昭和30年代、40年代を通じて仮設材の鋼製化が進み、建設機械が普及し、また施工の省力化に向けプレハブ化や現場作業のシステム化などが進んだ。当社もそれらをいち早く導入し、各現場に定着させることによって、ビルの高層化や大規模化という社会のニーズに対応していった。こうして50年代に入ると、もはや一般の建築現場の風景を一変させるような目新しい施工技術の開発は見られなくなってきた。
こうした状況にあって、この時期の当社の代表的な建築技術の開発は、エネルギー関連技術や先端技術に対応した開発を中心に進められた。
●プレストレストコンクリート製原子炉格納容器(PCCV)
原子力発電所で最も大切な原子炉を収納し、万一の場合でも放射性物質を外に出さない「いれもの」が格納容器である。わが国ではこれまで格納容器は鋼製でつくられてきたが、発電容量の大型化に伴い、50年代の初めから格納容器としての大型化が可能なプレストレストコンクリート製原子炉格納容器(PCCV{注})の導入が検討され始めた。
PCCVの概略寸法は高さが基礎上面より約65m、内径43m、シリンダー部厚1.3mの巨大な構造物であり、構成は内側に気密性を受けもつ鋼製のライナーと外側のプレストレストコンクリートから成る。日本のPCCVでは鉄筋はD51(直径51㎜)、1本当たり1,000t級のテンドン(緊張材)が使用されている。
格納容器の主な機能は気密性、耐圧性であるが、PCCVでは放射線の遮蔽効果も期待できる。
PCCV基準化のため50年8月、通産省に原子力発電用コンクリート容器技術基準検討会が発足し、設計の基準化と技術の実証性に取り組んだ。
PCCVの技術は米国、フランスを軸として開発が進められてきたが、わが国への導入には耐震性を中心に外国技術の見直しを行い、大規模な実証試験を経て日本的技術としての確立を図った。基準化にあたっては原子力部(当時)が積極的に取り組み、54年に当社技術研究所で実施した日本原子力発電と関西電力とのPCCVの大型水平加力実験は、実証実験として世界的に著名な実験となった。
日本で初めてのPCCVは、52年に始まった日本原子力発電・敦賀2号機に取り入れられ結実した。当社は早くから三菱重工業とPCCVの利点につき討議し、42年から研究を始め、技術の蓄積を重ねてきた。これらを背景に、敦賀2号機の基本設計は米国ベクテル社が行ったが、三菱重工業に協力して許認可取得、実施設計の業務を原子力部、設計部、技術研究所が受けもった。これを母体として工務部門を加えて53年4月から55年3月まで敦賀2号機の実施プロジェクトとしてGT-2プロジェクト・チームが設置された。
PCCVは敦賀2号機のあと、関西電力の大飯発電所3・4号機、九州電力の玄海原子力発電所3・4号機と実績を重ねている。
注 PCCV:Prestressed Concrete Containment Vesselの略。
●免震・除振・制振技術
50年代に入って金融機関のオンライン化に伴い、大地震時における大型コンピュータの安全確保、機能保持の要請が高まり、その対応が課題となってきた。こうした情勢のなかで、51年、免震床「ダイナミック・フロア・システム」の開発、実用化が行われた。これは、3次元床免震構法、すなわち、水平は低摩擦材によるすべりと摩擦ダンパー、鉛直はコイルバネとオイルダンパーを組み合わせる2重床の免震技術であり、当時としてはまさに画期的な技術として、その後十数年を経て開花する免震・制振ブームの歴史的原点となった。また、施工実績は延約8万㎡(平成3年3月末現在)と、現在においても当社はわが国最大の圧倒的な実績を有し続けている。
同じころ、小さなマス(重量物)と鉄板でつくったバネによって機械振動を低減する制振技術「ダイナミックバランサー」の開発にも着手し、実用化した。そして55年には、除振技術として、精密機械工場建家本体の微振動対策検討用プログラム「V.I.P.」の開発に着手し、58年の完成以来、半導体工場や精密工学関連研究所など、数多くのプロジェクトでの微振動環境評価・設計に利用されている。
