Reduction of Roughly 50% in CO2 Emissions from the Manufacturing of Construction Materials for the new construction of the Women's Pavilion at Expo 2025 Osaka, Kansai, Japan
Using low-carbon materials and recycling the facade of Japan Pavilion at Expo 2020 Dubai
-
Others
Obayashi Corporation is aiming to construct a sustainable building for the Women's Pavilion in collaboration with Cartier by Richemont Japan Limited (Cartier Japan) at the Expo 2025 Osaka, Kansai, Japan. Construction, which began on October 23, 2023, features measures to reduce CO2 emissions from the manufacturing of construction materials.
The Women's Pavilion is a collaborative display space supported by Japan's Cabinet Office; the Ministry of Economy, Trade and Industry; Cartier Japan; and the Japan Association for the 2025 World Exposition that encourage visitors to aspire to an equitable and sustainable future through the experiences and perspectives of women. The pavilion's ethos is to design a better world for a brighter future in which equality and respect prevail and every individual can fully express their potential. Preparations are currently underway to create learning and inspirational experiences and exhibits for visitors.
Obayashi has participated in the study teams on the pavilion construction from the basic design stage, working specifically on carbon management. By their very nature, pavilions are used for a shorter period of time than regular buildings and, as such, an extremely large proportion of their CO2 emissions (at least 80%) is emitted during the construction phase, and the production of construction materials in particular (Scope 3 Category 1 emissions in the Greenhouse Gas [GHG] Protocol).
