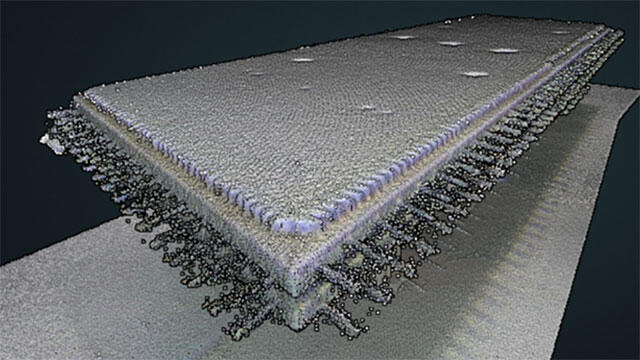
Integrated Construction System
Each part is installed at the construction site based on the installation coordinate data of each part obtained from the construction simulation. The actual installation coordinates are recorded in OBRIS, and feedback is provided to the design by performing a correction simulation to reflect the installation errors. By accurately determining the target installation coordinates for the four corners of the deck slab installation, it is possible to reduce on-site installation time and ensure the alignment of the entire construction area in the cloud.
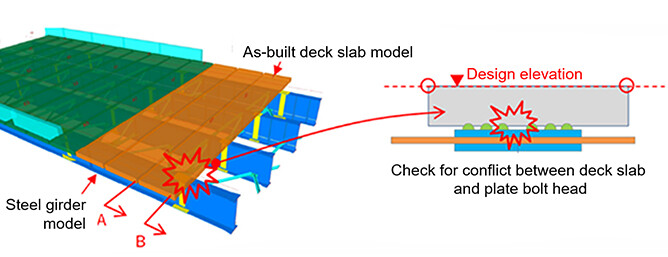
Integrated Maintenance and Management System
All data, from surveying to construction, is stored in the cloud. After construction is complete, the necessary data (design, quality control, as-built dimensions, construction date, and others) can be quickly retrieved from the cloud for maintenance and inspection.
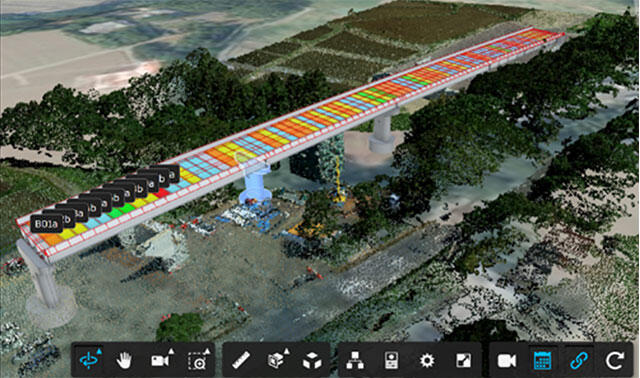
By using this system for bridge renewal, Obayashi will not only improve productivity, but also achieve safe construction and high quality by avoiding various risks, thereby contributing to extending the service life and improving the functionality of existing infrastructure.