Japan's First TLP-type Floating Structure for Offshore Wind Installed in an Actual Sea Area
Demonstration experiment commences for a floating foundation structure that combines considerations for fisheries and higher power generation efficiency
-
Technologies
Obayashi Corporation has installed Japan's first(*1) TLP (Tension Leg Platform) type floating structure for offshore wind, located in a sea area 3 km off the coast of Iwaya, Higashidoori Village, Shimokita County, Aomori Prefecture. A one-year observation of its behavior has begun since July, 2024. The "floater body and mooring system" in this demonstration has completed classification inspections by Nippon Kaiji Kyokai (ClassNK) and has been granted the classification of "Ships of special type" under the Ship Safety Law.
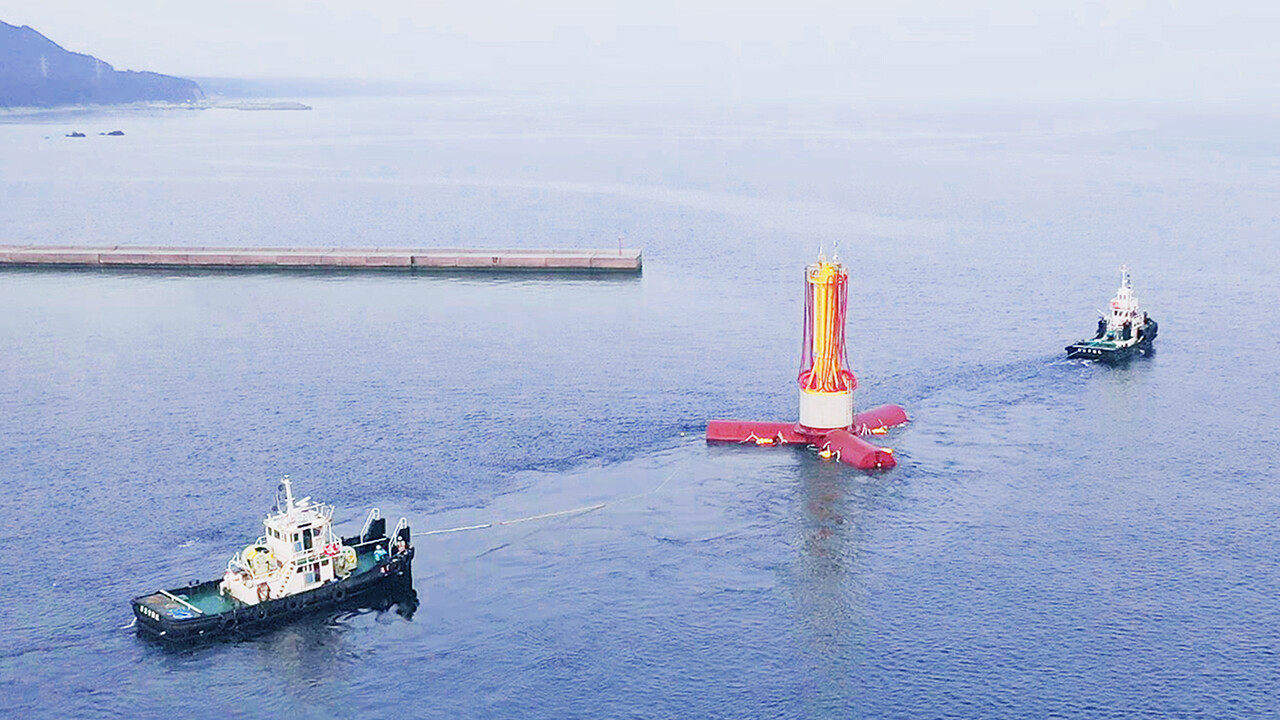
-
Floating structure launching
-
Floating structure in place
Development Background
There are two main types of foundation (support) structures(*2) used in offshore wind: the fixed type, which supports wind turbines by constructing a foundation on the seabed, and the floating type, which a wind turbine is installed on a floater foundation in the sea. Currently in Japan, most offshore wind power foundation structures are fixed types; however, since fixed structures are more suitable for relatively shallow waters, it is expected that floating structures suitable for deep water areas will be introduced, as these areas are more prevalent in Japan.
While the catenary mooring system for spar-type and semi-submersible type floaters is being put into practical use for floating structures, challenges remain, such as significant motion of the floater and lower power generation efficiency. On the other hand, TLP-type floating structures are expected to offer high stability against motion and improved power generation efficiency. They also occupy a smaller area of the sea, resulting in minimal impact on the fishing industry. However, TLP-type structures are generally considered difficult to install. Although they have been successfully implemented in offshore oil fields, there is no construction track-record for offshore wind power foundations in Japan, and they have not yet been commercialized.
Obayashi is engaged in the development of technologies for all types of foundations for offshore wind power, including both fixed and floating structures. We have focused on the development of TLP-type floating structures, which are promising in the future, and have steadily increased our technological maturity, such as obtaining the Approval in Principle (AiP) from Nippon Kaiji Kyokai in 2018.
