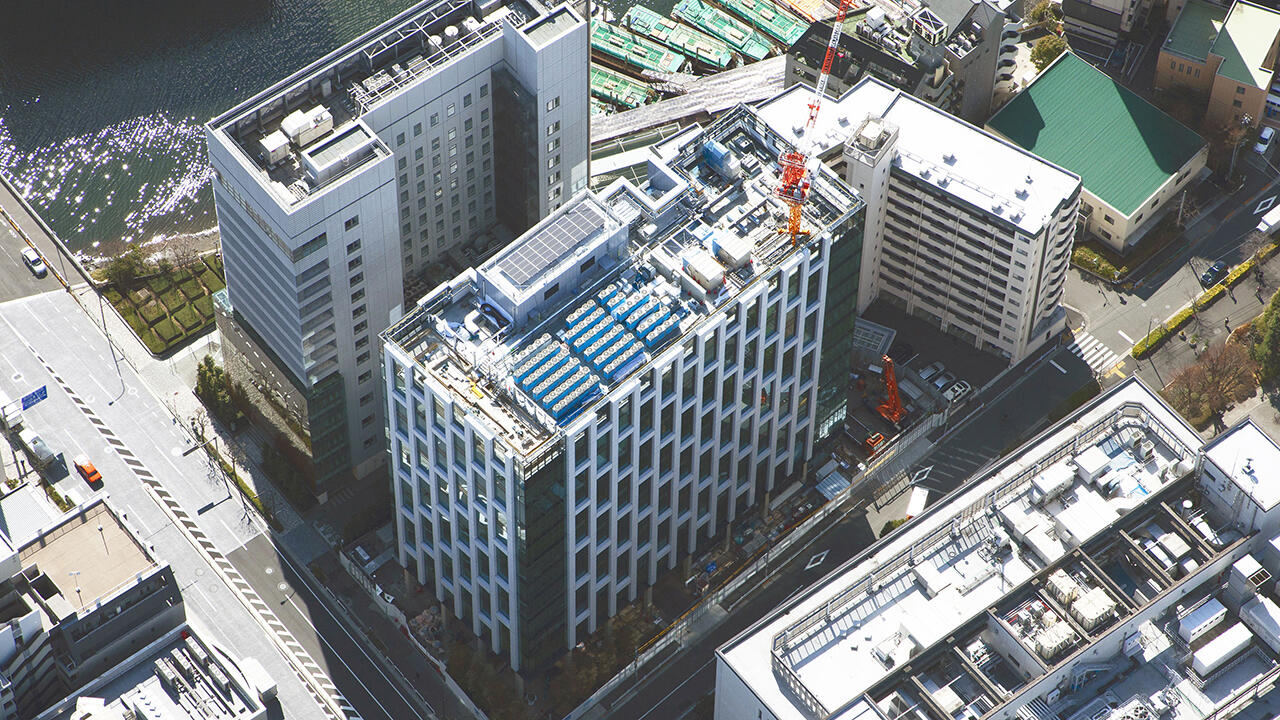
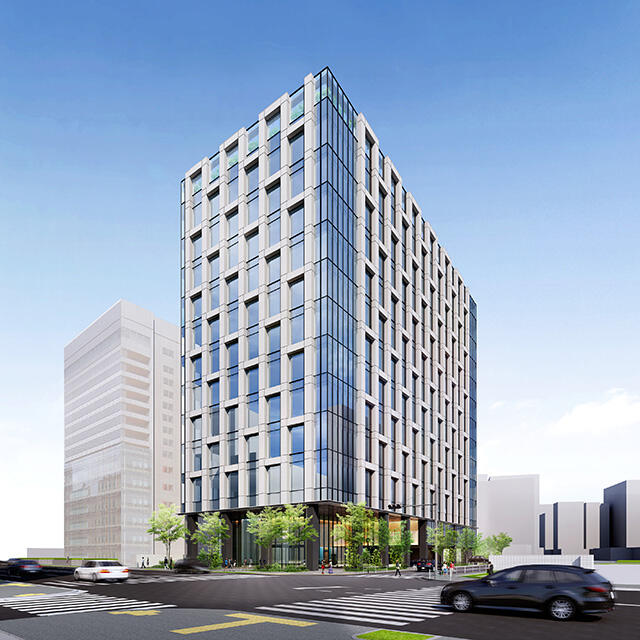
東京・品川駅から約800mの場所に、地下1階・ 地上12階建ての中規模免震ビルの工事が進む。
建物の発注者は、大林グループの不動産・開発事業の中核を担う大林新星和不動産だ。発注・設計・施工をすべて大林グループで手がけるメリットを最大限活用し、ロボット溶接、自動運搬、MR(複合現実)などの新技術を可能な限り導入。大林組は、高効率化施工に向けた検討や実証を行いながら、工事に取り組んでいる。計画のスタート時から「建物の付加価値の向上×生産性の向上」をめざし、合理的な構造計画を検討した。
無柱大空間を実現する構造計画
デザイン・構造・設備を一体化
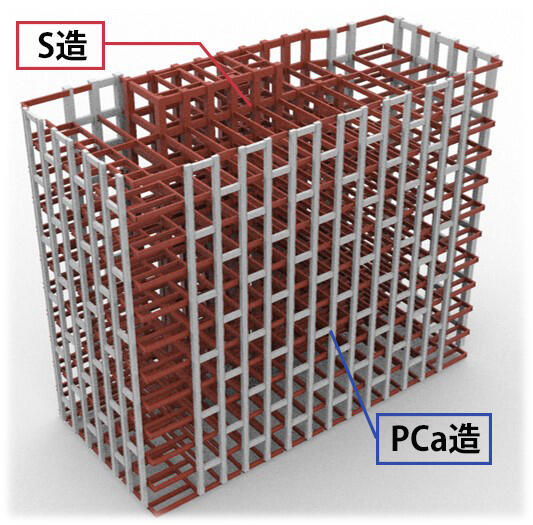
今回の工事では、高いデザイン性と耐震性能を実現するため、プレキャスト鉄筋コンクリート(PCa)造と鉄骨(S)造を組み合わせたハイブリッド構造を採用した。PCaは、現場で型枠を用いてつくるのではなく、あらかじめ品質管理の行き届いた工場で製作される。そのため、品質が均一で精度の高い安定した部材となる。
