3Dプリンターとロボット打設技術によるコンクリート構造物の自動化施工システムを開発
プレキャストコンクリートの製造における省力化と工程短縮を実現しました
-
プレスリリース
株式会社大林組(本社:東京都港区、社長:蓮輪賢治)は、セメント系材料を使用した3Dプリンターによる外殻製造技術と、コンクリートの吹き付けまたは流し込みをロボットにより行う技術を用いた、コンクリート構造物の自動化施工システムを開発しました。また、本技術を適用し、日本ヒューム株式会社(本社:東京都港区、社長:大川内稔)とプレキャストコンクリートブロック(※1)の製造に成功しました。
従来、コンクリート構造物の製造においては、型枠の組み立て・解体やコンクリートの打設など、多くの人手が必要でした。また、大型のプレキャストコンクリート製品は、鋼製型枠が特注生産となるため、設計から納品までの期間が約10ヵ月と長いうえ、製造コストが高くなることが課題でした。
そこで、大林組は、セメント系材料を使用して3Dプリンターでプレキャストコンクリートの外殻をプリントし、コンクリートの打設経路をプログラミングしたロボットアームで、コンクリートを吹き付けまたは流し込むことにより施工の自動化を実現しました。これにより、鋼製型枠の製作・組み立て・解体作業が不要となり、プレキャストコンクリートの製造における省力化と工程短縮および型枠製造のコストダウンを実現しました。
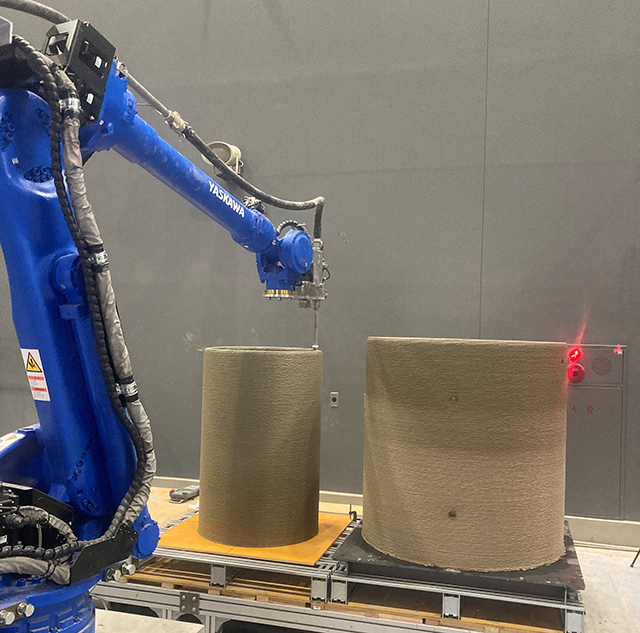
また、3Dプリンターは、設計図からダイレクトにロボットの制御情報を生成できるので、複雑な型枠や多品種の型枠が必要な構造物を構築できます。そして、3Dプリンターでプリントした外殻はコンクリートと一体化しており、従来手法で製造したプレキャストコンクリートと同等の強度を有していることも確認しました。
本システムの特長は以下のとおりです。
自動化施工による省力化