Using Obayashi's unique installation method (patent pending), we have completed installation of a demonstration TLP-type floating structure, which is one-fifth the size of a floater designed to accommodate a 15 MW-class wind turbine, in an actual offshore sea area. We have also commenced a one-year observation (from July 2024 to July 2025) to monitor the dynamic motion behaviors of the floater body and the changes in mooring material tension under actual wave conditions.
Details of the Demonstration Experiment
Adoption of a Hybrid Structure
The TLP-type floating structure is fixed with tension mooring materials called tendons and anchors installed on or into the seabed, whereby it functions as a foundation structure by utilizing the tension generated by the buoyancy of the floater body. In this demonstration experiment, we have adopted a hybrid structure made of reinforced concrete and steel members to reduce the production costs and to facilitate mass production of the floating structure. In addition, low-creep, high-strength synthetic fiber ropes have been used for the tendons to verify their applicability for the TLP-type floating structure.
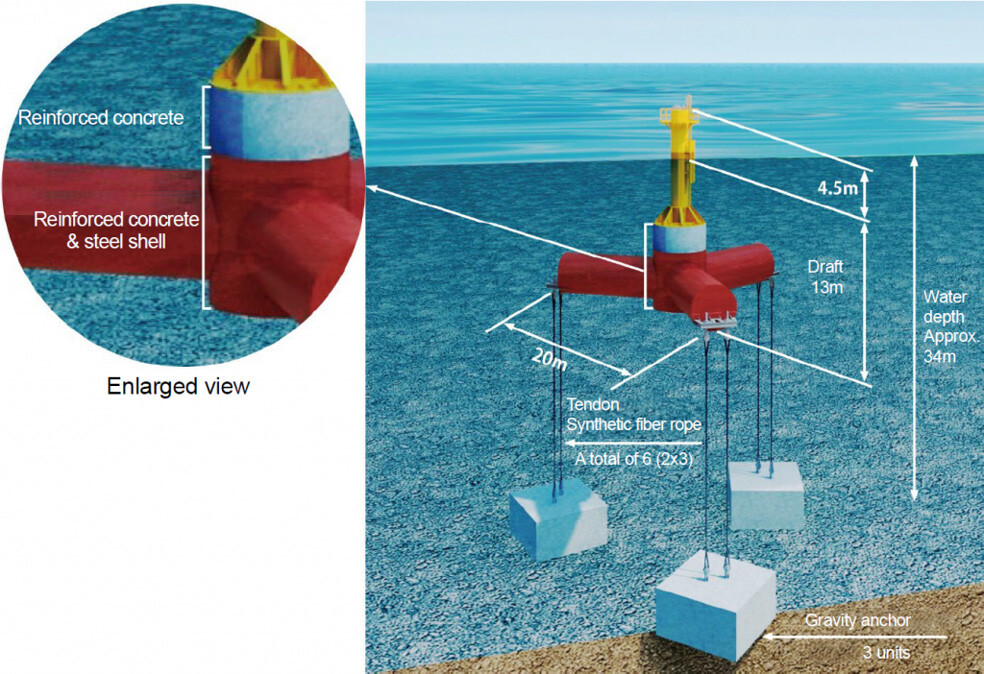
Establishment of Installation Methods
The TLP-type floating structure poses some challenges as it becomes temporarily unstable during installation. To overcome this, Obayashi has established a method for installing the floating structure while maintaining its stability without using a large, specialized vessel. (patent pending)
Verification of Structural Validity
Through a one-year of observation period, the motion stability under actual wave conditions will be confirmed and the watertightness of the concrete floater body will be verified, thereby confirming the durability of the TLP-type floating structure.
Future Prospects
Although the current floating structure is not equipped with a wind turbine, Obayashi advances technology development toward commercialization by conducting further demonstration experiments using a floating structure equipped with a wind turbine in real sea conditions.
Going forward, Obayashi will continue to contribute to the realization of carbon neutrality through the spread of renewable energy, including offshore wind power, by promoting technological development towards the realization of social implementation of TLP-type offshore wind power facilities after 2030.
- *1 Our own research (July 2024) indicates that "the installation of TLP-type floating structures for offshore wind in actual offshore sea areas" is the first in Japan.
- *2 Characteristics of foundation types for offshore wind power facilities
Foundation type | Monopile | Spar type | Semisubmersible type | TLP type |
---|---|---|---|---|
![]() |
![]() |
![]() |
![]() |
|
Structure type | Fixed base | Floating | Floating | Floating |
Mooring system | - | Catenary | Catenary | Tension |
Applicable water depths | Shallower than 50m | Over 100m | Over 80m | Over 80m |
Key features | Simple structure; small seafloor area occupied | Simple structure; large seafloor area occupied | Complex structure; large seafloor area occupied | Low floater motion and high power generation efficiency; small seafloor area occupied |
For further press inquiries please contact
Contact us