外観を特徴付けているのは、PCaの柱と梁による外郭架構だ。構造体と外装部材を兼用した柱と梁の内側には、給排気ユニットなどを組み込んだアルミカーテンウォール(ACW)が入る。デザイン・構造・設備を融合したパーツを積層することで印象的な外観をつくり出すとともに、LRV工法(PCa部材を現場で組み立てる)を採用して組み立てを簡略化し、生産性の向上を図る。
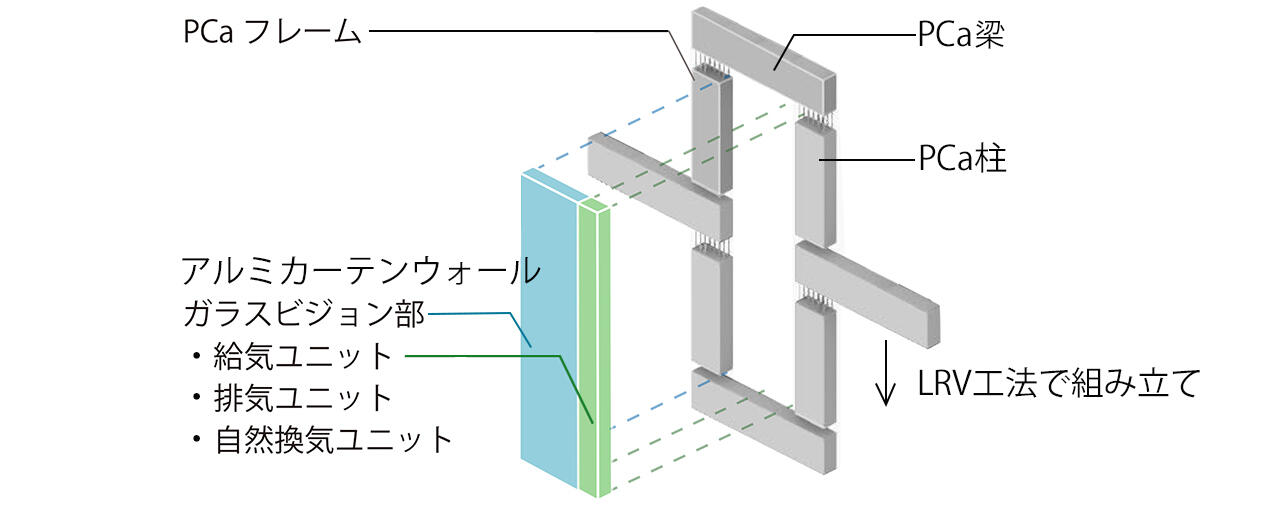
PCa柱は、断面の形を一般的な正方形から長方形に偏平させ、PCa梁と同幅になるように変更。室内側の柱と梁が一直線になるようにして、フロアの有効空間を最大限に確保した。さらに、建物のコア部分に超高強度CFT柱(コンクリート充てん鋼管構造)、ロングスパン鉄骨梁(S梁)を適用することにより、無柱大空間を実現した。
PCa造の外部架構とS梁の接合部は現場の作業が安易になるボルト接合に変更した。これは、免震建物としての構造性能評価も取得している。さらに、PCa部材は全て工場で塗装した。工事事務所所長の藤平はハイブリッド構造による生産性向上の効果を「現場での鉄骨溶接箇所を減らし、部材の小型化と軽量化で作業効率を高めました。PCa部材を組み立てた時点でほぼ外装仕上げが完了となるので、工程の短縮にもつながりました」と語る。
-