Obayashi has committed to reducing those CO2 emissions from construction materials by approximately 50%, or roughly 469 t-CO2 compared to the use of regular materials. This will be achieved by effectively employing such means as using low-carbon materials for the steel frame and concrete, which make up a large proportion of the building's weight, reusing a facade from a previous expo, and using foundation steel beams repurposed from leased materials.
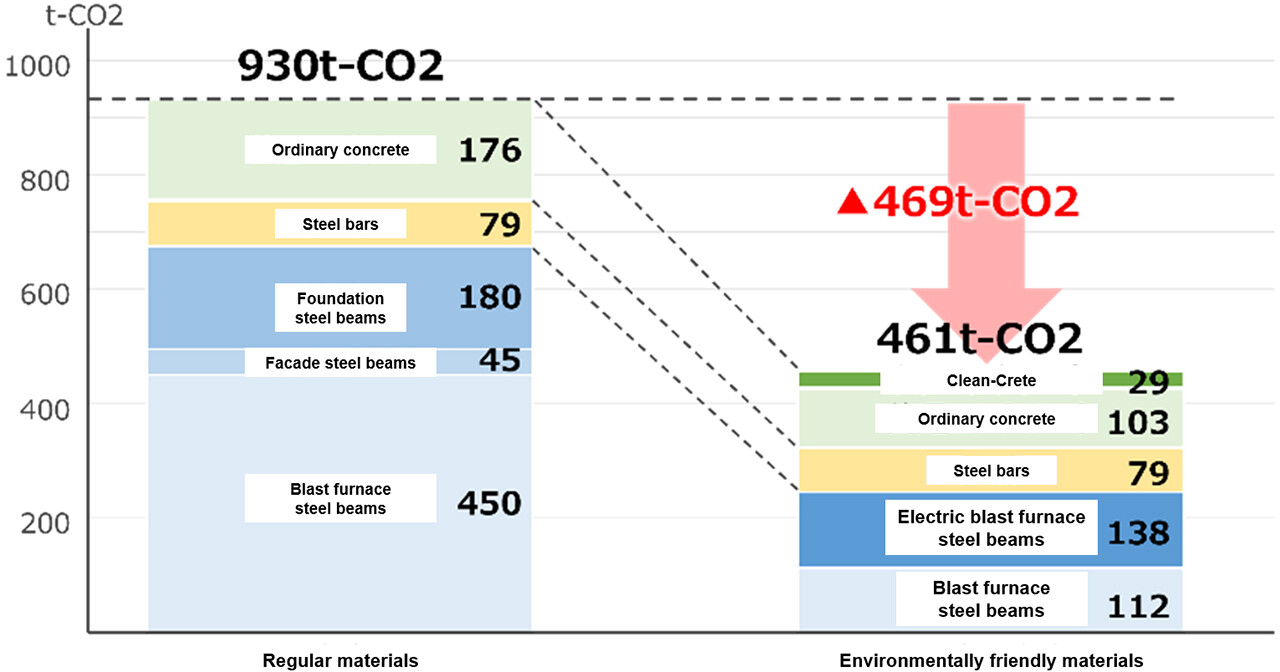
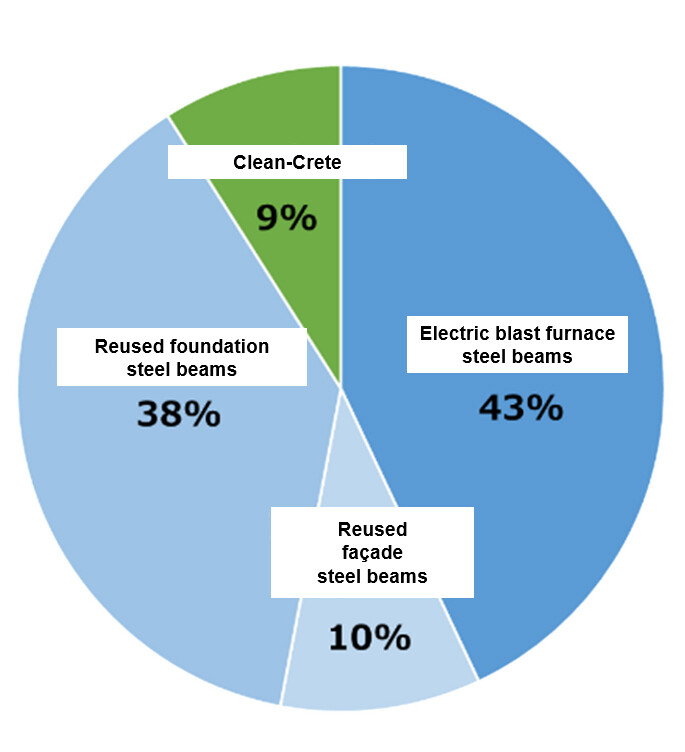
Obayashi is working to reuse the Japan Pavilion facade from Expo 2020 Dubai. Reusing a facade reduces CO2 emissions from the manufacture of materials to zero. However, carefully dismantling and managing the thousands of parts of the facade and reassembling them into a new shape poses its own construction management challenges. Obayashi was in charge of constructing and demolishing the Japan Pavilion at Expo 2020 Dubai, so during disassembly, each part was labeled with a QR code (*1) and managed on the premise that the facade was to be reused. Obayashi's own ProMIE® (*2), a project management system, will be used in the construction of the Women's Pavilion so on-site personnel can use the QR codes to instantly understand where each part is meant to go and assemble the new facade more efficiently.
Obayashi has declared its GHG reduction targets for 2030 of a 46.2% reduction in Scope 1 & 2 emissions and a 27.5% reduction in Scope 3 emissions compared to FY2019 levels. To achieve these targets, Obayashi is developing and commercializing various construction technologies and materials that will encourage decarbonization and help bring about a sustainable society.