50年代後半から60年代にかけて、建物の安全性確保とあわせて 、居住性等の付加価値を一層高めようとの社会的要求から、高さ31m以下の建物の免震化、および比較的固有周期の長い(1秒以上)建物の中小地震・季節風時の居住性の改善を主眼として、建物制振技術の開発が各社競い合うかたちでスタートした。
当社は60年、大手ゼネコンのなかでいち早く積層ゴムを利用した免震ビル構法として、積層ゴム+鋼棒ダンパー、鉛入り積層ゴム、高減衰積層ゴムの3種のタイプについて日本建築センターの技術評価を取得した。そして、61年の第1号物件である当社技術研究所・ハイテクR&Dセンターをはじめとして、以後の科学技術庁無機材質研究所無振動特殊実験棟、東京都老人総合研究所ポジトロン医学研究施設、渋谷清水第1ビルの受注にこの技術はタイムリーに結びついていき、“売れる先端技術”の先鞭として社内外の反響を呼び起こした。
制振技術については、アクティブにマスダンパーを作動させるアクティブ制振システムや、水タンクを利用したパッシブ制振システムも開発、実用化している。
●省エネルギー技術
省エネルギー技術に関する当社の歴史は古い。石油危機の10年も前の38年に、ピンボード制御盤によるワンマンコントロール方式を導入した大阪神ビル(日本建築学会賞受賞)を皮切りに、48年には、屋内発熱を回収して暖房に利用したり、世界初の最適化予測制御を開発・導入した大阪大林ビル(日本建築学会賞、空気調和・衛生工学会賞受賞)など、数々の省エネルギービルを建設している。
その実績を買われて、49年にスタートした「サンシャイン計画{注1}」にも三洋電機と共同で参加し、52年、枚方ソーラーハウスを建設している。これは太陽エネルギーの有効利用を目指した一戸建住宅の太陽熱冷暖房・給湯システムを研究開発するためのものであったが、ここにも多くの省エネルギー技術が組み込まれていた。
こうした省エネ要素技術を組み合わせ、建築デザインと設備の計画をトータルに考えた省エネルギービルを実現したいという気運のなかで、技術開発委員会・省エネルギー委員会で、省エネのモデルビルの計画がもち上がったのは54年末のことであった。
当時の大型ビルの年間1㎡当たりエネルギー消費量は約450Mcal(メガカロリー)、日本で実際に稼働している省エネビルで241Mcalであったが、米国ではカリフォルニア州政府ビルで121Mcal/㎡・年を目標に着工したとの情報も刺激となり、世界一の超省エネビル建設にチャレンジすることになった。そのビルは当社の技術研究所本館、目標値は100Mcal/㎡・年であった。
ビルの省エネをトータルに実現するには、数多くの省エネルギー手法をきめ細かく検討し、全体を一つの整然としたシステムにまで組み上げなければならない。それは高度な総合エンジニアリング力を必要とする非常に難しい作業である。このためにコンピュータを駆使し、個々の省エネルギー手法の効果を定量的にとらえ、エネルギー消費量のみならず、建設工事費をも考慮することによって、省エネルギー手法の有効性を迅速、簡便に評価しうるプログラム「ENECOST」も開発された。
技術研究所本館ビルの建設に関しては省エネルギーのアイデア募集に多数のアイデアが集まったが、そのなかからその時点において実現可能なものを選び、さらに従来の省エネルギー手法も加えて、採用すべき手法の検討を重ね、98の省エネ手法{注2}が採用された。
こうして計画スタートから20カ月たった57年4月、同本館ビルが竣工したが、同ビルのエネルギー消費実績は一般事務所ビルのわずか4分の1の87Mcal/㎡・年という画期的な数値を達成した。建設費は約20%割高となったが、そのための余分の費用は、建物の法定耐用年数65年の7分の1強に当たる8.7年で回収され、以後は省エネによる利益が得られると試算された。