PCa柱の断面図(上)。一般的なPCa柱型は室内側に突出する(左下)が本工事では室内側に突出しない(右下)ため 広いスペースを確保できた
-
断面を長方形に偏平させたPCa柱
精度の高い施工と作業効率を追求
工事における施工精度の確保と作業効率向上の実現に向け、施工計画などの検討と検証を重ねた。PCa外郭架構とACWで構成される外周の構築では、水平・垂直を正確に管理するため3次元計測を採用した。
狭あいな場所において柱、梁を揚重するタワークレーンは、建物の中央に設置する計画とした。クレーンを設置する3階床レベルの構造フレームを最優先で構築し、早期にクレーンを設置したことで鉄骨取り付け精度が高まり、作業効率も上がった。
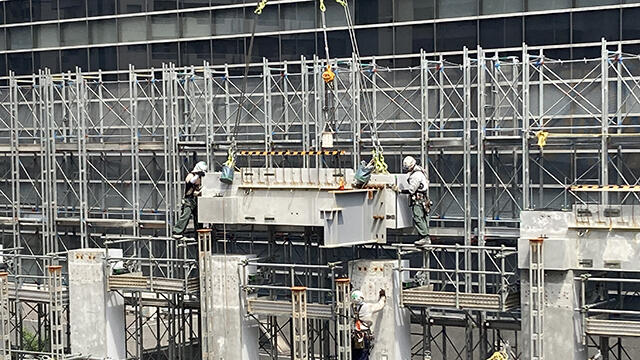
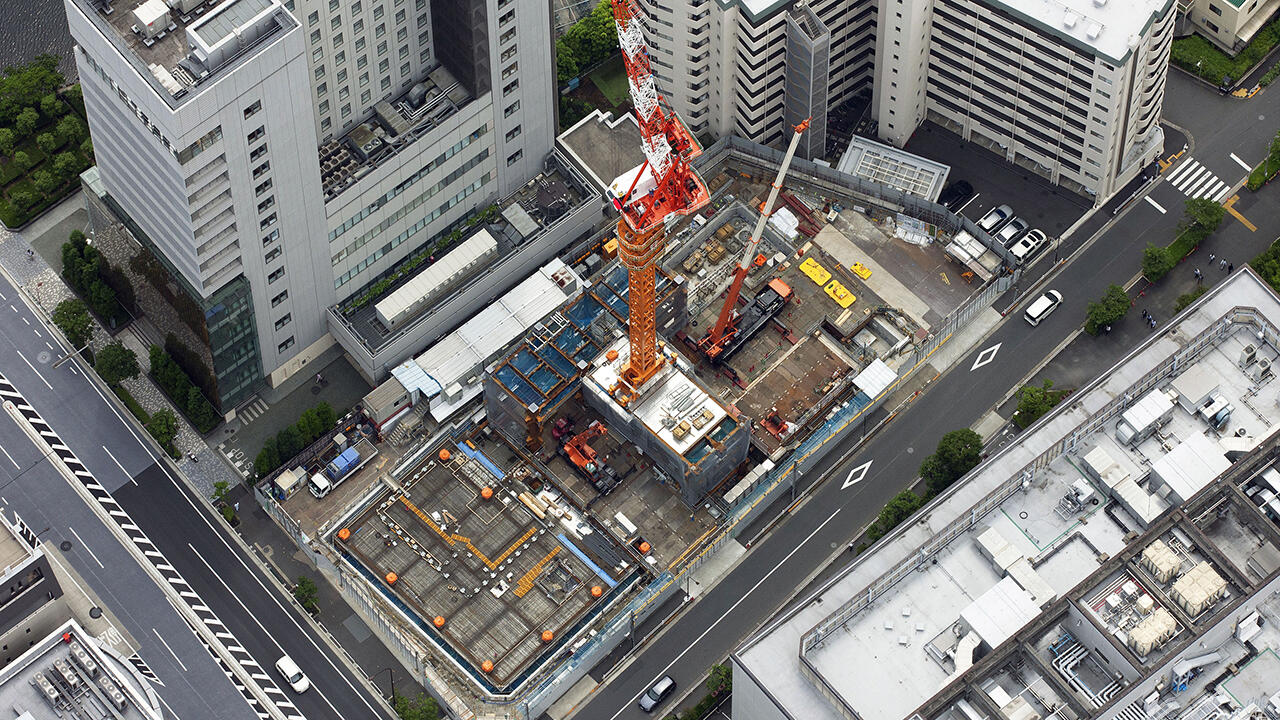
生産プロセスの見直し
フロントローディングとBIMモデル
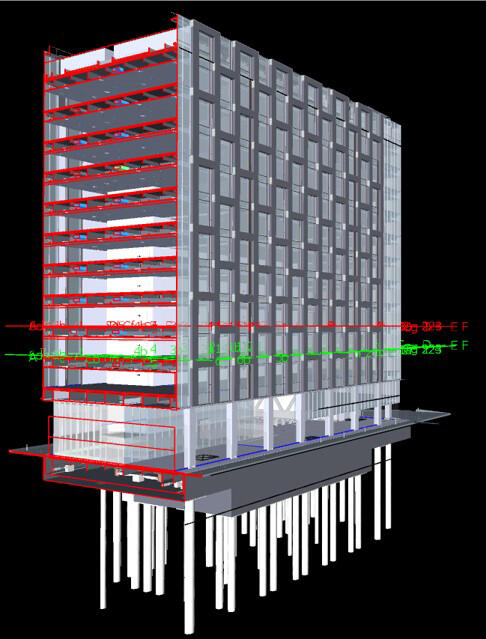
大林組は、今回のプロジェクトでフロントローディングを導入している。フロントローディングとは、コンセプトや方針、建物イメージを決める基本設計の完了後、直ちに、工事事務所が各部門と連携・協力し、それぞれの非効率な点や無駄を見直して業務の質と効率性を高めることだ。これにより、プロジェクトを成功に導く最適解を追求することができ、施工性を考慮した実施設計が可能となった。