Project outline
Project name | The Women's Pavilion in the Expo 2025 Osaka, Kansai, Japan | ||
---|---|---|---|
Location | 1-2-1 Yumeshima-higashi, Konohana-ku, Osaka City, Osaka Prefecture | ||
Client | Cartier by Richemont Japan Limited | ||
Designer・Supervisor | Yuko Nagayama Associates Ove Arup & Partners Japan Limited |
||
Contractor | Obayashi Corporation | ||
Structure | Steel frame | ||
Site area | 2,000.16m² | ||
Building construction area | 1,185.76m² | ||
Total are | 1,708.38m² | ||
Construction period | New construction: From October 23, 2023 to January 31, 2025 Demolition: From November 1, 2025 to April 10, 2026 (planned) |
Rendering of completed building
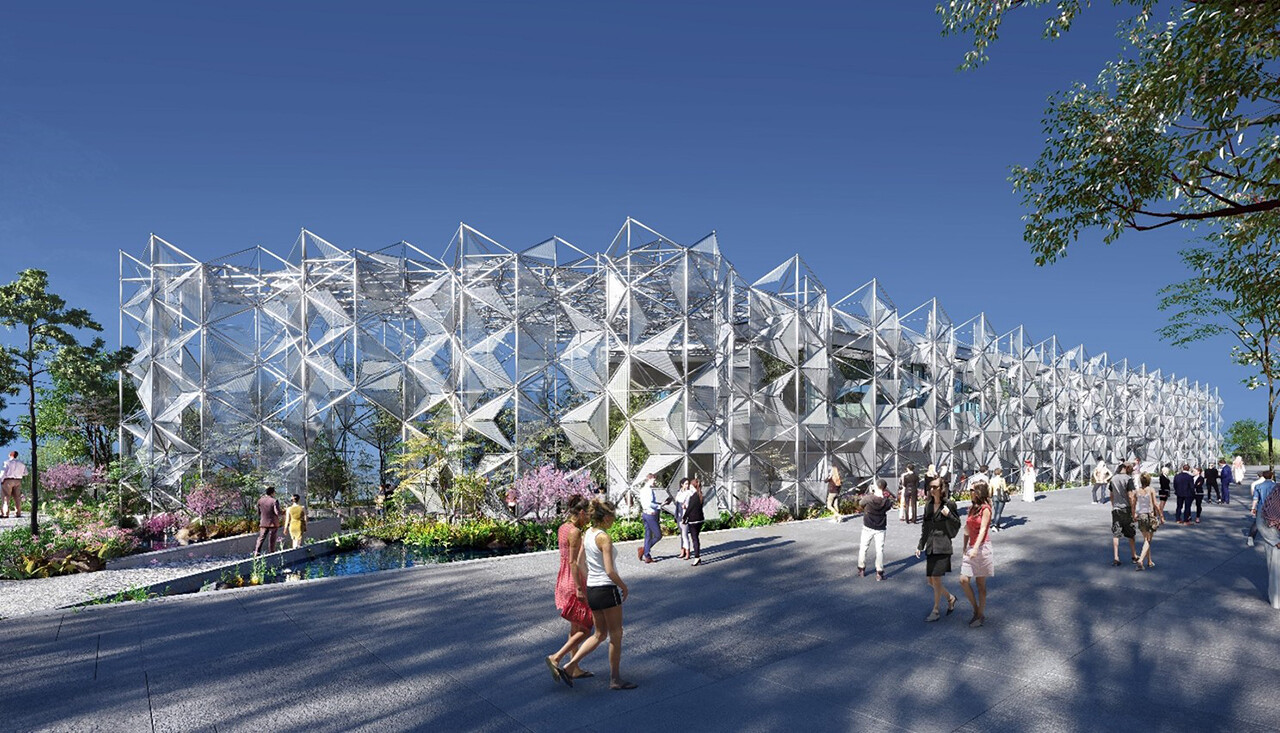
Key carbon management initiatives
- Replacing blast furnace steel beams used as key frame components with electric furnace steel beams
Roughly 75% of the pavilion's main steel frame components are made from electric furnace steel, which reduces CO2 emissions by approximately 200 t-CO2. - Reusing the Japan Pavilion facade from Expo 2020 Dubai
Making the facade materials from scratch would generate approximately 45 t-CO2, but reusing an existing facade will cut CO2 emissions to zero. - Leasing earth-retaining materials to use as foundation steel beams
Newly manufacturing foundation steel beams would produce approximately 180 t-CO2 emissions, but repurposing leased earth-retaining materials used on construction sites and for other purposes will reduce CO2 emissions to zero. When the pavilion is dismantled, the foundation beams can once again be used as retaining materials. - Using low-carbon Clean-Crete for the building foundations
Obayashi's own Clean-Crete®, (*3) which is ranked No. 1 in low-carbon concrete used in the construction industry, will be casted into the building foundations. Using Clean-Crete in place of ordinary concrete can slash the building's embodied carbon by roughly 44 t-CO2, or 60%.