この建物は59年にASHRAE(アシュレー:米国暖房・冷凍・空調学会)エネルギー賞最優秀賞を米国以外の作品で初めて受賞したのをはじめ、同年、空気調和・衛生工学会賞、61年日本建築学会賞(業績部門)を相次いで受賞し、“省エネ技術は大林”の評判をとった。当社はその後も省エネ・新エネ技術開発として、コージェネレーション(熱と電力の同時供給)、氷蓄熱、風力発電、スーパーヒートポンプ等、この分野での技術開発に積極的に取り組んでいる。
注1 サンシャイン計画:通産省工業技術院の「2000年をめどにクリーンエネルギーを開発しよう」という計画。
注2 省エネ手法:そのなかには「ダブルスキン」の採用をはじめとする建築の断熱・日射遮蔽、通風に関する15の手法、「太陽熱利用や土中蓄熱」など太陽熱の能動的利用(アクティブソーラ)に関する5つの手法、「タスク/アンビエント照明方式」などを含む照明電力の低減のための11の手法ほかがある。
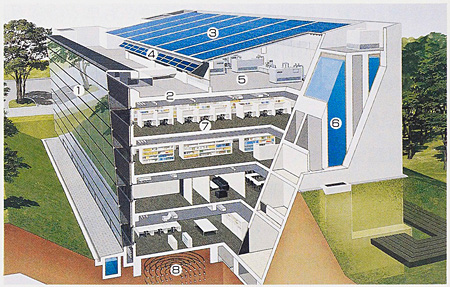
超省エネビル・当社技術研究所本館(昭和57年竣工)の断面パース
①ダブルスキン
②無梁版構造
③太陽熱コレクター
④太陽電池
⑤設備機械室
⑥蓄熱槽
⑦省エネルギー照明方式
⑧太陽熱土中蓄熱
地道な努力が奇跡的な効率を達成
竹内 均東京大学名誉教授は、技術研究所本館ビル建築の意義を『98メガカロリーへの挑戦』(当社製作パンフレット)の中で、次のように述べている。
「消費エネルギーが半分ですむといった工夫は、容易になされるものではない。これまでの2倍の効率のエンジンを作ったら、わが国のマスコミは一斉に、これを世界的な大発明としてとりあげるに違いない。わが国における火力発電の総合効率は約41%である。火力発電所の効率を、これの2倍の82%にあげることは、不可能といってよいことである。(略)
画期的な大発明ならぬ、地味な工夫の積み重ねが、奇跡的な効率をもたらす。1年でもとをとるといった華やかさを捨てて、長期的にみてはじめて経済性が理解されるといったいきかたをとる。この二つだけをとりあげても、それはこれからの科学や技術のゆくえを暗示するものである。象徴的にいえば、それは総合化でありまた成熟化である。
私はこれまで、省エネルギーや総合化をねらいとする第3世代の学問の重要性を、ことあるごとに強調してきた。今度大林組の作った超省エネルギービルは、私のこれらの主張のシンボルのように思えて、うれしくてならない。」
●サイロ貯炭技術
46年に導入されたスウェトー工法はスリップフォーム工法の一つであるが、技術の完成度がきわめて高く、多くの優位性をもつものであった。しかし、大型のRC塔状構造物のニーズはそう多いものではなく、そこで塔状構造の施設を周辺技術も含めて総合的に開発し提案することによってニーズをつくり出すことがこのころの技術開発の大きなテーマの一つとなっていた。公害防止に着目した内筒式超高煙突や自然通風式冷却塔がそれであり、この方面でも当社は実績を積んでいった。さらに50年代に入ると美観の面から、その特長の一つである二次曲面を生かしたつづみ型のシルエットをもつ大型の高架水槽も受注し始めた。
第2次石油危機直後の54年、IEA{注}の石油火力新設禁止宣言を機に石炭火力がにわかにクローズアップされ、多くの電力会社が環境に適合する貯炭設備の検討に取りかかった。これに応えてサイロをはじめとするクローズドタイプの貯炭設備の技術開発がプラントメーカー、ゼネコン入り乱れての競争となった。