加えて、BIMモデルを積極的に活用。実施設計では意匠・構造・設備の設計検証を行い、見積り段階では積算数量の算出に利用した。着工後に導入した次世代生産設計図は、外形情報や部材間の位置関係などの情報をBIMモデルから直接引用したもの。これにより、設計変更のたびに2次元の生産設計図を作り直すという従来行っていた作業がなくなり、作図の省力化を実現した。
所長の藤平は「生産設計図の作成スピードが速くなり、着工から3ヵ月で総合図について発注者と合意できました。施工においても例えば、高さ方向での部材同士の干渉位置など、平面図では分かりづらかった部分を事前に3次元で確認できるので、手戻りが少なくなりました」とBIMモデル利用のメリットを語った。
固定式総足場から、スライド式の連層足場へ
-
PCa柱と梁の接合部のグラウト注入および目地シールの施工に際し、外部作業用の足場が必要となる。
もともと計画されていた高さ約60mの総足場工法をフロントローディングによって、直上にスライドしていく連層足場に変更。これは、総足場を組めない高さ100m以上の高層大規模案件のデータ蓄積としての役割も担う。
連層足場にしたことで、スライド後に低層階の作業を進められ、早期に外構工事に着手することが可能となった。
-
生産性向上のモデル現場として
仮想現実、自動化、ロボット化などの技術を検証
鉄骨の製品管理には、MR(複合現実)を活用した施工管理アプリ「holonica™」を採用した。設計図書や仕様書などから必要な情報を選別し、施工箇所と照らし合わせてその適否を判断するには、従来、経験と多くの時間が必要だが、アプリを活用し、業務プロセスを簡略化を試みた。
さらにMRで外装のデジタルモックアップによる発注者へのプレゼンテーションを実施した。通常カーテンウォールは実物大モックアップを製作するが、多大なコストがかかる。BIMモデルがあったことや現場の敷地が狭あいだったことから、デジタルモックアップの採用に至った。MRは、空間のイメージを共有でき、実物大モックアップ以上の表現力を発揮する。発注者からも好評だ。
現場ではこのほか、現場ロボット溶接工法や耐火被覆吹付けロボット、自動搬送システム(AGV)も適用。技能工との協業体制やコスト面の検証を重ねた。
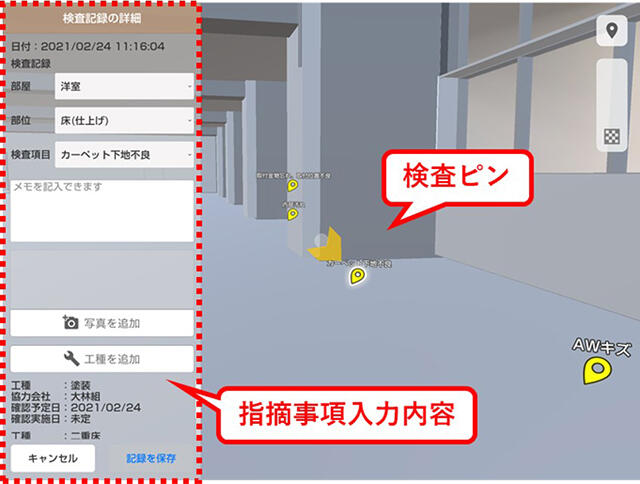
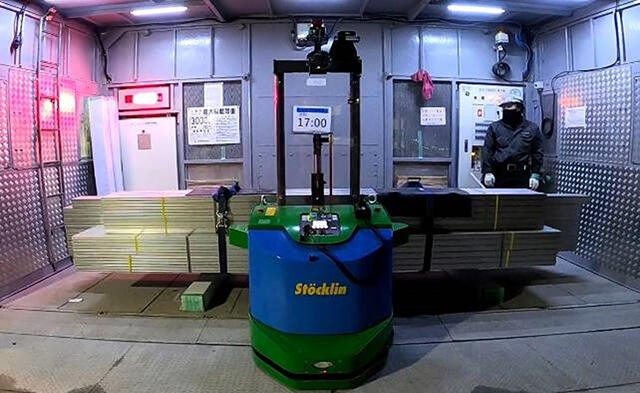
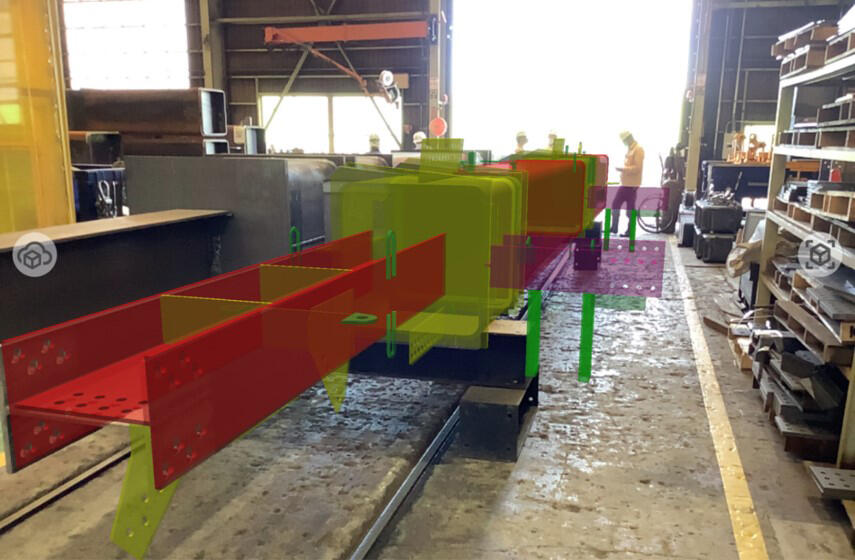