Managing reused materials
The facade is a three-dimensional frame comprising 2,053 spherical pieces, or nodes, and 195 different types of rod-shaped parts, or tubes.
To reassemble, each part must be placed in its designated position. However, because there is an enormous number of parts, it would be very complicated to try and reassemble them exactly as they are after having been disassembled and stored when Expo 2020 Dubai concluded.
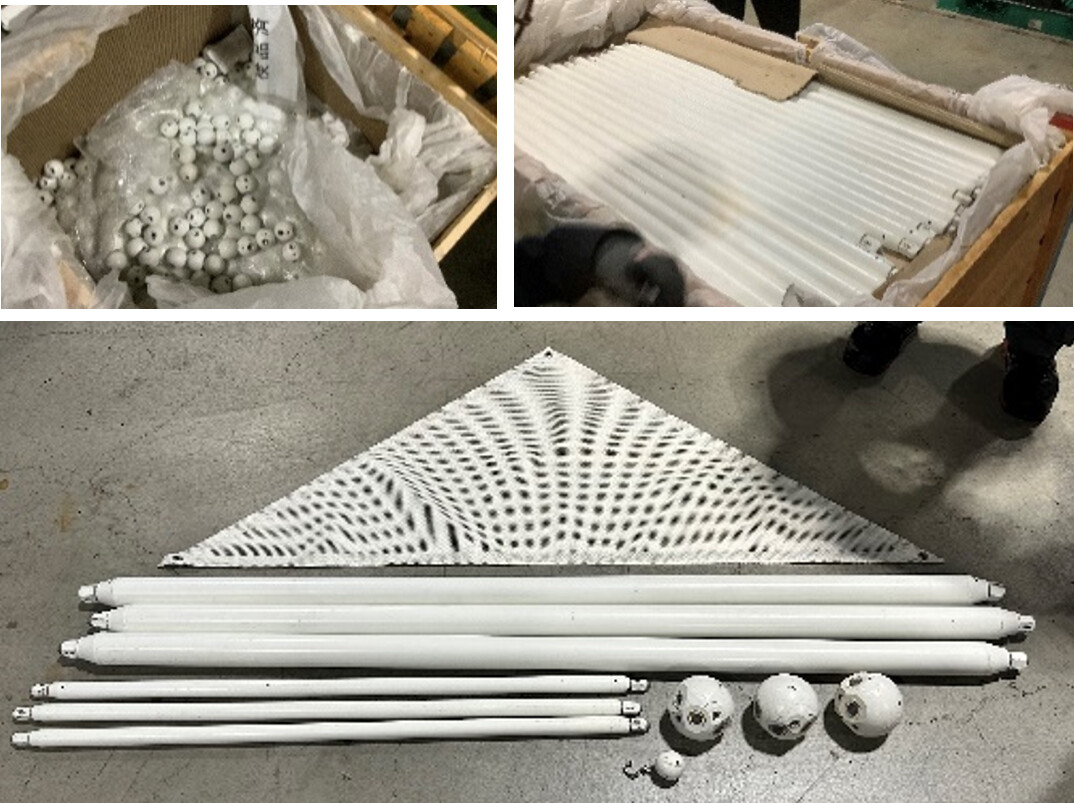
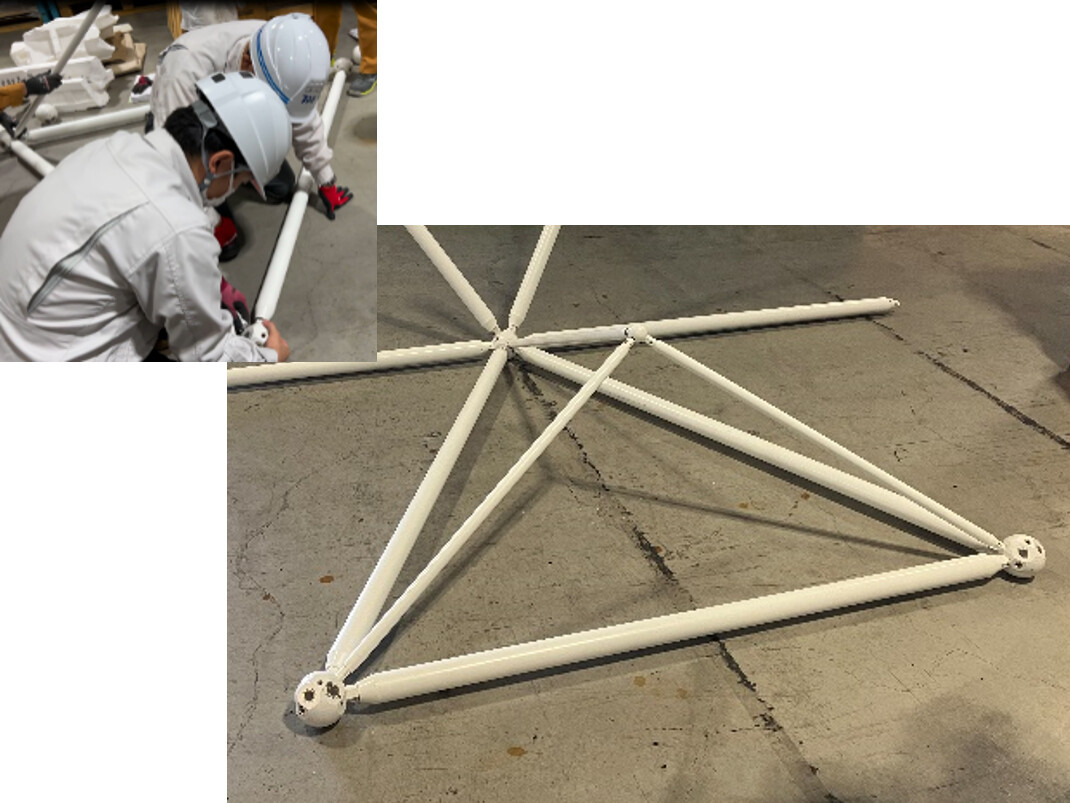
This problem can be solved by using Obayashi's own ProMIE project management system. Using the ProMIE system, the unique identification number engraved on each facade piece was linked to the scheduled delivery date and other parts-related construction information entered into the BIM model, and a QR code was affixed to each part to make it easy to identify. This resulted in an approximately 25% reduction in the amount of time spent sorting parts, ascertaining where they were meant to go in the new construction, and carrying and assembling the parts in situ.