本システムでは、3Dプリンターで外殻をプリントすることにより、型枠の組み立て作業や打ち込み後の解体作業が不要となります。また、数人の作業員で行っていたコンクリート打設をロボットアームが自動で行うことにより、従来の3分の1まで省力化を実現しました。
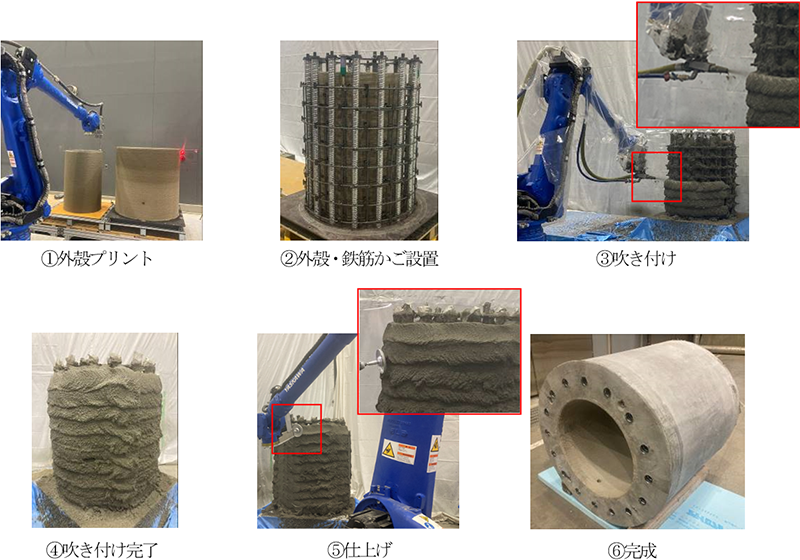
プレキャストコンクリートの製造工程を短縮
3Dプリンター製の外殻は鋼製型枠より短期間で製造できるうえ、次の製作に型枠を転用するまでの待ち時間が発生しないため、プレキャストコンクリートの製造工程を大幅に短縮できます。特注の鋼製型枠で複数のプレキャストブロックの製造が必要なプレキャストケーソン基礎工事では、ブロックの製造工程が、従来の約10ヵ月から約2ヵ月間短縮できます。
また、外殻のプリントやコンクリートの打ち込みをロボットアームが自動で行うので、24時間体制の製造が可能となり、さらなる製造工程の短縮を実現します。
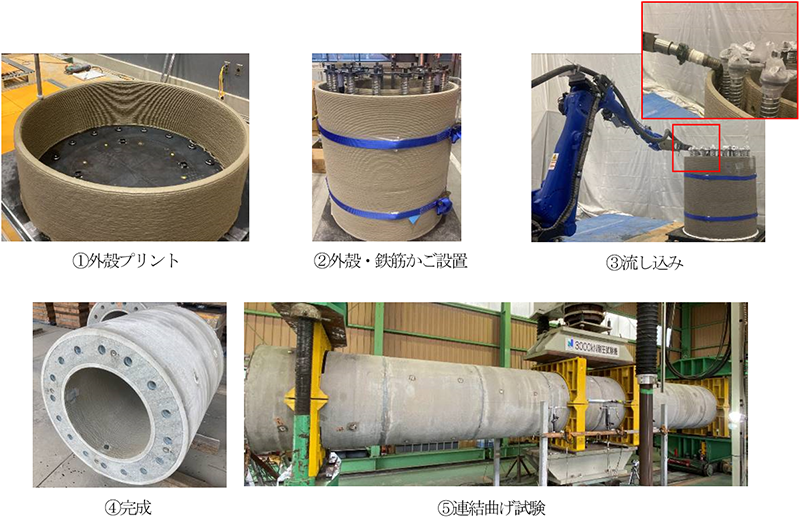
型枠の製造コストを削減
3Dプリンター製の外殻は、3Dプリンターの費用や人件費などを含んで比較した場合でも、鋼製型枠より安価に製造でき、型枠費を最大50%低減することができます。
大林組は、今後も3Dプリンターとロボットアームを使用したコンクリート構造物の製造に対する研究開発を継続し、実工事への適用を図るとともに、将来的には施工現場における自動化施工を実現します。
- ※1 プレキャストコンクリートブロック
工場で製造した建物の基礎となる円筒形のRC造ブロック。積み重ね、鉄筋やPC鋼棒で一体化して構築したものがプレキャストケーソン基礎となる
以上
この件に関するお問い合わせ先
大林組 コーポレート・コミュニケーション室 広報課
お問い合わせフォーム
プレスリリースに記載している情報は、発表時のものです。