成果を伝え、次に活かす
「導入するさまざまな技術の検証とフィードバック」が本工事に課せられた最大の課題だ。
外郭に構造体と外装材を兼用するという特異性を持ち、高効率な生産性を追求するため、フロントローディングをはじめ、さまざまな自社技術を積極的に取り入れている。通常は採用しない技術も取り入れたことで、中規模事務所ビルの設計施工の案件として一つのモデルケースにもなっている。
所長の藤平は「ハイブリッド構造の高層化に向けた足がかりになること、採用した技術のメリットだけでなくデメリットもフィードバックすることが重要。生産性向上につながる成果を今後の案件に伝えることが、私たちの使命です」と語った。
本工事の最終的な結果検証はこれからの課題だ。さまざまな技術を取り入れ、検討・実証に取り組んだ成果が、大林グループの未来を拓くカギになるに違いない。
(取材2022年3月)
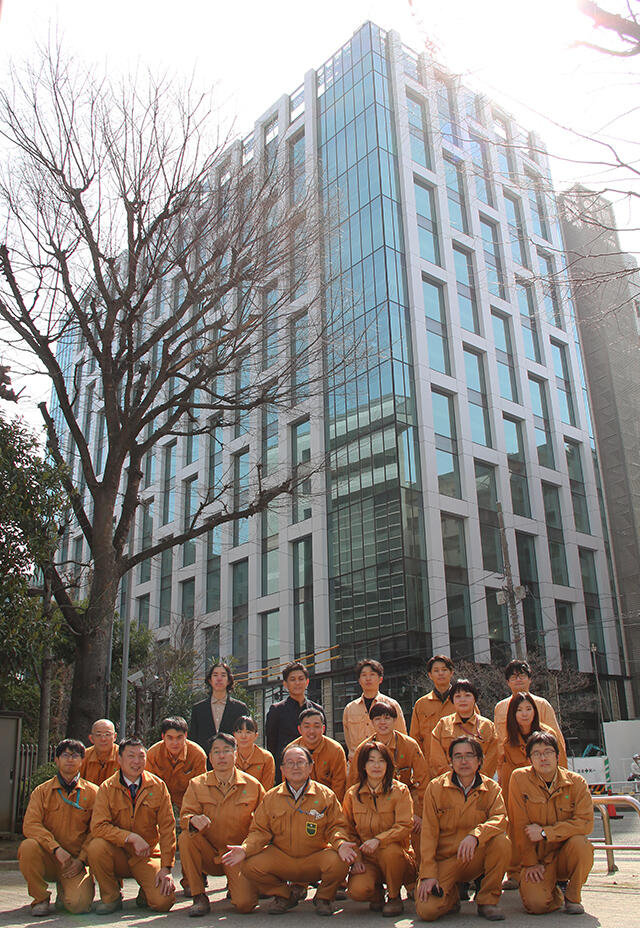
工事概要
名称 | (仮称)港南2丁目プロジェクト |
---|---|
場所 | 東京都港区 |
発注 | 大林新星和不動産 |
設計 | 大林組 |
概要 | S造・RC造、免震構造、12F、PH付、延1万6,888m² |
工期 | 2020年9月~2022年7月 |
施工 | 大林組 |