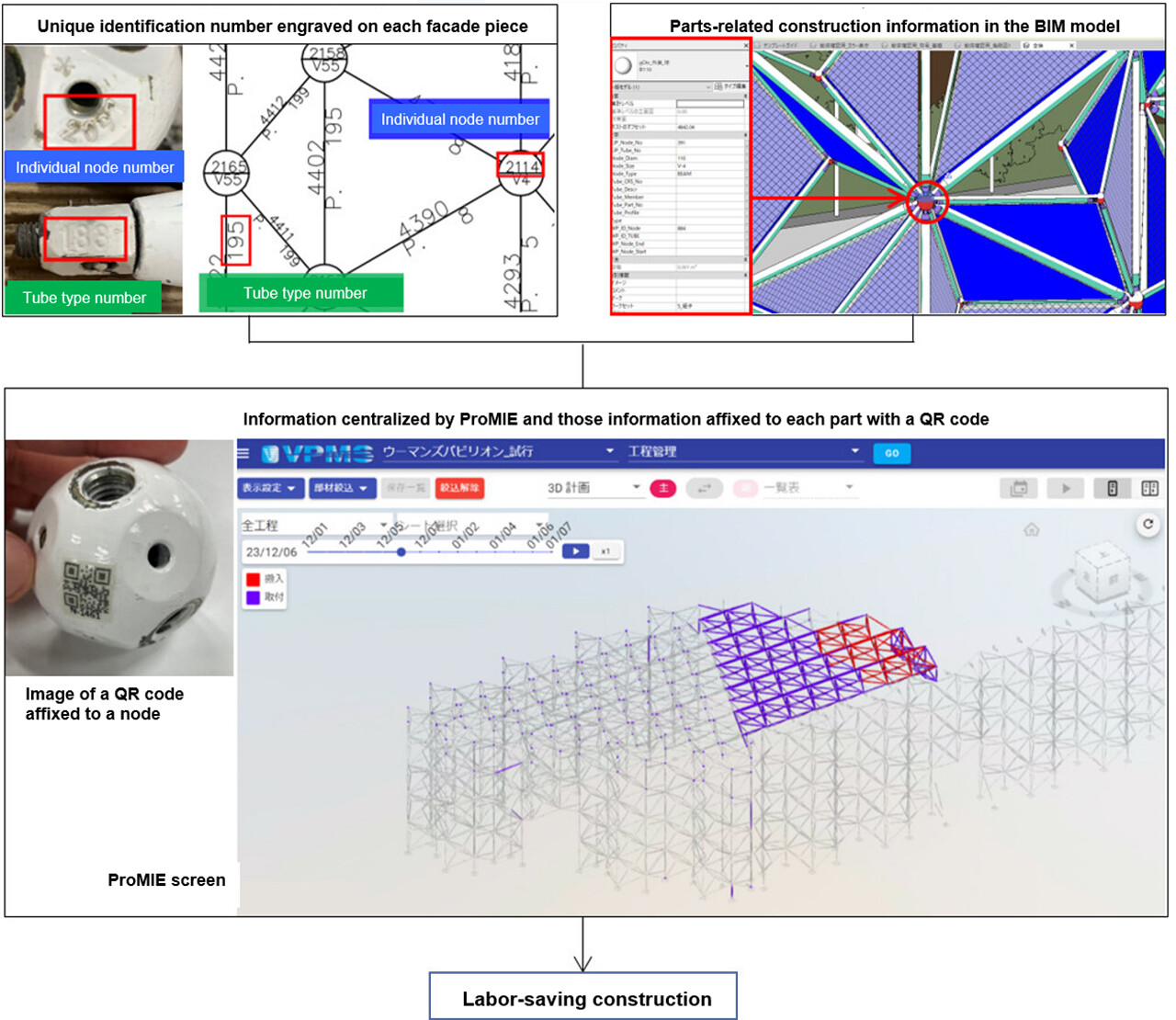
- *1 QR Code is a registered trademark of DENSO WAVE INCORPORATED
- *2 ProMIE
A system which can visualize project management in an integrated environment
- *3 Clean-Crete
A type of concrete developed by Obayashi which can reduce CO2 emissions by a maximum 80% compared to ordinary concrete by replacing cement with industrial by-products such as fine powdered slag from blast furnaces (a by-product of steel manufacturing) and fly ash (a by-product of coal-fired thermal power generation), which do not generate much CO2
For further press inquiries please contact
Contact us