当社は、スウェトー工法の用途開発の一つとして、石炭や鉄鉱石を対象とした超大型サイロの技術開発をすでに進めていたこともあり、いち早く55年には日立製作所と共同で新型払出し装置「Wコニカルシステム」を開発し実証実験を行った。これが評価され、56年に四国電力西条発電所で、日立製作所と共同でターンキーベースの受注に成功した。これは、火力発電所の本格的なサイロ式貯炭・混炭・運炭設備として初めてのもので、課題とされていた“詰まり”や“自然発火”を解消し、現在まで約10年間順調な稼働を続けており、完成技術としての評価を確立している。
注 IEA:International Energy Agency(国際エネルギー機関)。第1次石油危機の際に設けられた。
●クリーンルーム技術
クリーンルーム技術はアメリカのNASAで宇宙開発とともに発展し、産業界では電子工業はもとより、精密機械工業やバイオテクノロジー等、製品の精密化、高品質化や信頼性を高めるため、より高いクリーン度が求められるようになっていた。一方では、これまで利用されなかった分野でも利用が広まり、いまやクリーンルームは重要な役割を果たすようになってきている。
クリーンルームは大きく工業用クリーンルーム{注1}とバイオロジカルクリーンルーム{注2}とに分かれる。50年代後半をピークに当社は多くの施工実績を重ね、ここで蓄積された技術ノウハウに裏付けされたクリーンルームの総合エンジニアリング技術を開発してきた。
58年には技術研究所内に、換気回数を10回/h~540回/h変化でき、清浄度を“クラス{注3}0”まで自在にできる実験用の高性能クリーンルームを設置した。これにより、必要な清浄度を最も効率的に実現でき、かつ経済的なクリーンルームについてのエンジニアリング能力を一層高めることができた。
また、61年にはクリーンルームのリークテストで検査・測定を行うロボット「クリムロ」の開発も行った。
これらの技術とその後の開発の総合的成果として、平成3年には、1立方フィート中に0.1ミクロン以上の粒子が1個以下といった、世界で最高水準の大型超クリーンルーム(NECローズビル工場メガライン)を完成させている。
注1 工業用クリーンルーム:半導体製造、精密機械組立、薄膜・フィルム製造、ディスク・リードフレーム、磁気テープ製造、原子力施設など。
注2 バイオロジカルクリーンルーム:病院の手術室、無菌治療室、未熟児新生児室、食品加工・包装、医薬品製造、微生物・純粋培養実験など。工業用クリーンルームと異なり、さまざまな微生物を制御することが主目的の空間。
注3 クラス:米連邦規格で1立方フィート中の0.5ミクロン以上の微粒子の和が、たとえば1,000個なら“クラス1,000”となる。
●超高RC建築技術
40年代に登場した超高層建築は、S造で主に事務所ビルであったが、50年代後半から同じ超高層でもRC造による超高層住宅がブームを迎えていった。
こうした超高層RC建築に対する業界の動きに応じて、当社はハード、ソフト両面から研究開発を進めてきたが、その契機は43年の十勝沖地震であった。技術研究所を中心に、RC建物の耐震性の向上および高層化・超高層化施工の合理化を目指して、これら建物の耐震設計法の研究開発が行われた。
59年9月に設置された技術開発委員会第三専門委員会・RC超高層住宅小委員会のもと、高強度コンクリート(480kgf/㎠)の実物大の打設や、破壊実験による実証、50階まで設計可能なRC超高層一貫構造設計プログラム「STREAM-H」「STREAM-Z」の開発、内部吹抜け型超高層住宅の風洞実験、超高層住宅コンペ出品なども精力的に行ってきた。
こうした成果が、営業努力と相まって民活第1号の東京新宿・西戸山タワーガーデンに結びつき、さらに61年末、大阪・桜之宮中野地区都市型集合住宅プロジェクト開発設計競技で最優秀賞を得て、住宅としては日本一の高さの超高層RC集合住宅、桜宮リバーシティ・ウォータータワープラザ(RC造、地下1階、地上41階、塔屋1階、延4万7,114㎡)を手がけることとなった。